What Makes Laser Cutting Ideal for Metal Parts?
Laser cutting metal parts is an ideal solution for projects requiring high precision with flexibility in manufacturing. Being part of the laser manufacturing world, ideally, I would like to see as many metal parts as possible made from this technology. That makes great business sense to me and of course competition can be fierce so providing the best quality and service possible are aspects every laser manufacturer strives for. The demand for precision cut components that encompass tight tolerances and surface roughness characteristics that are within the required specifications is a challenge for any method, including CNC Milling, waterjet cutting, and metal stamping. There is no one in providing custom metal components in use today that covers all design parameters that come forward, but there are factors that laser technology is ideal for in manufacturing high precision metal components such as:

- Flat 2D is Key: Laser cutting is a great method for producing flat, 2D profiles. The process is non-contact and produces some of the finest geometries. Other laser systems specialize in cutting tubes and stents, and are highly specialized for that purpose. Using small beam diameters results in sharp walls with smooth radius.
- Handling of Those Tough Thinner Gauges: You would not think that cutting thin metals foils is challenging, but it is. Since laser technology is a non-contact process, thin metal foils are not damaged by excessive pressure. Mounted metal can be torn, and stamped foils are easily damaged.
- Taking On Low and High Volume: The flexibility of laser manufacturing allows for processing of small quantities, but the capability to ramp up to high production without the need for tooling.
- Ease Of Manufacturing: Cutting of metal components needs really two elements; the CAD data and the metal alloy to be cut.
- All Those Iterations: Laser cutting is a go to method for Prototype and R&D support. Often the need for multiple iterations is done on the same sheet of material, without additional cost.
- Rapid Response and Execution: Without the need for tooling and excessive set-up, precision laser cut components can be done rapidly. Knowledge of the project’s needs and purpose are important for both the customer to convey and manufacturer to understand.
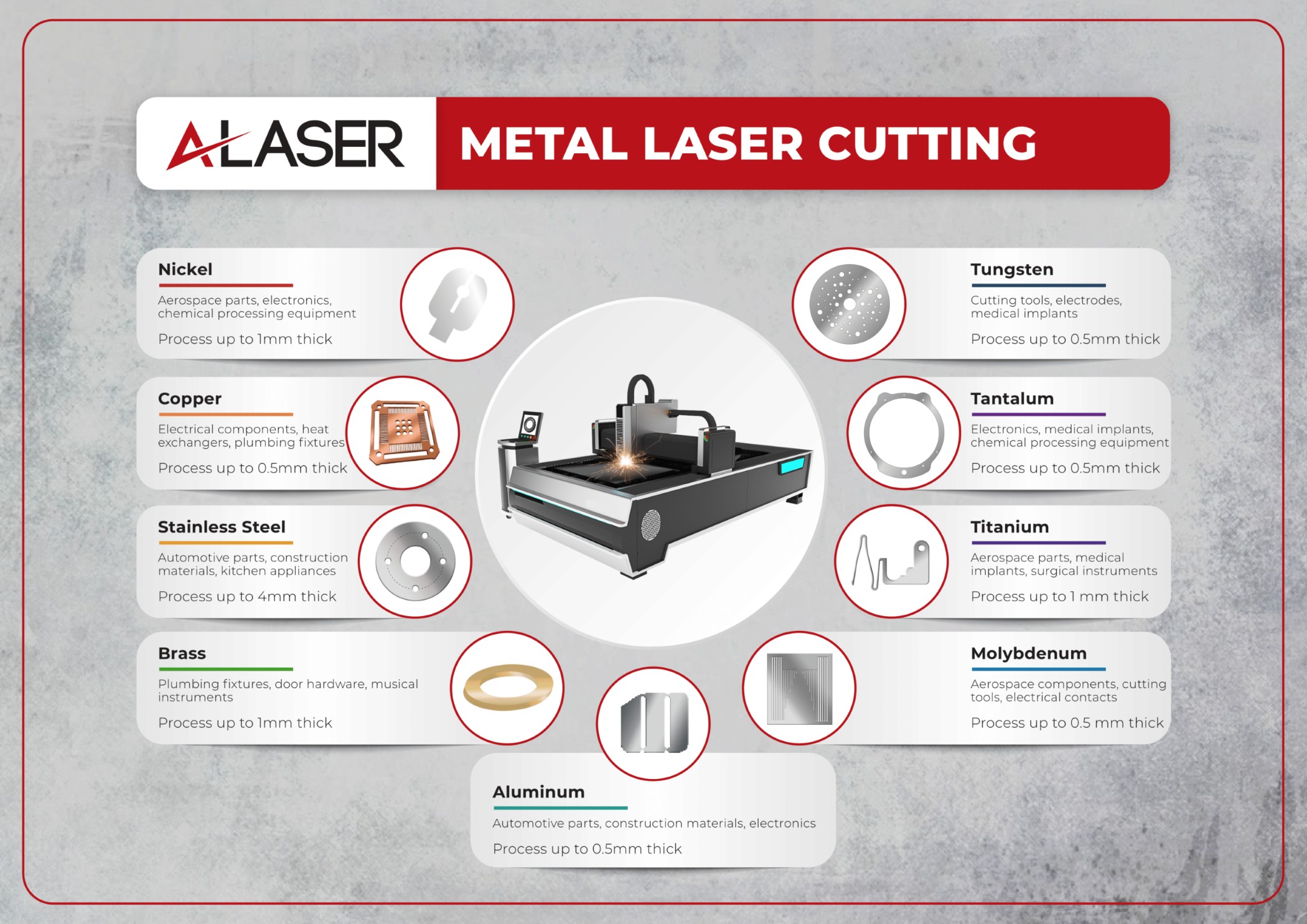
The Real Deal
The best attributes for using laser cutting technology of metal parts can be seen in real projects as for example a brazing service provider. The need for gold/copper alloys cut into specific shapes would be then go through the brazing process by the customer. The handling of such delicate foils could not be cut accurately by hand nor by any other means. Reaching out to laser specialists, the challenge was met and helped the customers grow their brazing business. For the medical industry, companies specializing in diagnostics have critical and demanding requirements. The project came forward to support R&D and prototype work, with the intention of ramping up once passed in clinical trials. Working with the medical device industry, it is common for any new product to take several years or more before final FDA approval is given. The solution given by laser technology was a great fit resulting in a recurring and successful venture. Another great example is from the adhesive dispensing industry. Laser cutting of various thicknesses of stainless steel, from 8mils to 20 mils thick, with consistency and tight tolerances of +/- 0.0254mm, made the dispensing of adhesives accurate. The metal components formed a series of nozzles, each being almost identical to each other. This was a critical parameter for a successful product. These few noted examples are a microcosms of how laser cut metal parts has been a part of improving technology and opening new doors with new solutions.
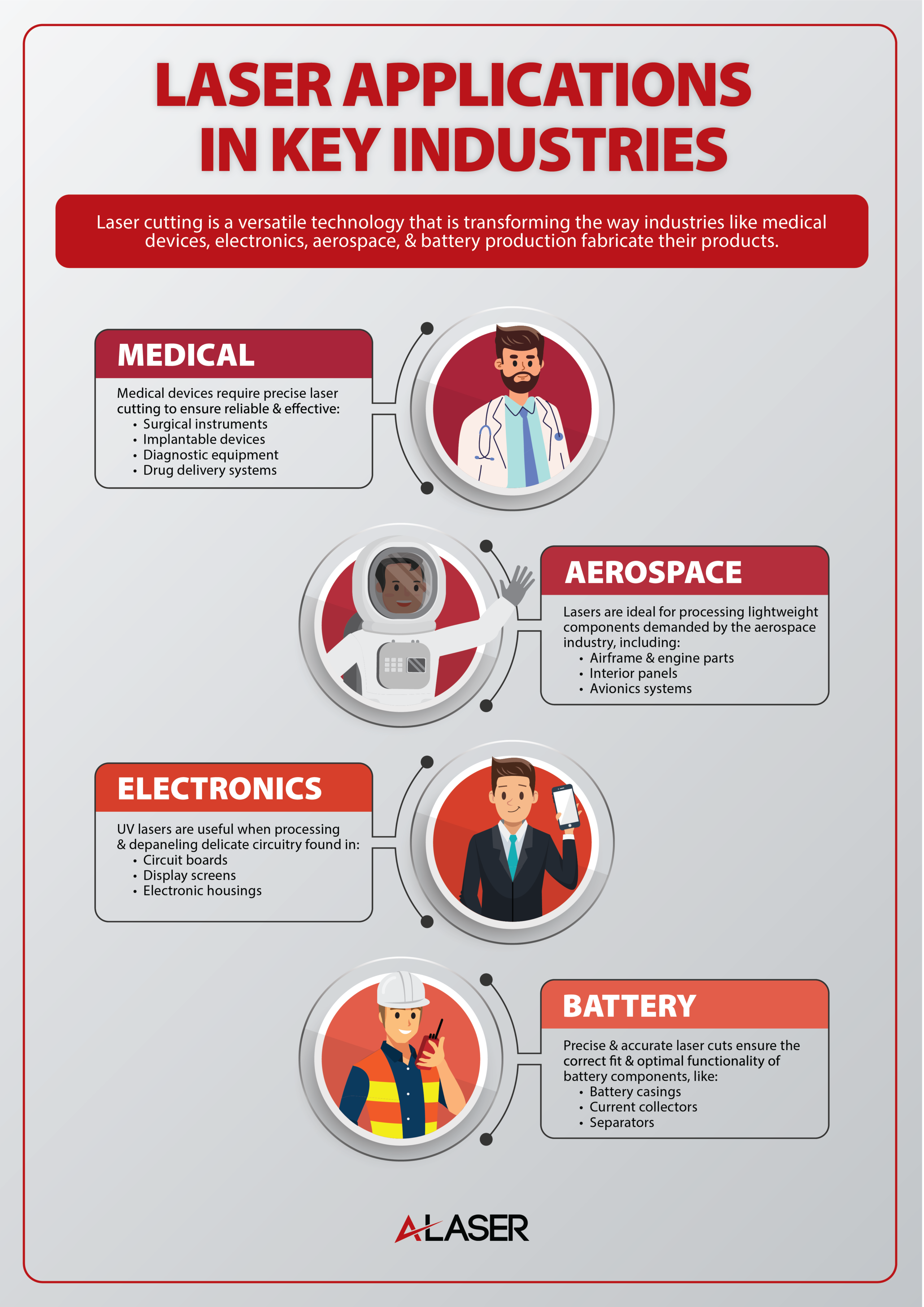
In conclusion, the success of laser cutting technology for metal parts lies in its ability to deliver precision, flexibility, and efficiency across various industries. The non-contact nature of the process ensures the integrity of delicate materials, while the capability to handle both low and high volumes without extensive tooling makes it adaptable to ever-changing production needs. The proficiency in producing intricate 2D profiles and managing thin gauges adds to its versatility. Laser cutting’s rapid response and execution capabilities further enhance its appeal, making it an indispensable method for both prototype development and high-volume manufacturing. Ultimately, the collaboration between knowledgeable laser specialists and their clients is pivotal in achieving excellence, leading to the growth and innovation in fields such as medical diagnostics, semiconductor manufacturing, textiles, clean energy and many more.