Laser cutting difficult materials and shapes are challenges that are solved by years of experience with qualified service providers. Even seemingly simple shapes such as washers or gaskets can require multiple resources due to new materials or stringent tolerances of the geometry. This flexibility with laser processing solutions makes the technology highly desirable for many established companies and new start-ups. The pursuit of excellence in product development creates challenges for every form of manufacturing. For innovation to take place, obstacles in material properties and geometric form can open doors to manufacturing that were previously never considered. This is a great benefit that laser manufacturing has taken advantage in support of precision manufacturing and micromachining. Not every project of course is in need for in-depth collaboration between a laser service provider, customer, and material source, but when they do occur, the results can be very rewarding.
Challenging Projects
Materials come in a wide variety of chemical formulations that can cross over to many industries, like stainless steel or aluminum, or rubber-based products, for example. There are others that can be more specific to applications like graphene for gasketing components or polyimides for their electrical and thermal insulating properties. The ideas coming forth from new developing technologies really are what keeps laser cutting service providers active in providing high quality with efficiency and repeatability for new and challenging jobs. The following examples will give a clear understanding of some of the most challenging projects and the solutions that were developed:
The FR4 Challenge: FR4, which is a composite material used widely for the fabrication of printed circuit boards, is often routed and depaneled by mechanical means such as CNC routers and CNC Mills. A project was designed for the paring of two circuit boards to have interlocking fingers, that would allow for precise function of the intended device. However, while the interlocking fingers were necessary, they were not designed to withstand the rigorous forces that a CNC cutting can inflict on materials. The delicate fingers were about 2.5mm wide by 1.5cm long. They kept breaking during the CNC process.
Laser Solution: For cutting FR4, UV or ultraviolet laser technology is a great choice, especially for profiles that are intricate or delicate, as in the “fingers boards” project. Laser cutting is more accurate than the processing of arrayed circuit boards, so the first step was to determine the cutting sequence. This would give the best accuracy for each cut board. The next step was to dial in the laser parameters of cutting speed, power, and dwell time to cut desired outline. The cut edge required minimal to no HAZ or heat effect, while holding a tolerance of +/- 0.0508mm. Further recommendations to process additional PCB panels at a smaller size and with the addition of more local fiducials made the project a production success. The broader tolerances most PCB projects have do not necessarily require high precision cutting, but when those do occur, laser technology has proven to be of great value.
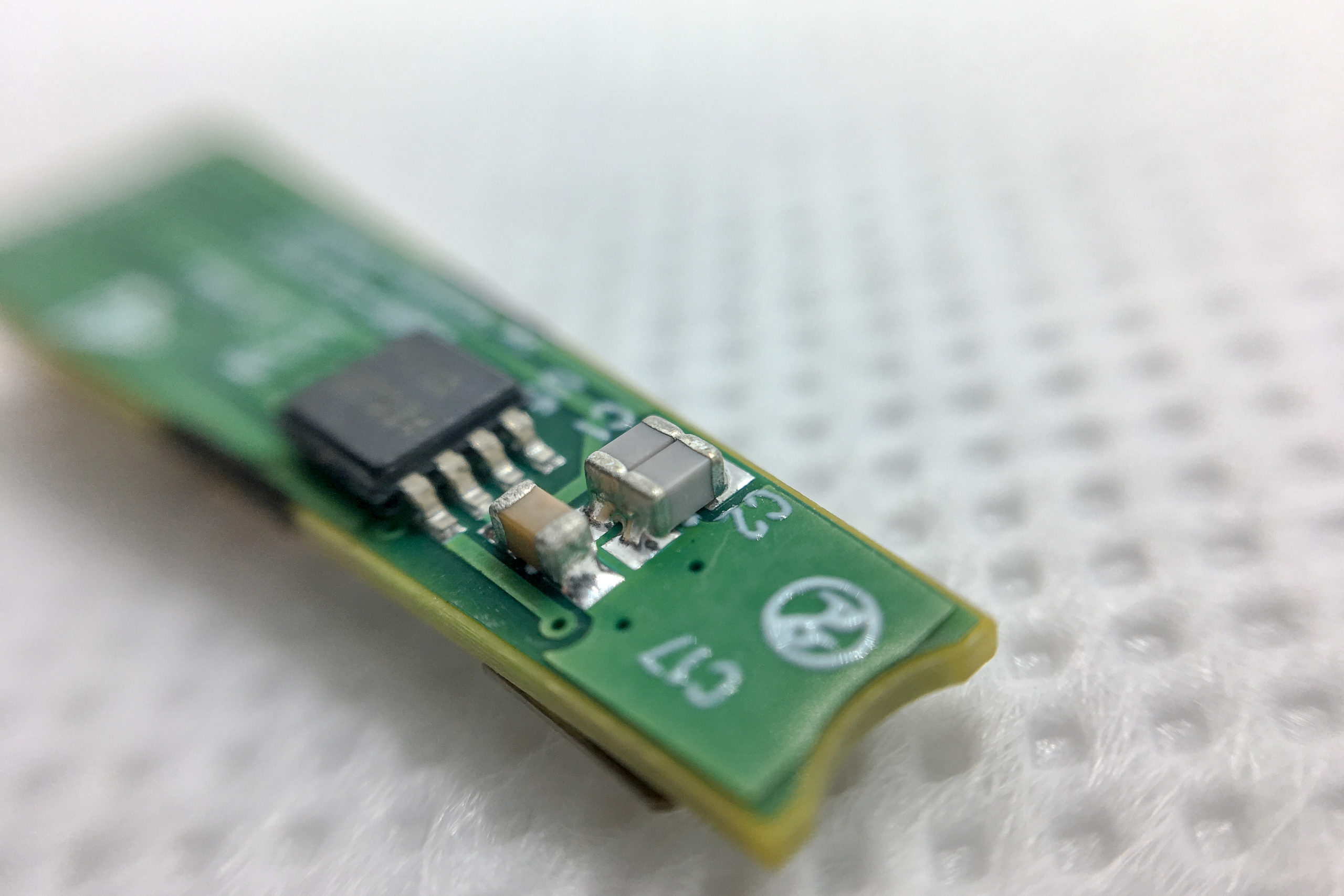
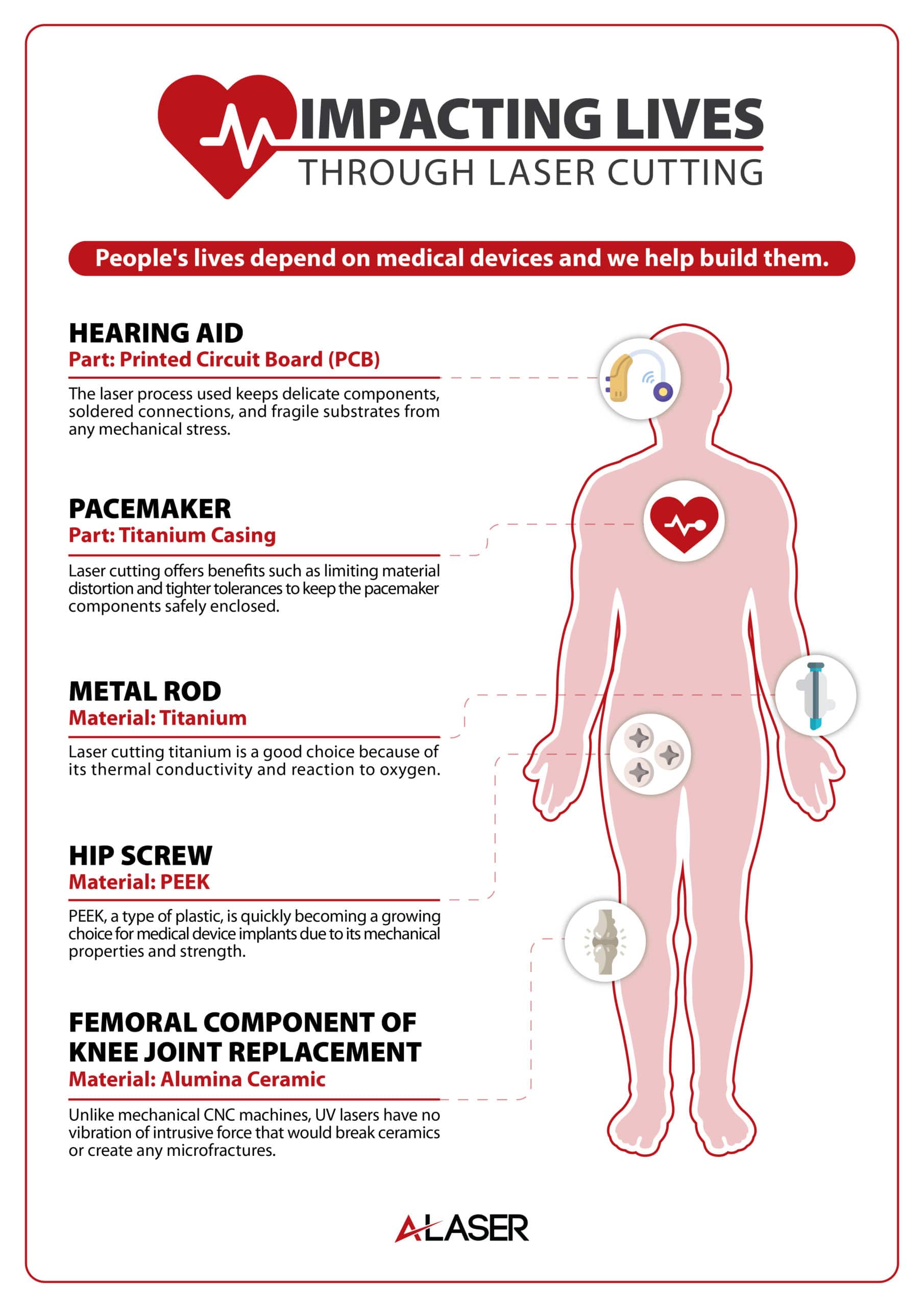
Medical Micro Assemblies: Stainless steel is a versatile material used by almost every industry you can think of. Its strength to weight ratio and resistance to corrosion gives it the edge for many devices and applications. For the medical industry, stainless steel is common and continues to be a key part of medical advancements. One particular project required a designed mechanical assembly of a cartridge that would house micro staples that would be used by this mechanism to staple arteries in place and by doing so, reducing a patient’s recovery time. Methods such as stamping would not produce the straight wall edges needed. The stainless steel was too thin for CNC methods to cut with out damage. It was the versatility of laser cutting technology that created the solution.
Laser Solution: These cartridges and supporting parts were all made of stainless steel from thickness of 8, 10 and 15 mils with tolerances from +/- 0.0254mm to 0.0127mm in some key and critical points. Laser parameters adjusted for both ultraviolet and infrared systems, with a high degree of inspection. Additionally, to achieve this accuracy a collaborative effort was made between the material supplier, laser cutting provider, and a secondary laser welding service. These mechanisms needed to work flawlessly which added additional post processing of deburring and polishing. Each step underwent inspection and approval before a final completed assembly was approved.
More Challenges At a Glance
There are countless projects we can portray that laser cutting is challenged with. This is a recuring aspect of the business and often the most rewarding for manufacturing. Once one obstacle is overtaken, it does give laser services providers the edge for doing similar difficult tasks. The following list is a quick view of other challenging materials and designs that were encountered and how completed:
- Alumina Ceramic Components: Very fragile and brittle. Using ultraviolet lasers for thicknesses below 0.254mm and fiber lasers for thicknesses above 0.254mm. Laser parameters such as speed, power and dwell time are controlled for both systems to prevent cracks and fissures. The non-contact systems that lasers have, prevents marring ad surface scratches.
- Flexible Two Stage Epoxy: Used as seal and gasket for aerospace antennas. Processing on UV lasers for accuracy of +/- 0.0254mm. Process included developing packaging to seal the gaskets and prevent damage during shipment. Adhesives are also applied to metallic and non-metallic materials and cut to provide single use parts or left intact on full sheets, by “kiss” cutting methods that control the laser parameters to cut through the material and adhesive, but not trough the backing liner.
- Battery Technology: Nickel is used widely in battery designs, but it is soft and challenging to create profiles with sharp clean edges in thickness of 5-8mils. Using the non-contact laser technology, extremely accurate profiles support new emerging designs. Handling of nickel foils and sheets must be taken to prevent damage pre and post laser. As a highly reflective metal alloy, laser parameters are controlled and monitored during the cutting process.
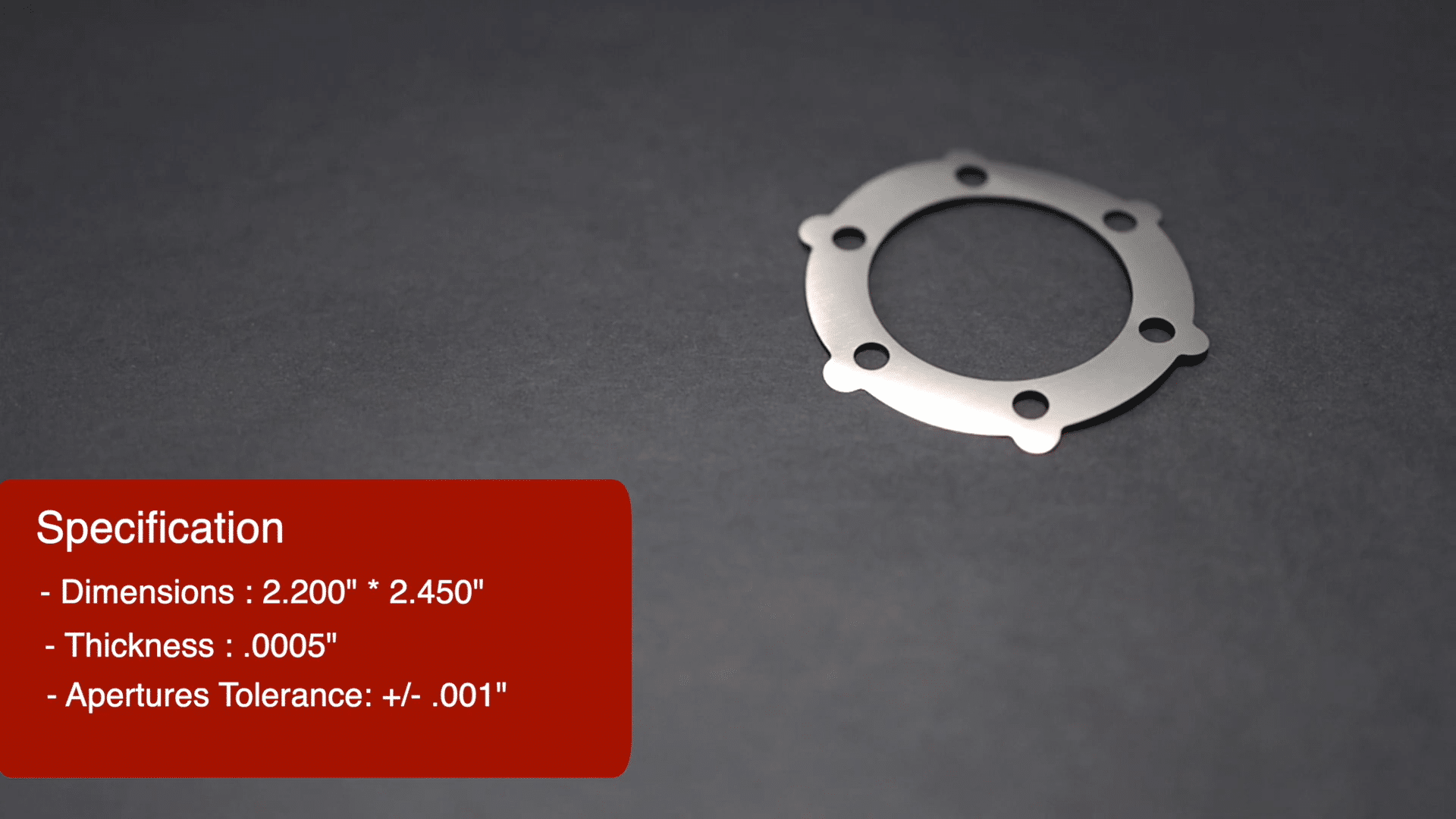
- Brazing Alloys: Costly brazing alloys are designed with delicate and challenging profiles. These cannot be die-cut nor stamped without damaging the foil. Laser cutting solves this with the material being held in place by vacuum. Parameters adjusted to minimal to no heat affect or HAZ.
- LIDAR Challenge: Lidar sensor assembled on FR4, printed circuit panel array. Needed systems to support volume production. Traditional routers damaged the sensitive lasers on the boards. Laser cutting was the only solution to adhere to the stringent requirements of tolerance and function. Each profile needed to be exact to fit inside protective housing.
- Polyimide Mesh Screen: Polyimide is a tremendous material, used by countless industries because of its electrical insulation properties, high thermal threshold and flexibility. One project needed a mesh screen out of 1mil polyimide for an advanced electronics device. With 10mil wide struts and 30mil square openings, this challenge needed the laser parameters adjusted to cut with no heat affect to an accuracy of +/- 0.0508mm over the array. A developed system to cut the polyimide on a PTFE porous base kept the material flat and an inspection system adjusted to measure accurately without damaging the completed screen.
Conclusion
Laser technology stands out as a remarkable tool in the realm of manufacturing, providing a definitive edge when it comes to designing intricate profiles from troublesome materials. Unlike traditional methods that often struggle with precision and quality control, laser cutting difficult materials and shapes is a proven method offering unparalleled accuracy, consistency, and flexibility. Its non-contact nature ensures minimal damage to delicate substrates, making it ideal for applications where other processes fall short. By harnessing the capabilities of advanced laser systems, manufacturers can tackle complex projects with confidence, knowing that the results will meet stringent specifications and enhance the overall functionality of the final product. Ultimately, laser technology not only overcomes the challenges posed by difficult materials but also sets a new standard for excellence in modern manufacturing.