Stainless Steel Mesh
For some of us stainless steel mesh may be one of those materials we rarely think about. Learning more about it, I found that it is used in so many industries with very specific applications. From my experience in manufacturing precision parts with lasers, we do see projects come in from time to time using stainless steel mesh, but on a smaller scale.
Stainless steel mesh can be made from many different grades including 302, 304, 316, 316L. 316L has better corrosion and abrasion resistance. From this there is two basic types of mesh created: Welded stainless steel mesh and stainless steel wire mesh. Welded mesh has great strength as each intersection is welded. It gives the mesh high rigidity and can withstand harsher conditions and applications. It can give architectural uses for being clean facets and having repeated patterns. Its strength can be great for railings throughout many industrial facilities. Oil and gas and pharmaceutical industries will use it to filter out impurities. Agriculture can use this also for barriers and shelters.
Stainless steel wire mesh, unlike its welded counterpart, is woven. This weave can vary dramatically due its intended use. Often the material is made with chromium and nickel giving more resistance to corrosion but added strength and used in many of the same applications of the welded mesh. What we do see is the difference between the way the mesh is created. A larger diameter of wire will result is a greater diameter of the mesh. This is best for use both in aesthetics and function.
We all must eat and in the world of the food industry, from processing to restaurant use, food grade stainless steel mesh is made. It is best suited being made from 316 stainless steel rather than an alloy like 304 which can corrode from the salt.
Stainless steel mesh seems to have found a rightful place in our lives. I see it now in my home as strainer in the sink. Researching thoroughly on what mesh would be best for your project by collaboration with the experts who manufacture these materials is key.
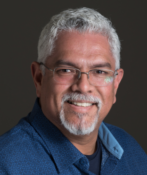
About the Author
Joe has been part of the A-Laser team for over 10 years and has extensive experience with laser cutting technology, sales, and customer service. Joe was born and raised in San Jose, CA and has resided with his family in Gilroy, CA since 1997. The unique projects he gets to learn about and the industries they support, keep everyday new! His hobbies include photography, he is a member of the Morgan Hill Photography Club, hiking, model building and collecting vintage camping lanterns and stoves. His favorite places include Mount Lassen Volcanic National Park, Portland OR, and Boston MA.