What Machines Are Used?
What is a plastic cutting machine and what is it used for? That’s a question and deserves further insight into a growing manufacturing method. A plastic cutting machine is a precision tool that utilizes technology to cut, engrave, or mark plastic materials. These technologies offer exceptional accuracy and detail, making them ideal for a wide range of applications, from prototyping to mass production. Systems used today are controlled by computer software, allowing for intricate designs and complex shapes to be created with ease. Plastic itself has been around for many decades now and through its history, has benefitted technological growth in all industries but also carried along controversy on its use and impact on the environment. That itself applies to numerous manufacturing methods and materials and all of us will weigh what we feel impacts ourselves currently in positive ways or perhaps can lead to discussions on alternatives. Today, plastics impact so much of our lives in positive ways that the need for continued manufacturing support seems endless. The technology available to manufacturers transforms plastics into precision components for industrial uses and countless applications such as for medical uses and devices, for consumer electronics, for aerospace and military applications. We rely on these technologies in producing plastic parts for everyday uses and benefit from its versatility in form and function.
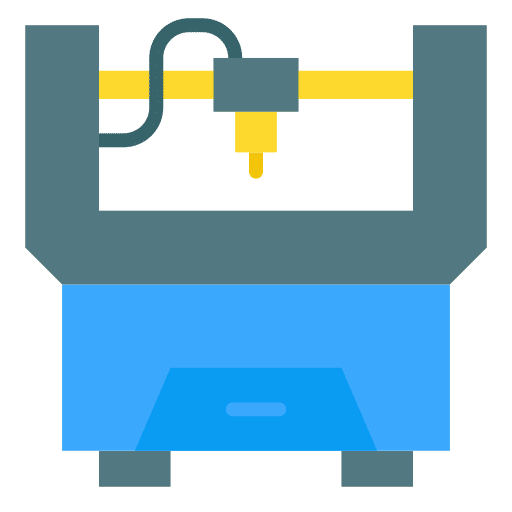
Cutting Plastic Technologies
The world of plastic cutting machines is incredibly diverse, offering a range of technologies to suit various applications and material types. Popular machine systems are:
Machine Type | Characteristics | Tolerance* |
---|---|---|
CO2 Laser | Good for clear plastics. | +/- 0.025mm to 0.127mm |
Ultraviolet Laser | Precise, good for thin plastics and metals, minimal heat affect. | +/- 0.025mm for many projects up to +/- 0.076mm |
Picosecond Laser | Short pulse rate-No HAZ(heat affected zone), thin plastics and materials. | Depending on project specifics can be as low +/- 2-5nm |
Femtosecond Laser | Extremely short pulse rate. No HAZ(heat affected zone). Ultra-thin plastics and other materials. | Depending on project specifics can be as low +/- 2-5nm |
Waterjet Cutting | Thicker materials, intricate shapes, minimal HAZ. | +/- 0.050mm to 0.100mm for many projects |
CNC Technology | Versatile, 2,3,4 and 5 axis. Cost efficient for high volume manufacturing. | +/- 0.050mm to 0.500mm |
Plasma Cutting | Cuts through thicker materials. Fast rate. Multiple materials. | +/- 0.250mm |
Importance of Tolerance and Quality of Cutting Plastic
*Tolerance is affected by numerous variables including material, thickness of material, geometry, environmental conditions, quality required, HAZ(heat affected zone). The above tolerances are generalized for comparison.
Tolerance expectations are paramount for many projects. Factors like material properties, machine precision, and cutting parameters significantly influence the achievable accuracy. Laser technologies, renowned for their precision, excel in producing intricate details with minimal heat-affected zones. CNC machining, while versatile, may require more stringent tolerances for certain applications. Waterjet cutting and plasma cutting, often used for larger-scale production, typically offer coarser tolerances. Some cutting machines will have internal systems to check the tolerance and geometry, but many companies wishing to undertake high precision projects and work with industries like medical device, defense, and aerospace, will get certified under ISO 9001 series, for example. Under such certification a QMS or Quality Management System, is put in place and defines processes and procedures for scheduling machine maintenance, materials control, and calibration of measurement devices, amongst others. Ultimately, understanding these factors and selecting the right technology is crucial for achieving the desired level of precision in plastic cutting operations.
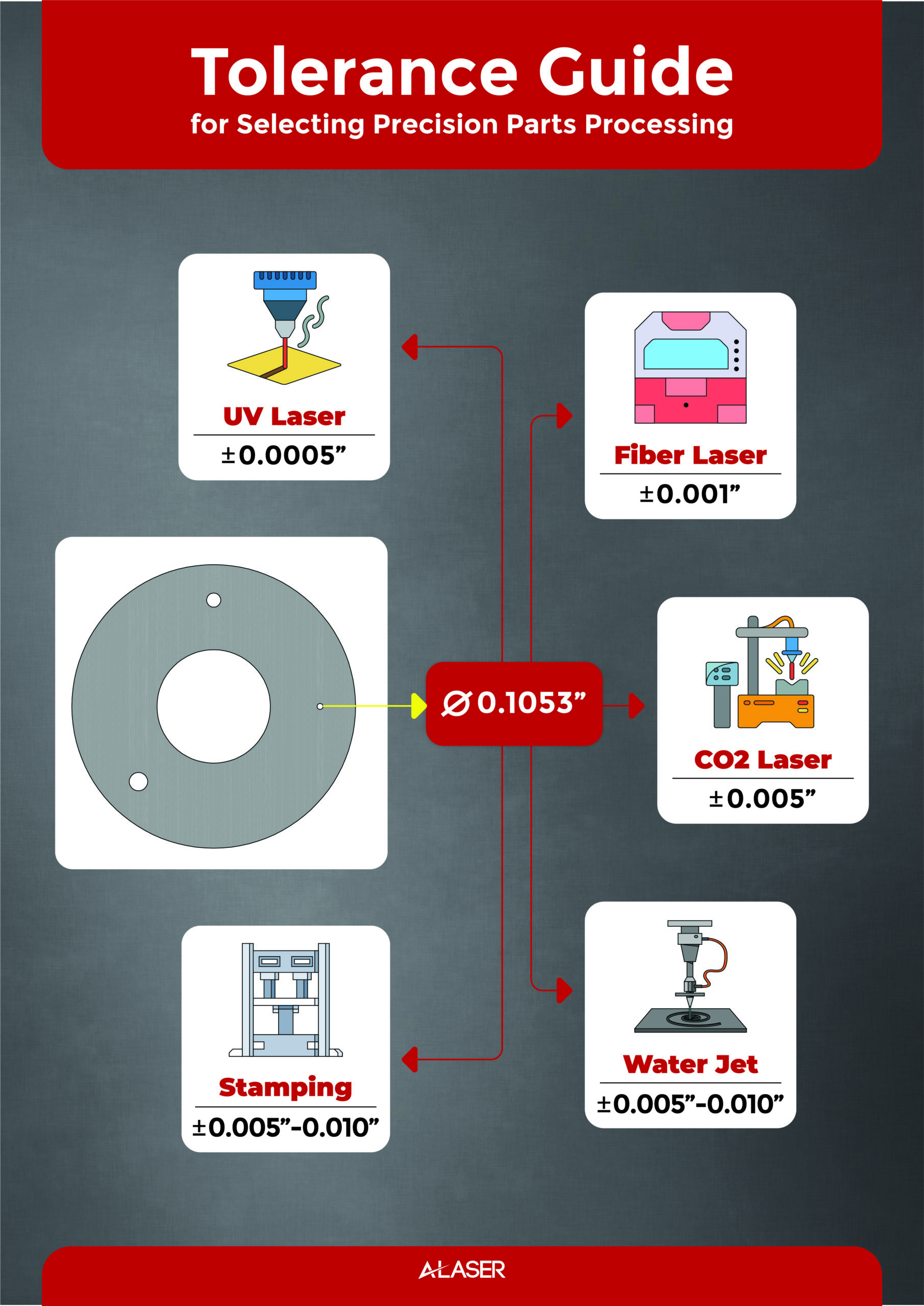
Plastic Cutting Technologies-Cost Considerations
The cost of plastic cutting technologies can vary significantly depending on several factors, including initial investment, setup costs, maintenance cycles, longevity, repair costs, and training requirements. Here’s a brief cost comparison of the major technologies:
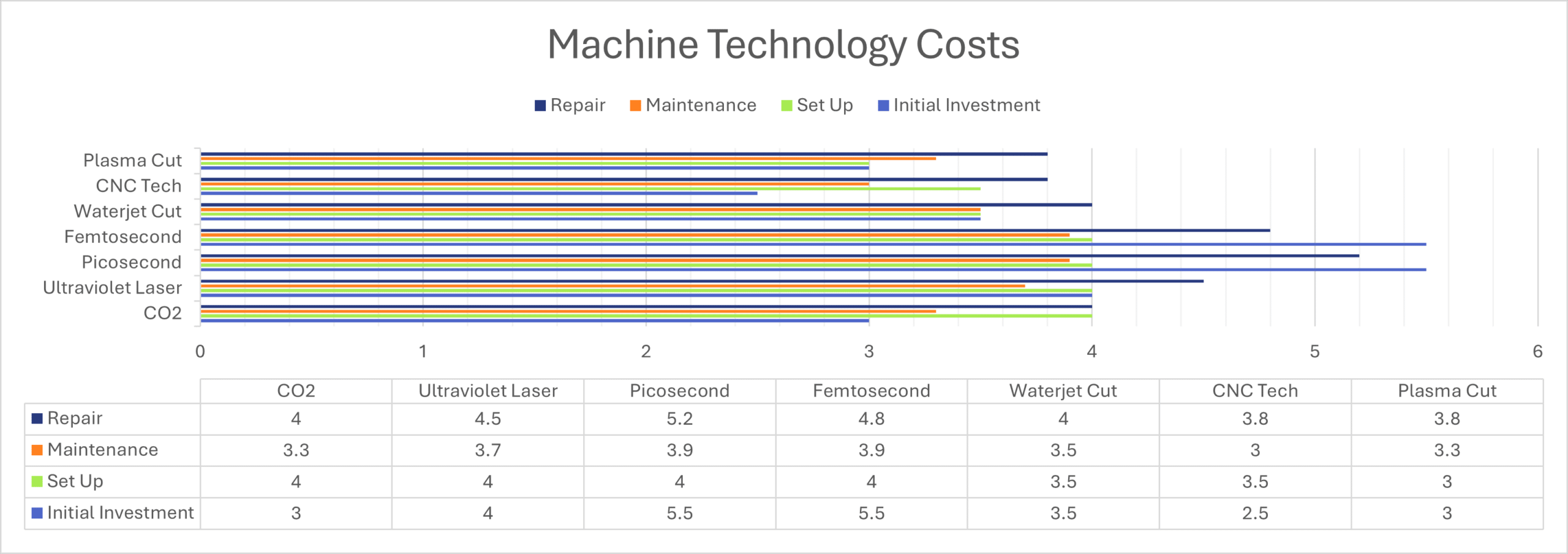
In conclusion, the overall cost of plastic cutting technology depends on a combination of these factors. Manufacturers should carefully evaluate their specific needs and budget to determine the most cost-effective option for their application.
What Machine Is the Best for Cutting Plastics?
The choice of technology depends on several factors, including the material’s properties, desired precision, production volume, and cost. Manufacturers may choose plasma cutting for its speed and efficiency, waterjet cutting for its versatility, CNC machining for its flexibility, or laser technologies for their precision and clean cuts. Some plastic cutting projects may need to use the resources of different systems to complete the project. For example, a project requiring Peek or polyimide at thin gauges of 0.0127mm will be supported using ultraviolet technology. In addition, other parts of the project may require ABS plastic or acrylic, that are thicker and best processed by CO2 laser technology. Perhaps this completed assembly is placed in a housing of polycarbonate that is machined through CNC technology. Ultimately, the ideal technology or technologies will be selected for meeting the specific requirements of the application.
Impact of Plastic Cutting Technology
Plastic cutting machines create their magic behind the scenes. These precision tools are the unsung heroes, shaping everything from the delicate lenses of our eyeglasses to the critical components of medical devices. In the realm of medicine, plastic cutting machines enable the creation of life-saving implants, prosthetics, and surgical instruments. In the consumer world, they bring us durable and stylish products, from the sleek smartphones in our hands to the comfortable furniture in our homes.
Beyond these familiar applications, plastic cutting machines also play a pivotal role in driving innovation and growth across various industries. In the optics industry, they help craft high-precision lenses for cameras, telescopes, and microscopes, expanding our understanding of the world. In the aerospace industry, they enable the production of lightweight and durable components for aircraft and spacecraft, pushing the boundaries of exploration. And in countless other sectors, from automotive to electronics, plastic cutting machines are essential for manufacturing the products that power our economy and enrich our lives.
Cutting plastics, especially for precision components, has transformed over the past decades to support leading edge technologies. The methods of forming plastics through molding and vacuum forming do provide industries with high quality products, but these technologies are limited when finer precision is required. When considering methods to cut plastic materials keep these in mind:
- Laser cutting technologies is ideal for precision and intricate designs.
- Waterjet cutting is excellent for thick materials and heat-sensitive materials.
- CNC technology offers versatility and precision for various applications.
- Plasma cutting is suitable for thick materials and high-volume production.
Manufacturers will choose the technology that best meets their specific requirements based on factors such as material properties, desired precision, production volume, and cost. The best source of information is to contact a precision manufacturer about your project and discuss what
options are available and determine the best course to achieve the desired outcome. Plastics provide benefits such as cost, reliability, strength to weight ratio, aesthetics and can be made in a host of custom colors. Machining these materials itself has advanced through the past 40 years and includes mechanical processes like CNC to laser cutting technology. As new methods of recycling plastic materials are developed, there does seem to be a greater collaboration between consumers, manufacturers and environmentalists to understand the needs of today while creating a better system for processing to keep tomorrows future bright.