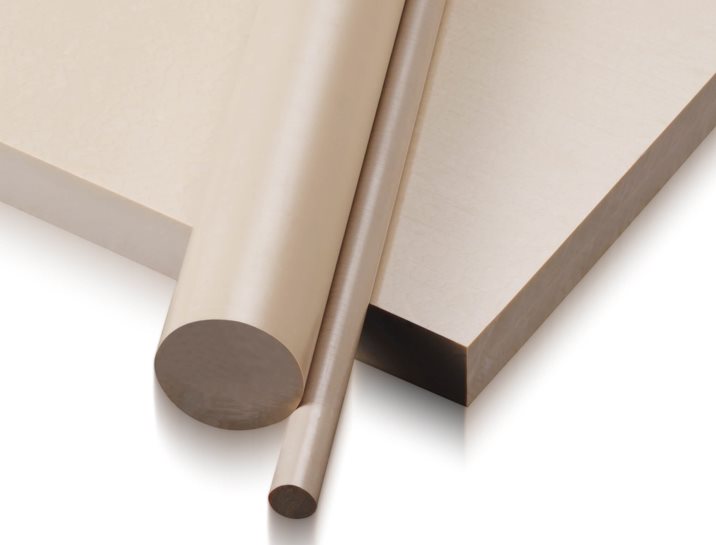
Introduction To the World
Our level of care from dental prosthetics to orthopedic implants would be greatly diminished if not for the valuable uses that PEEK provides. PEEK is a colorless polymer and has characteristics as being durable, with high heat threshold with chemical and electrical resistance. The journey of PEEK begins in the realm of molecular chemistry, where an orchestration of reactions transforms simple precursors into complex chains of polyetheretherketone. These chains, meticulously aligned and interconnected, form the crystalline structure that infuses PEEK with its remarkable strength and resilience. From this molecular transformation, PEEK emerges as a versatile material, that is made into rods, sheets, and pellets – the raw forms awaiting skilled manufacturers to be transformed into precision components that will serve in the most demanding environments. From the depths of the ocean to the vast expanse of space, components made from PEEK utilize the semi-crystalline structures that are durable with biocompatibility for medical uses as well as aerospace and electronics just to name a few. Matching PEEK with the medical and dental industries is just a glimpse of the impact this material has made over the past few decades. It was introduced around 1978 and used first in defense applications. Since 1981, PEEK has been a trademark of Victrex Corporation and has proved to be an extremely reliable material for electronics, medical devices, aerospace, automotive and many other vital applications.
Producing Raw Peek
PEEK, like other industrial materials, must be processed first in raw forms to be available for various manufacturing methods of plastics. An overview of this process is as follows:
- Step-Polymerization: Polymerization is a process in which small molecules known as monomers combine chemically to produce a very large chainlike or network molecule, called a polymer. For PEEK, the monomers form to create high molecular weight polymers.
- Extrusion: After polymerization, the PEEK resin is typically extruded into various forms of sheets, rods, or pellets, and blocks. Extrusion involves heating the resin and forcing it through a die to create the desired shape, and thickness of the desired raw form.
- Manufacturing of PEEK Components: There are numerous ways PEEK can be manipulated into precision shapes and components such as injection molding, compression molding, laser cutting, waterjet cutting, CNC machining, and die-cutting. Each method listed will have raw forms of PEEK it uses in its manufacturing process.
A Game Changer for Industries
PEEK has incredible strength and rigidity, rivaling even some metals. This allows it to withstand demanding environments, making it ideal for applications like aerospace components and heavy machinery parts. With outstanding chemical resistance PEEK is virtually inert to most chemicals, including acids, alkalis, and solvents. This makes it invaluable in industries like oil and gas, where components are exposed to harsh chemicals. PEEK can withstand high temperatures without losing its mechanical properties. This characteristic makes it suitable for applications in aerospace, automotive, and even food processing where equipment operates at elevated temperatures. The biocompatibility that PEEK exhibits is well-tolerated by the human body. This makes it a prime choice for medical implants, such as spinal discs and artificial joints, minimizing the risk of rejection and complications. Furthermore, PEEK can withstand high levels of radiation, making it suitable for use in nuclear power plants and medical equipment that utilizes radiation. PEEK is a space age material but not regulated to exploration beyond our planet, but in actuality helps advance technology in industries well known to those more obscure, but as equally important.
Diverse Applications
PEEK is made in raw forms of rods, tubing, sheets, and blocks. From these forms, manufacturing techniques like laser cutting, die-cutting, CNC Milling, waterjet cutting and others, are used to manufacture varying components supporting a vast collection of applications, that continues to grow as technologies arise and or new applications open. PEEK’s unique combination of properties has led to its widespread adoption across a vast array of industries:
- Aerospace: Aircraft engine components, landing gear, and structural parts.
- Automotive: High-performance engine components, gears, and bearings.
- Oil & Gas: Deep-sea drilling equipment, valves, and seals.
- Medical: Spinal implants, artificial joints, surgical instruments.
- Electronics: Connectors, circuit boards, and semiconductor manufacturing equipment.
- Food Processing: Food processing equipment, conveyor belts, and packaging materials.
This information highlights just some of the ways PEEK is found to support very important sectors of manufactured goods and services.
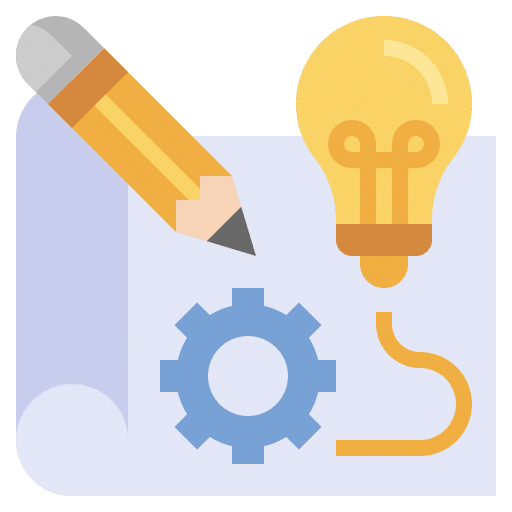
Why Choose Peek?
The properties of PEEK material as mentioned earlier of strength, durability, high temperature threshold, and biocompatibility, result in benefits by using this material such as:
- Ease of Machinability: PEEK can be manufactured by different methods depending on the type of component being produced. This versatility opens the door for the creation of complex and intricate components.
- Improved Reliability: Due to its consistent performance under extreme conditions, PEEK parts have long lifespans.
- Reduced Maintenance Costs: Have a great track record for performance and reliability, does reduce costs for assemblies and systems that use PEEK parts.
- Increased Efficiency: Due to its lightweight and high-performance characteristics.
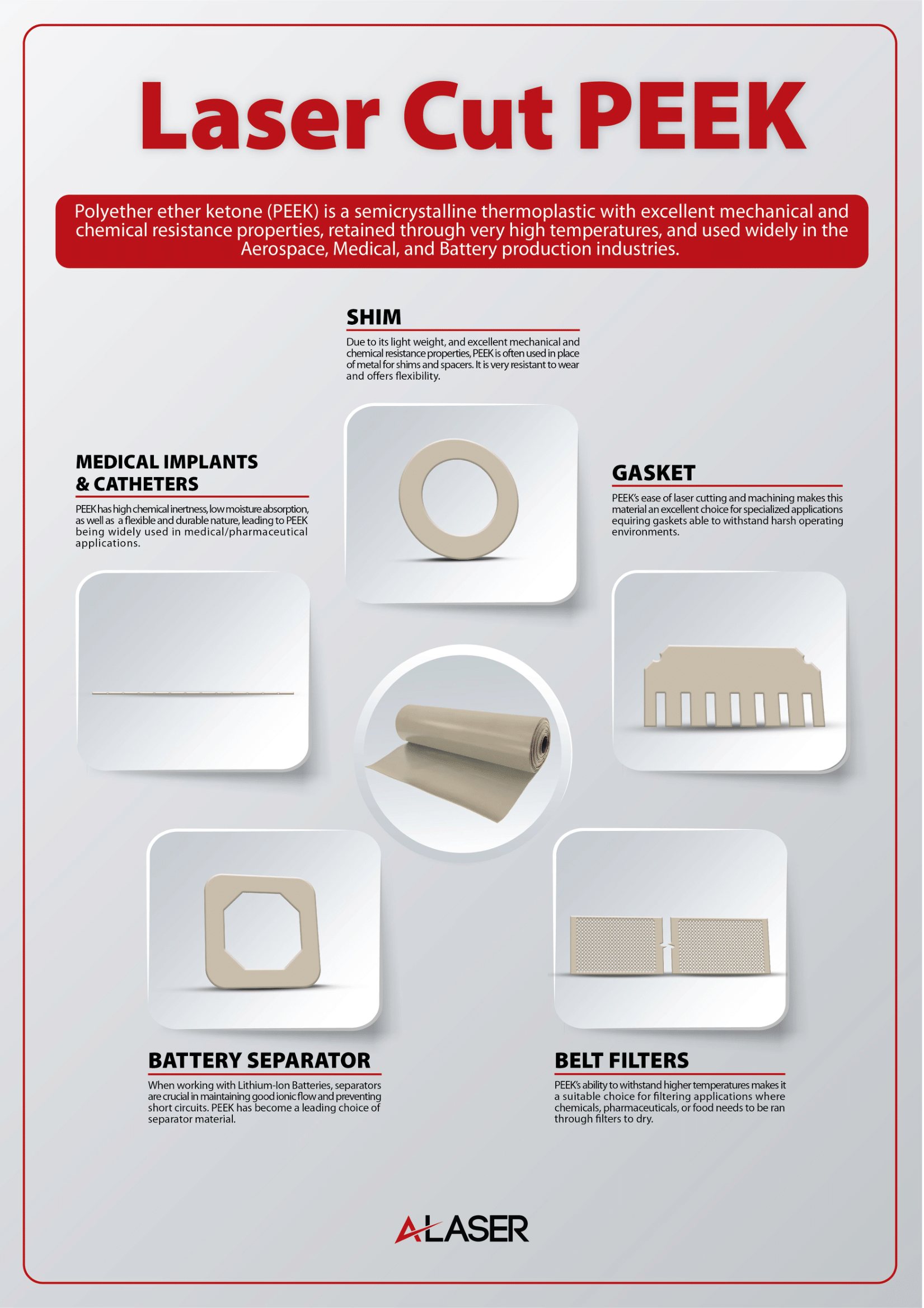
Manufacturing Outlets for PEEK
As mentioned, PEEK precision components are made by different technologies, using the raw forms that are currently available by manufacturers. Some of the more common are CO2 laser, CNC machining, die-cutting, CNC knife cutting and ultraviolet laser. It is ultraviolet or UV laser technology that has greatly taken advantage of its capabilities and cuts PEEK extremely well. Using ultraviolet laser systems, manufactures are producing PEEK parts and components made from sheets, tubes, and films. The way these types of lasers work is by ablation of the material. The beam of intensified ultraviolet light is focused and cuts or ablates along the programmed path, which is computer numerically controlled (CNC). Other adjustments to the power, dwell time, laser passes, and frequency are made per the specific qualities needed per the components design. The resulting components are accurate in many cases to a +/- 0.0254mm and a positional accuracy of +/- 0.0500mm of 500mm.
Future of PEEK
Having sustainability while being flexible and able to withstand harsh environmental conditions is important for today’s applications. Manufacturing of raw PEEK is changing to develop a more recyclable product and reduce its impact on the environment. PEEK, with its extraordinary properties and applications, is a material of great scientific discovery. With new avenues of technology being open and improvements to existing ones are made, materials like PEEK plastic are used in ways to overcome industry challenges with unmatched and creative solutions for space exploration, medical devices, food services, and countless others. As an integral part of innovation, we can expect to see PEEK plastic continue to be sought after for decades to come.