PCB Laser Cutter Precision and Flexibility for Modern Manufacturing
In today’s high-tech industries, precision is paramount, especially when working with printed circuit boards (PCBs). PCB laser cutting has emerged as the gold standard for separating boards from panels, offering unmatched accuracy, flexibility, and efficiency. Whether you’re crafting complex geometries or working with delicate materials, laser technology revolutionizes the depaneling process, surpassing traditional methods like milling, sawing, and die-punching.
The Advantages of PCB Laser Cutting
Applications of PCB Laser Cutting
Laser technology is transforming how industries approach PCB manufacturing, offering unmatched precision and flexibility.
Here are the key applications of PCB laser cutting:
-
Precision Depaneling: Essential for industries like automotive and aerospace electronics, where reliability and precision are paramount. Laser depaneling ensures smooth, clean separations with no mechanical stress, protecting delicate components while maintaining structural integrity.
-
Drilling and Marking: Perfect for creating vias or embedding traceability information directly onto PCBs. Laser systems deliver pinpoint accuracy, ensuring consistent hole diameters and clear markings for high-density designs, all while avoiding mechanical wear and tear.
-
Laser Routing: Provides clean, burr-free edges without the shape limitations of traditional cutting methods. This method vaporizes material rather than burning through it, resulting in maximum repeatability and tolerance. Ideal for intricate designs that demand sharp precision.
-
Laser Cutting Flex Circuits: Specially designed for delicate, vibration-free cutting of flexible circuits. This process minimizes thermal influence, preserving the quality and elasticity of Kapton and other flexible substrates, making it indispensable for wearable electronics and compact devices.
-
Prototyping: Accelerates product development cycles by allowing manufacturers to quickly iterate PCB designs. Laser technology eliminates the need for tooling, enabling the production of intricate prototypes with exacting tolerances and minimal lead time.
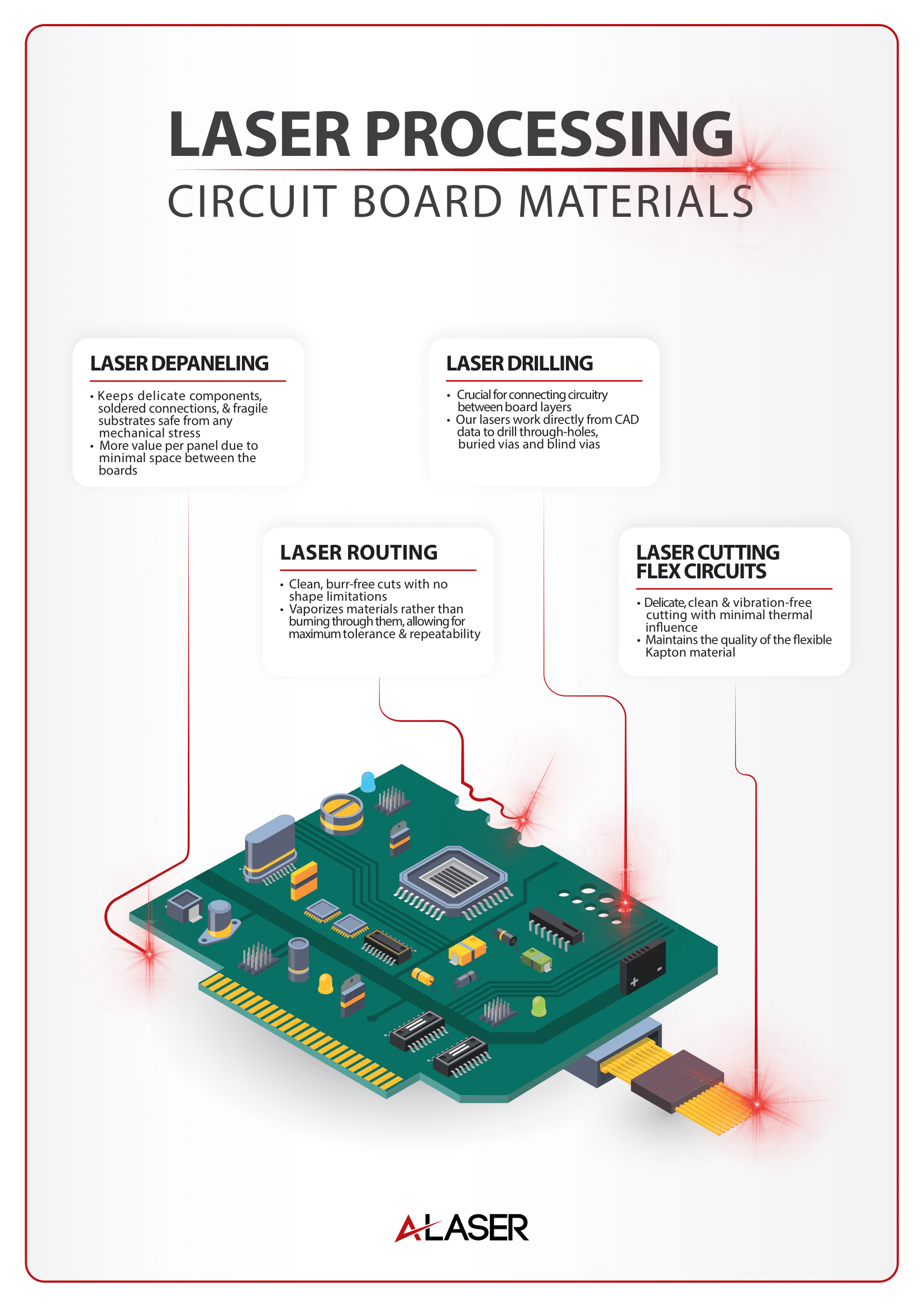
Comparison of Laser and Mechanical Depaneling Methods
Method | Precision | Material Stress | Cleanliness | Design Flexibility | Tool Maintenance |
---|---|---|---|---|---|
Laser Cutting | Extremely high | None | Dust-free | Unlimited | None (wear-free) |
Milling | Moderate | High | Dusty | Limited | Regular |
Die-Punching | Moderate | Moderate | Some debris | Limited | Periodic tool changes |
Sawing | Low | High | Dusty | Limited (straight cuts) | Frequent |
Addressing Common Misconceptions
“Does laser cutting generate excessive heat?”
Modern laser systems focus heat within a precise area, minimizing thermal effects. For example, temperatures 100 μm away from the laser point are comparable to reflow processes, ensuring no damage to sensitive components
“Is laser cutting cost-prohibitive?”
Laser cutting is not cost-prohibitive when considering its precision, elimination of tooling expenses, and ability to handle complex designs with minimal waste, making it a highly efficient and value-driven solution for a wide range of applications
Advanced Features for Optimized Production
Modern PCB laser cutters integrate with Manufacturing Execution Systems (MES), enabling real-time traceability and streamlined workflows. Their flexibility extends beyond depaneling to drilling, marking, and even structuring, providing a versatile solution for evolving production needs.
Why Choose Laser Cutting for PCBs?
PCB laser cutters are indispensable for industries demanding precision, speed, and adaptability. By leveraging this technology, you can:
- Reduce waste and material costs.
- Increase throughput with minimal downtime.
- Achieve superior edge quality for high-performance electronics.