Manufacturing with Silicone Materials
I can’t recall the first time I heard of silicon and what is was, but it was probably in the 1970’s. I grew up in San Jose, California and during those years I went from being a pesky adolescent to a sulky teenager. Well at least sometimes I was sulky, but that is another story. I do remember Atari and the amazement we all had when playing Pong. An older brother of mine purchased the system and we spent many nights in the wonderment of this technology. The orchards of the landscape were slowly being replaced with concrete. Why? Silicon. This material has made such an impact on our lives and fostered so many advances to technology. It is one of those amazing discoveries that will keep having an impact on our lives.
Credit to the invention of the silicon chip is given to Jack Kilby and Robert Noyce back in 1961. Noyce who founded Intel, also is credited with putting Silicon Valley on the map. This new way of integrating circuits, moved us from the older vacuum tubes that were prevalent in products until that time. It has made new technology progress to our current standards for phones, laptops, the internet. Still, what is silicon? Scientifically it has an atomic number of 14 and is a non-metallic in the carbon family. It is the 2nd most abundant element on earth. Only oxygen surpasses it. Through many processes’ silicon is formed into a crystalline and powder structure and used to form materials such as silicon wafers, glass, silicon rubbers, silicon-based adhesives and many more.
Manufacturing with silicone-based materials is done through a multitude of technologies like die cutting, stamping, precision saw blades, laser cutting, injection molding. These technologies allow products to be used in industries such as health care, aerospace where gaskets and sealants are vital, construction, household products like non-stick coatings, polisher and cleaners, paints, electronics for advanced computer technology, encapsulation, and numerous others. Is there a preferred technology used over others regarding silicone? I would say no. There are too many uses for this material and many manufactures have found ways to produce product. For my focus, manufacturing products from a silicone base is rewarding, but can also be challenging. Laser technology is just one way a gasket for example can be made. Creating them from a laser source will be dependent on the material, the color of the material and the type of silicone material it is? For silicon rubbers, those have a color blended work very well on a UV laser. Those that are clear, fare better on a CO2 laser system. For silicone-based adhesives used in conjunction with other materials, there does need to be an adjustment on a laser system that will cut both without damaging either. This is the fun part I have learned from engineers working in manufacturing using lasers.
Silicone materials are seated deep into our way of life, whether we know this or not. Once silicon is processed to become any numerous silicone polymers, the uses and benefits we have gained are almost incalculable. I wonder where we would be without it?
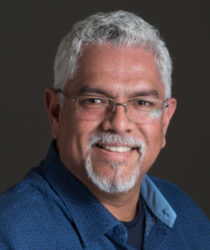
About the Author
Joe Azevedo was born and raised in San Jose, CA, right in the heart of Silicon Valley. He has lived in the area for the past 23 years, gaining a variety of industry knowledge throughout his career. In the late ’80s, Joe performed processing and touch-ups for Litho films in the manufacturing of printed circuit boards. In the early ’90s, Joe started working for SMT stencil suppliers as a CAD technician and, eventually, customer service. He did this for 16 years, then joined the FCT Assembly team in November 2009, continuing his role in customer service and account management in SMT stencils. Shortly after, Joe moved over to the A-Laser division in 2010. After two years at A-Laser, he transitioned from customer service support to sales. He considers the industries that we support and the projects we service a privilege to be a part of.