Does Laser Cutting Work for Copper & Brass?
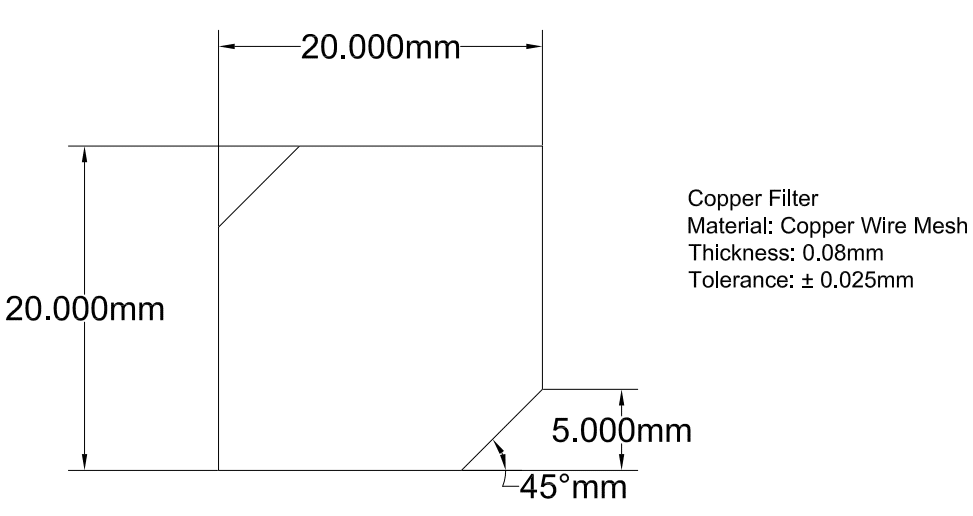
Laser cutting copper and brass are softer metal alloys that are readily laser cut on different systems. That’s one of the advantages you’ll find when looking at the prospect of using laser cutting technology for your next copper and brass precision project. In the timeline of precision manufacturing, laser technology is the newcomer, although it has been used since the mid 1980’s as an alternative source of components supporting flat, 2D geometries as well as tubular designs like medical stents and other micro tube devices. When projects of copper and brass come forward there are some considerations for all manufacturing methods to consider such as the design of the part, the thickness of the material, and the quantity. Laser technology has great attributes that give it the edge for certain brass and copper projects and can be a vital partner in a supply stream.
The Versatility of Laser Technology
From experience, there are two versatile laser types of cutting copper and brass today, and those are ultraviolet and fiber laser systems, producing precision parts out thin foils and sheets not only from the copper and brass, but from other alloys and materials. Here is a brief overview of each technology:
- Ultraviolet Laser: The are nanosecond pulsed laser systems, using relatively low wattage (power) .1 to 50 Watts to cut. Having narrow beam diameters of 20 micron, for example, UV lasers cut not only copper and brass, but stainless steel, aluminum, tungsten, nickel, nitinol and other metal alloys. Additionally, UV lasers cut polyimides (Kapton), rubber, FR4, graphene, polyetherketone (PEEK), adhesives and adhesive tapes and other non-metallic materials.
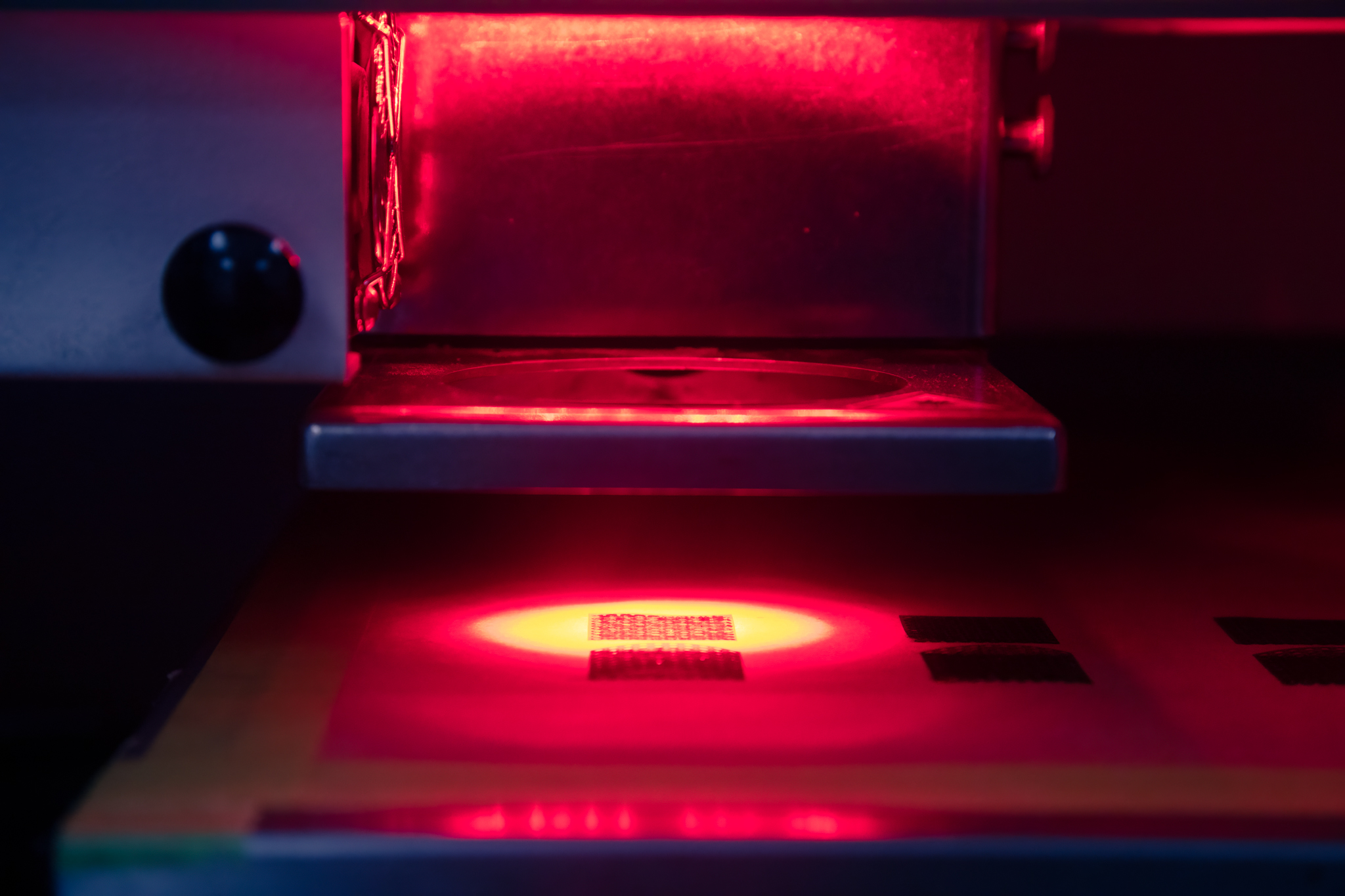
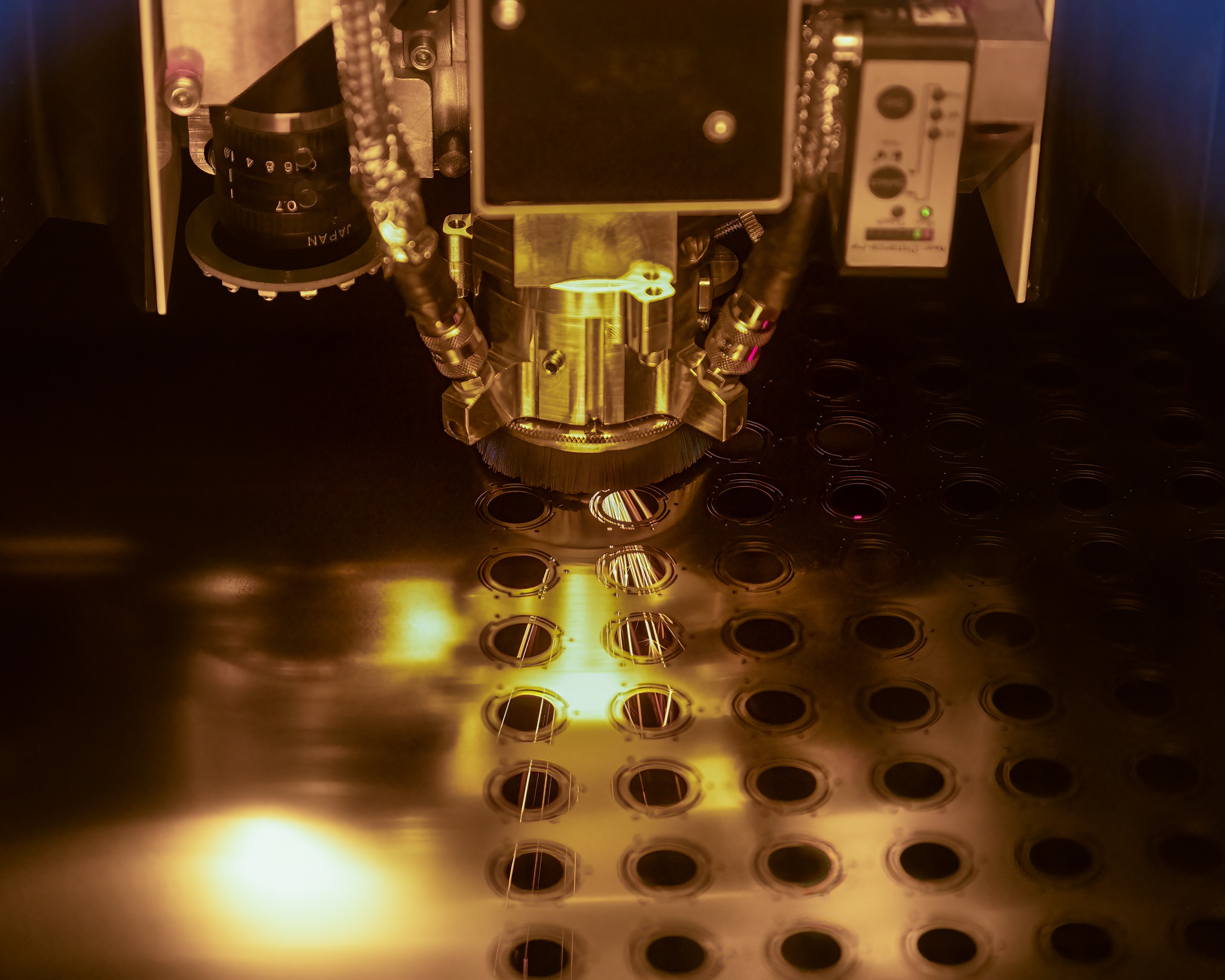
- Fiber Laser: Using intensified beam of light energy, fiber lasers generally use higher wattage ranging from 50 to 4000 watts or higher, with the higher levels of wattage directed at heavier industry needs and thicker grades of metal alloys. Fiber lasers are versatile in cutting alloys such as titanium, tungsten, stainless steel, aluminum, nickel, along with copper and brass. The beam diameters of fiber lasers vary but can be for example on some systems with dual cutting heads, 18 micron and 35 microns.
There are always continuing developments in laser technology and new systems with added material capabilities will continue to advance. For laser cutting copper and brass there will be continued needs to have these alloys cut for industries and devices for diverse and refined applications to sustain new products.
Why Laser Cutting Works For Copper and Brass
Copper is used in many applications but can be challenging to manufacture without damaging the material. The same is true for producing precision parts out of brass. Both alloys being malleable and resistant to corrosion can be used as internal components of devices or can be cut to produce ornate and visually aesthetic enhancements for architectural and interior design uses. Some advantages to cutting both materials by laser are:
Precision Control: With laser systems having small beam diameters as mentioned earlier, intricate and challenging profiles and designs can be cut. There are no tooling or expensive dies to be made when laser cutting. All that is needed is the CAD file to program the laser and if changes are made, it is to the file only. Many laser systems have a standard of tolerance of +/- 0.0254mm, but many can be controlled to tolerances of +/- 0.0127mm or tighter, depending on the laser system, thickness of the copper or brass, and geometry cut.
Prototype and Production Support: Laser manufacturers have an advantage of being able to support many projects at the R&D level and move quickly into full production overnight. Multiple iterations can be done on the same sheet of material to speed up testing and evaluation, while for production, parts are nested to maximize material usage.
The Challenge of Ultra-Thin Materials: Brass and copper come in pre-cut sheets or rolls of foils, much like the aluminum you will use in your kitchen. The handling of these materials takes great skill and procedures to consistently produce these raw forms into geometries that are precise and repeatable. Consistently providing highly accurate parts as tight as 0.5mil is an advantage that laser cutting has. Shinny metals like copper and brass can be polished into a high mirror like finish that may be important for aesthetics, but scratches and surface imperfections can diminish the function of internal components with rough edges and marred surfaces. To prevent issues from occurring, laser cutting is a non-contact method where only the cutting beam of light is doing all the work. Of course practices and procedures need to be in place for set machine set-up and post handling. Proper storage of materials for future production runs ensures repeatability without delay.
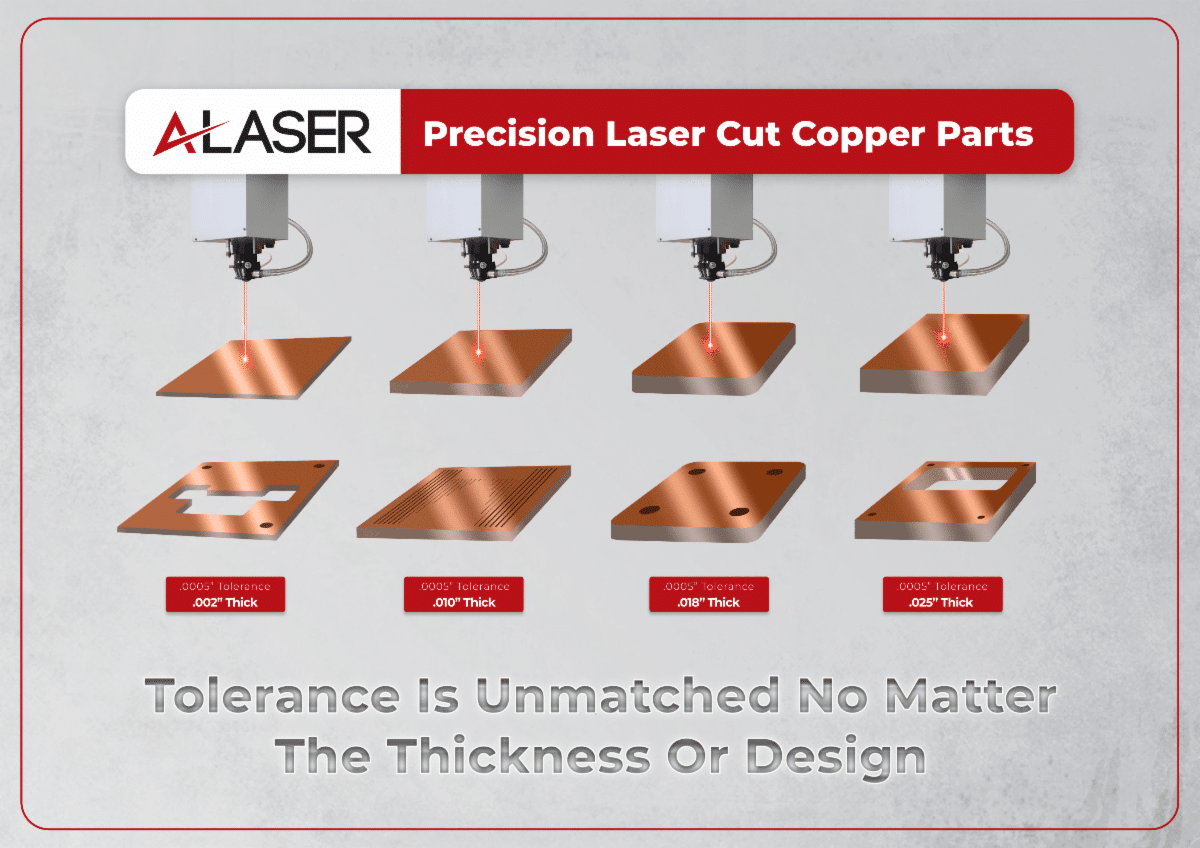
Conclusion
Laser cutting technology presents a revolutionary solution for manufacturing parts out of copper and brass, offering unparalleled precision and versatility. The ability to control laser systems with minute beam diameters allows for intricate and detailed designs without the need for expensive tooling or dies. This precision control, coupled with the ability to handle delicate materials without causing scratches or surface imperfections, makes laser cutting an ideal method for producing both functional components and aesthetically pleasing enhancements. Additionally, laser systems facilitate rapid prototyping and production, enabling manufacturers to quickly transition from the R&D phase to full-scale production, optimizing material usage and enhancing efficiency. As the demand for these alloys continues to grow across diverse industries, laser cutting technology stands out as a superior method for meeting the stringent requirements of modern manufacturing.