Laser Cutting Plastic Sheets
Laser cutting has revolutionized how plastic sheets are processed, offering precision, efficiency, and clean edges for a wide range of materials. For high-performance plastics like PEEK, Kapton, and Cirlex, laser cutting is often the go-to solution for industries requiring detailed components with tight tolerances.
Popular Plastic Sheets for Laser Cutting
Material | Key Properties | Applications |
---|---|---|
PEEK | High strength, chemical resistance, biocompatibility | Medical implants, aerospace components |
Cirlex | High dielectric strength, thermal stability | Insulators, high-frequency circuit components |
Kapton | Extreme heat resistance, electrical insulation | Flexible circuits, aerospace thermal barriers |
Acrylic (PMMA) | Optical clarity, impact resistance | Retail displays, light diffusers |
Polycarbonate | Toughness, high impact resistance | Machine guards, electronics housings |
Understanding the properties of these plastics helps determine their suitability for specific projects.
How to Ensure Optimal Results with Laser Cutting
- Choose the Right Plastic: Advanced plastics like Kapton and PEEK are designed for high-performance applications, making them ideal candidates for laser cutting.
- Understand Thickness Limits: While lasers can handle both thin and thick plastic sheets, the specific machine type and laser wavelength impact the results.
- Collaborate Early: Working with your cutting partner during the design phase can ensure the most efficient process for your project.
How Laser Cutting Enhances Plastic Sheet Applications
Whether you’re designing parts for medical devices, aerospace components, or flexible electronics, the choice of cutting method matters. Laser cutting is increasingly popular for advanced plastics like PEEK, Kapton, and Cirlex due to its ability to produce consistent, high-quality results.
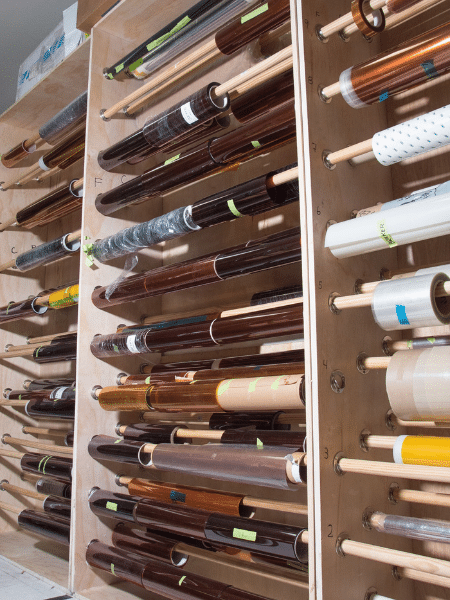
Tips for Designing Plastic Parts for Laser Cutting Sheets
Use CAD Software
Precise designs ensure that the laser follows exact dimensions and paths.
Consider the Material
Thin films like Kapton may require different laser settings compared to thicker materials like PEEK.
Account for Thermal Properties
Some plastics, such as Cirlex, are highly resistant to heat, making them ideal for laser cutting with minimal distortion.
What Can You Create with Laser-Cut PEEK?
PEEK is one of the most versatile and high-performance plastics available, and laser cutting takes its potential even further. From intricate gaskets and shims to critical medical implants and catheters, laser technology enables the precise fabrication of PEEK parts for a wide range of industries. Whether you need durable belt filters, efficient battery separators, or components for demanding environments, laser cutting delivers the accuracy and consistency needed for complex designs.
Laser cutting also eliminates the need for tooling, making it ideal for low-volume production, rapid prototyping, and high-mix manufacturing where speed and adaptability are key. Explore the infographic to discover the full range of innovative parts you can create from laser-cut PEEK and other high-performance plastics.
Processing plastic sheets with laser technology offers a range of benefits: clean, burr-free edges, exceptional accuracy for complex geometries, and the ability to handle materials as thin as films or as thick as heavy-duty sheets.
PEEK’s versatility and performance make it a standout material for precision parts, but it’s just one of many plastics that excel with laser cutting. Materials like Kapton and Cirlex are ideal for high-temperature or electrically insulative applications, while acrylic and polycarbonate provide solutions for optical clarity, impact resistance, and lightweight durability.
- Click image to enlarge
FAQs About Laser Cutting Plastic Sheets
-
A: Laser cutting uses a focused beam of light to vaporize material along precise paths, eliminating tool wear, minimizing material waste, and creating cleaner edges than mechanical methods.
-
A: Yes, with proper techniques, heat-sensitive materials like Kapton can be cut with minimal heat-affected zones. This maintains their structural integrity and ensures optimal performance.
-
A: Laser systems can process a range of thicknesses, from ultra-thin films to thicker sheets, depending on the plastic material and cutting equipment.