Laser Cutting Metal Revolutionizing Industries and Shaping the Future
Laser cutting metal has become a game-changer across industries, offering precision, efficiency, and innovation that were unimaginable decades ago. From its early beginnings to its modern-day applications, laser cutting has transformed how metal components are produced, paving the way for breakthroughs in sectors such as aerospace, automotive, and beyond.
The timeline of laser cutting in metal fabrication reflects a history of ingenuity and constant improvement. What began in the 1960s as a method to cut hard materials has evolved into a sophisticated process that enhances precision, reduces waste, and supports the complex demands of modern manufacturing.
The Evolution of Metal Laser Cutting
Early Beginnings (1960s-1970s)
Laser cutting emerged during the 1960s as a cutting-edge solution for materials like titanium and steel. Initially used primarily in aerospace for its ability to handle complex geometries, the technology started gaining traction in the automotive industry due to its capability to streamline production.
Technological Advancements (1980s-2000s)
With advancements in computer-controlled laser systems, metal cutting became faster and more accurate. The introduction of fiber lasers significantly improved energy efficiency, enabling more precise cuts on thinner metals and alloys. By the late 1990s, laser cutting had become a mainstay in automotive production, particularly for body panels and structural components.
Modern Applications (2010s-Present)
Today, laser cutting is utilized for intricate, high-performance parts in industries like medical device manufacturing and renewable energy. Aerospace relies heavily on laser technology to ensure precision in everything from turbine blades to aircraft body components, while the automotive industry benefits from its cost-effectiveness and ability to mass-produce parts without sacrificing quality.
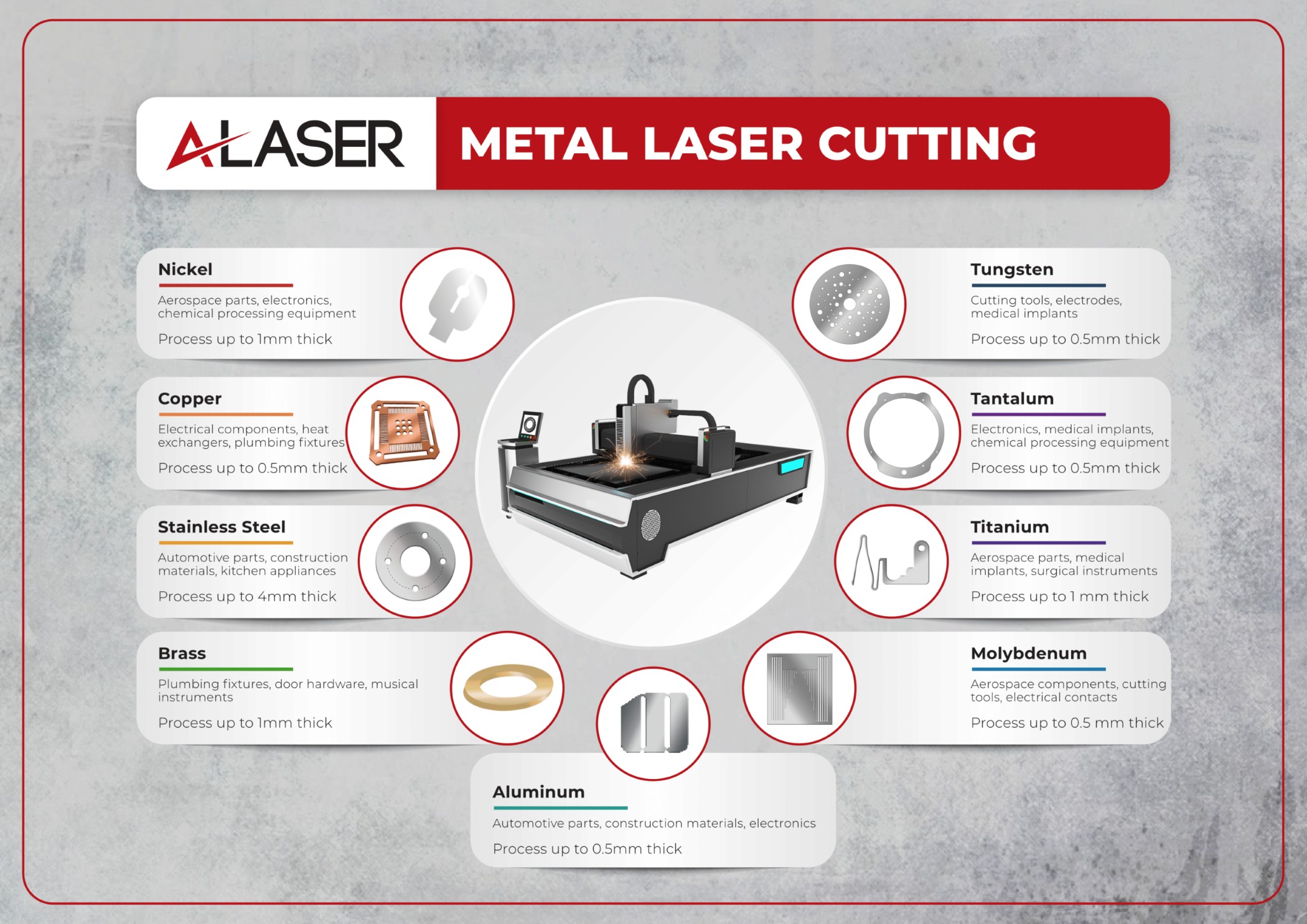
Emerging Trends and Challenges in Using Laser-Cut Metal in Specific Industries
As laser-cut metal technology advances, new trends are shaping the automotive and aerospace industries, while challenges are emerging as manufacturers adapt to new materials and expectations.
Emerging Trends:
-
Automation and Robotics: The integration of AI and robotics in laser cutting systems is becoming increasingly common. This trend is helping industries, particularly automotive manufacturing, improve production speed while maintaining the precision required for complex parts. Automated laser cutters can optimize cutting paths in real-time, reducing human error and downtime.
-
Multi-Material Use: Another trend is the ability to cut multiple metals, including copper, aluminum, steel, and titanium, in a single process. For example, copper is commonly used in automotive electrical components due to its conductivity, and advancements in laser technology now make it easier to cut and shape without damaging the material.
-
Sustainability: There’s an increasing focus on sustainability, and laser cutting is playing a key role in this. In automotive manufacturing, the precision of laser cutting reduces material waste and energy consumption, contributing to greener production processes. Manufacturers are now using more eco-friendly metals like aluminum and stainless steel, which are both lightweight and recyclable, supporting sustainability goals in both aerospace and automotive sectors.
Challenges:
-
Cutting Reflective Metals: Cutting reflective metals like copper and aluminum poses a challenge for traditional laser systems because they can reflect laser beams back into the machine, potentially causing damage. While new fiber laser technology has made progress in mitigating this issue, cutting reflective metals efficiently still requires specialized equipment and expertise.
- Thermal Distortion: Another challenge, particularly in aerospace and electronics applications, is thermal distortion. Thin metal sheets, such as copper or aluminum, are prone to warping when subjected to heat during cutting. This can affect the dimensional accuracy of parts, making it crucial for laser technology to continually advance in controlling heat input and minimizing distortion.
Metal Laser Cutting Applications:
Industry | Laser Cutting Application | Advancements & Trends |
---|---|---|
Aerospace | Engine parts, turbine blades, aircraft body components | Lightweight materials, heat management, intricate designs |
Automotive | Body panels, structural components, exhaust systems | Automation, mass production, minimal material waste |
Medical Devices | Precision components, surgical tools | Ultra-fine cutting, biocompatible materials |
Renewable Energy | Wind turbine components, solar panels | Sustainability, cutting new alloys for energy efficiency |
Electronics | Circuit boards, heat sinks, small-scale precision parts | Miniaturization, complex patterns, rapid prototyping |
Looking Ahead: The Unfolding Potential
As laser cutting continues to evolve, the possibilities for its application are nearly limitless. The move toward fully automated, AI-driven laser systems is transforming the manufacturing floor, while the development of new materials presents both exciting opportunities and fresh challenges. In the future, we can expect even greater precision, energy efficiency, and the ability to process ever-more complex parts, keeping industries like aerospace, automotive, and renewable energy on the cutting edge.
Laser cutting metal is not just a fabrication method—it’s a force driving industries into the future, revolutionizing how we build and innovate. Whether you’re looking at the past, present, or future, laser technology remains at the forefront of precision manufacturing, cutting a clear path to what’s next.