A Solution for Many Industries
Kapton film is one of those technological wonders that has such a profound effect on many advances in space exploration, aeronautics, electronics and many more facets of industry we rely upon. With such impact as a material, one cannot discuss the attributes of this polyimide, without mentioning Dupont Corporation, which Kapton is a trademark of. Kapton, which was introduced back in 1965, was designed to withstand extreme temperature ranges from -269°C to +400°C. A polyimide in chemical make-up made Kapton available for applications in industries that required temperature stability from extreme cold to extremely high levels. It has great resistance to chemicals, making it a fantastic material for harsh conditions. It was designed to be flexible, offering new options for mechanical solutions. It was first applied within the aerospace industry and through the years Kapton was being used for flexible printed circuits in new developing technologies, for automotive applications, heavy industry uses, medical devices, defense and so many other numerous applications. The push for new research and advances in technology was the spark that engineers took to create new formulations of Kapton film to support these expanding industries. As new Kapton types were developed, manufacturing methods like laser cutting technology followed to keep pace with demands for precision parts and cutting of flexible circuits.
The Impressive Polyimides
To support increasing demand to industries needing the characteristics of Kapton, but customized to specific uses, Dupont has developed a series of base types of Kapton such as*:
Kapton® Type* | Base Film Description |
---|---|
HN | General purpose polyimide. |
HA | Amorphous general purpose polyimide film exhibiting higher elongation |
FPC | Higher dimensional stability, surface modified for improved adhesion to the film |
EN | Lower CTE film to closer match copper |
B | Black, homogeneous opaque film |
WS | White film |
MT / MT+ | Higher Thermal Conductivity: up to 6 X HN (>0.7 W/mK) |
* Shown above is a partial summary listing of Kapton® polyimide films. Source: Dupont Corporation.
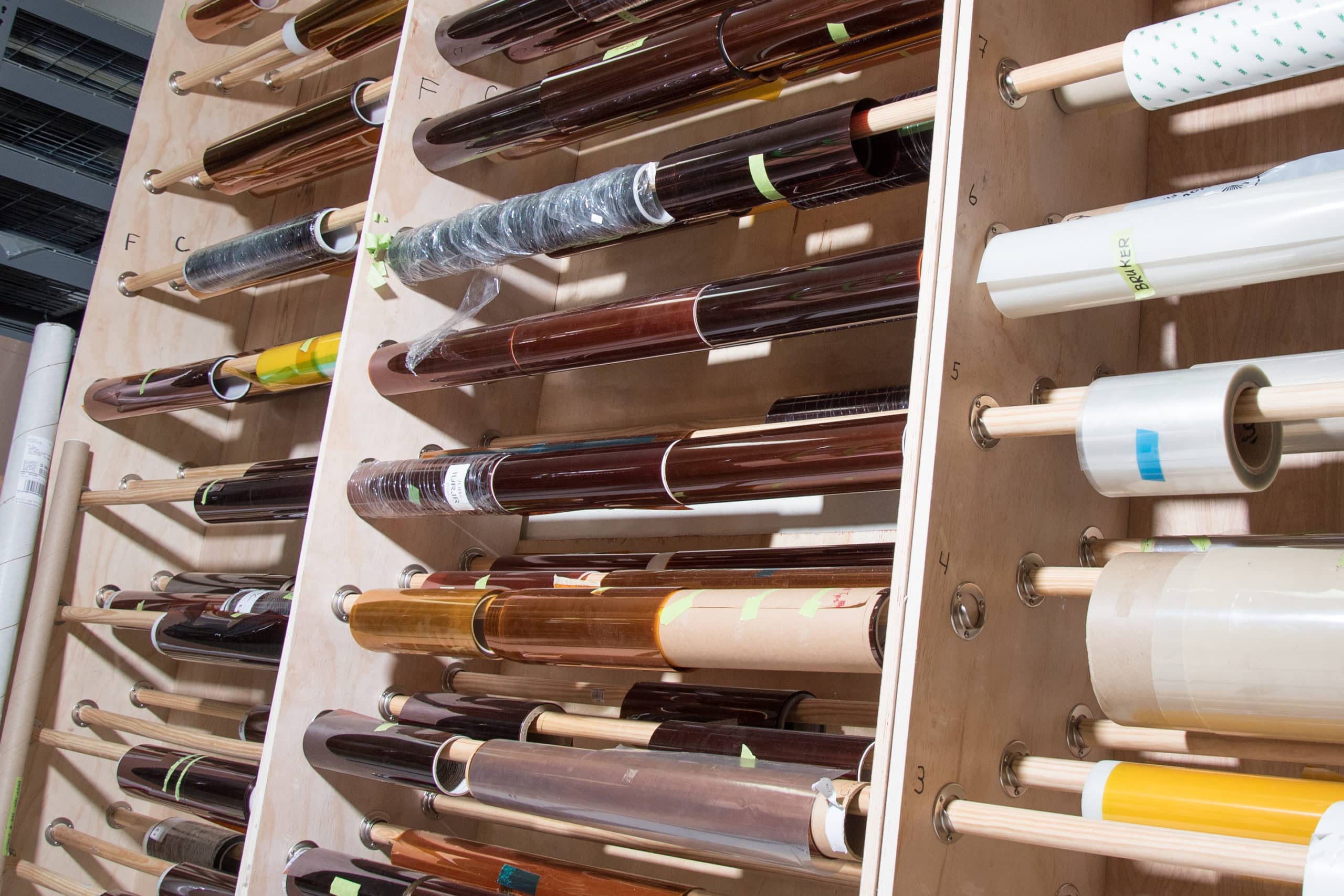
Kapton films are available for such diverse applications and as polyimides, the characteristic of great thermal range and chemical resistance has allowed for formulations to be produced with enhanced chemical resistance, shrinkage resistance, thermal conductivity, abrasion resistance that focuses on specific industry uses and applications. The following is a sampling of these formulations*:
- Kapton® B
This matte black polyimide film offers exceptional physical, chemical, and electrical properties in a broad temperature range, as well as excellent dimensional stability at high temperatures.
- Kapton® EN
This premium polyimide film is ideal for use as a dielectric substrate in flexible printed circuits and high-density interconnects. It offers superior stability, a high modulus, and a matching coefficient of thermal expansion to copper, making it the preferred choice for very fine pitch circuitry.
- Kapton® EN-A, EN-C, EN-Z
Superior quality polyimide films for use as a dielectric substrate. A perfect choice for chip on film, flexible printed circuits, high-density interconnects, and next-generation IC packaging applications. These films offer excellent CTE control, high modulus, and surface quality, making them preferred dielectric films.
- Kapton® FN
Designed with FEP fluoropolymer on one or both sides of Kapton® HN, this polyimide film is durable, versatile and offers added chemical resistance. Its heat bonding and sealing capabilities make it ideal for a range of industrial applications.
- Kapton® FPC
This polyimide film is treated on both sides and features exceptional physical, chemical, and electrical properties over a wide temperature range, similar to our general-purpose Kapton® film. Additionally, it provides superior dimensional stability and adhesion specifically designed for flex circuit manufacturers who require high-quality adhesion and low shrinkage properties.
- Kapton® HN
For applications requiring a high-performance all-polyimide film, Kapton® HN is the recommended choice due to its exceptional balance of properties over a wide temperature range. It has proven effective in extreme temperatures, ranging from -269°C to 400°C. This versatile film can be laminated, metallized, punched, formed, or coated with adhesives.
* Shown above is a partial summary listing of Kapton® polyimide films. Source: Dupont Corporation.
Transforming A Transformative Material
As impressive as Kapton is, seeing it being made into precision components is equally impressive. Because Kapton film is flexible and comes in varying thicknesses, choosing the right manufacturing method is very important. Over the past 30-40 years, laser technology itself has developed and increased its levels of efficiency, accuracy and sustainability. By doing so, laser cutting of Kapton has become on of the most popular methods and materials used in the laser cutting industry. Under ultraviolet laser technology, Kapton and polyimides in general, are cut to very fine and precise geometries serving all the industries as mentioned earlier. The fusion of UV laser systems and Kapton film were destined to be a match in precision manufacturing. Although Kapton is processed by other manufacturing methods like die- cutting and CNC knife cutting, for custom precision components laser technology continues to be a favored option.
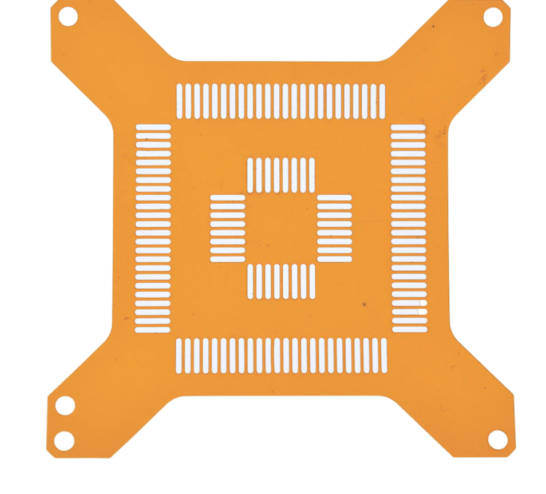
Kapton surface mount rework stencil
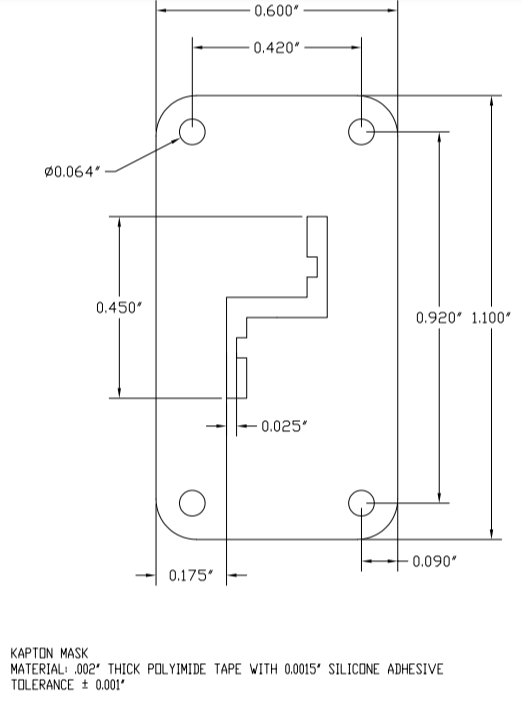
Impacting the Twenty First Century
More powerful computers, phones, and watches are some of the most recognizable products we use and rely on for communication and entertainment as well as monitoring of our health and wellbeing. Many of these types of products will have flexible circuitry made from Kapton film. Many industries used to manufacture goods are run by smarter and more efficient controllers, sensors, and other automation tools, and these too will have Kapton as part of the circuitry and sustainability by being chemically resistant and provide continuous operation in extreme temperature ranges. The use of Kapton during the space race helped insulate critical wiring and components and electronics. Its use can be seen today in the operation of the James Webb Space Telescope, which the solar shield is made in part using Kapton. Without Kapton, many of the advances in technology we have today would not be available. The following are additional examples of the countless ways Kapton is used, but still a microcosm of the benefits it is making in the twenty first century:
Electronics and Semiconductor Industry:
- Flexible Circuit Boards: Kapton’s flexibility and heat resistance make it ideal for flexible circuits, enabling smaller and more durable electronic devices.
- Chip Encapsulation: Kapton is used to encapsulate and protect integrated circuits from moisture, dust, and mechanical stress.
Aerospace and Automotive Industry:
- Spacecraft Insulation: Kapton is used in multilayer insulation (MLI) blankets to protect spacecraft from extreme temperature fluctuations.
- Wire and Cable Insulation: Kapton’s excellent electrical insulation properties make it suitable for insulating wires and cables in aircraft and electric vehicles.
- Medical Devices: Kapton’s biocompatibility and heat resistance make it suitable for various medical devices, such as catheters, implants, and surgical instruments.
Other Industries:
- Telecommunications: Kapton is used in fiber optic cables and other telecommunication equipment.
- Energy Storage: Kapton is used in batteries and fuel cells to improve performance and safety.
Overall, Kapton’s unique properties make it a versatile material with a wide range of applications in modern technology.
Conclusion
Kapton film, a remarkable material with exceptional thermal and electrical properties, has undeniably left an enduring mark on diverse industries over the past four decades. Its ability to withstand extreme temperatures, harsh environments, and mechanical stress has made it indispensable in applications ranging from aerospace and electronics to medical devices and telecommunications. As a testament to its versatility, Kapton lends itself well to various machining techniques, particularly laser cutting, which allows for precise and clean cuts. With its continued innovation and adaptation to emerging technologies, Kapton film is poised to shape the future of countless industries, solidifying its legacy as a truly transformative material.
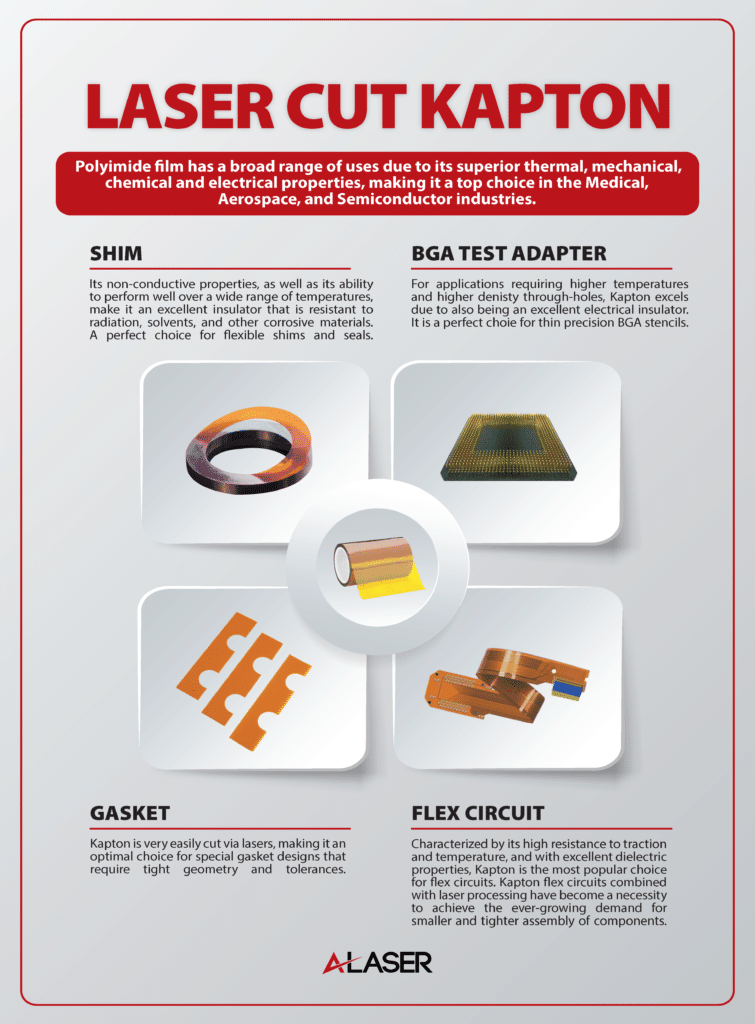