Innovation through Iteration
Research and Development, a term commonly referred to as R&D, is the central process in which new advances are made. We see this throughout history, when changes to the environment challenged man to advance the skills for hunting, for changing ways to procure sustenance, to better the way to communicate and share ideas on a larger scale, all had in one way or another iteration. The first attempts to create a new tool or new process to leech out the tannin in acorns, were not developed overnight. This took time and took desire to find a better way.
I don’t know when the term R&D was commonly used, but in my lifetime, it seems to be the basic process to advance technology. This covers all areas of our lives, from studies on human interaction, transportation, medicine, agriculture and so on. Why is this done? I see it as the desire to make a difference in our lives for the better. That is a global statement and not every advancement of course has improved our lives nor was made to better man’s place in the world, but from my experience in laser manufacturing, I do get to see the recurring focus to do something better for our lives and environment.
One of my first experiences in seeing R&D in action was for a medical device project. This was taking a known medical procedure for heart surgery to a new process. A new method and medical tools were being developed in tandem with goals to reduce surgical time and allow patients to recover in days as opposed to weeks.
I recently attended a webinar on materials and technology and the term “Innovation through Iteration” was brought up. I love this term, as it clearly states the path that is needed for invention, for improvement in technology. We faced a challenge that the customer needed one part to have two different thicknesses out of stainless steel. A plan was formed to have the raw material chemically etched down to the prescribed thinner thickness. This material was then aligned on laser to cut the profile. It took support from the technicians giving feedback to the Quality Team then the QA Team inspecting and rejecting what was non-conforming and finally providing the customer with trial runs until signed off and approved. The whole project would take years in planning but was a collaboration we were very proud to be a part of.
During all this R&D, the OEM had to be thinking of scaling up. Can this process, these materials, be scaled up for mass production? What is cost now and throughput and what will the cost be for higher quantities? Can the current suppliers support and keep up with demand while being cost competitive? These questions of course are needed to be asked in parallel of an R&D project that has a final goal of production for mass use. As a supplier of precision parts, I want to know what the scope of the project is and if production what is the demand and so on. Ultimately both parties want to achieve their goal of success of product improvement and their financial bottom line.
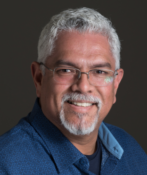
About the Author
Joe has been part of the A-Laser team for over 10 years and has extensive experience with laser cutting technology, sales, and customer service. Joe was born and raised in San Jose, CA and has resided with his family in Gilroy, CA since 1997. The unique projects he gets to learn about and the industries they support, keep everyday new! His hobbies include photography, he is a member of the Morgan Hill Photography Club, hiking, model building and collecting vintage camping lanterns and stoves. His favorite places include Mount Lassen Volcanic National Park, Portland OR, and Boston MA.