Designing for laser cutting is the start to using technology that offers a powerful pathway from digital designs to physical reality. Gaining the full potential of laser technology demands a design approach attuned to its nuances. This discussion will explore critical considerations when designing laser cutting precision parts for the best optimization. Beginning with the selection of appropriate materials and understanding the impact of the laser beam diameter, also known as kerf. We will then examine strategies for efficient material usage through intelligent nesting of parts, touch upon potential post-laser processes such as chemical deburring, tumble deburring, and electropolishing, that can enhance the final product. Finally, we will address the importance of defining the desired quality level, whether through AQL sampling or 100% inspection, and designing with the achievable degree of tolerance control (precision) in mind. By thoughtfully addressing these factors, designers can create laser-cut parts that are not only accurate and functional but also cost-effective and meet the required specifications.
Materials and Laser Technology
One of the best attributes of laser technology is the ability to cut a wide spectrum of materials, that include polymers, laminates, plastics, adhesives, metal alloys, gasketing and rubber-based types and many more. These capabilities are not cut on one laser system however but done with technology using different wavelengths of light with an extreme variance of power, beam diameter, speed and other characteristics. Laser service providers know the capabilities of the systems they use so a key question is:
“Does the required material choice fit within their ability to manufacture precision components?” Once that is made clear, there are some general categories for materials and laser technology to consider:
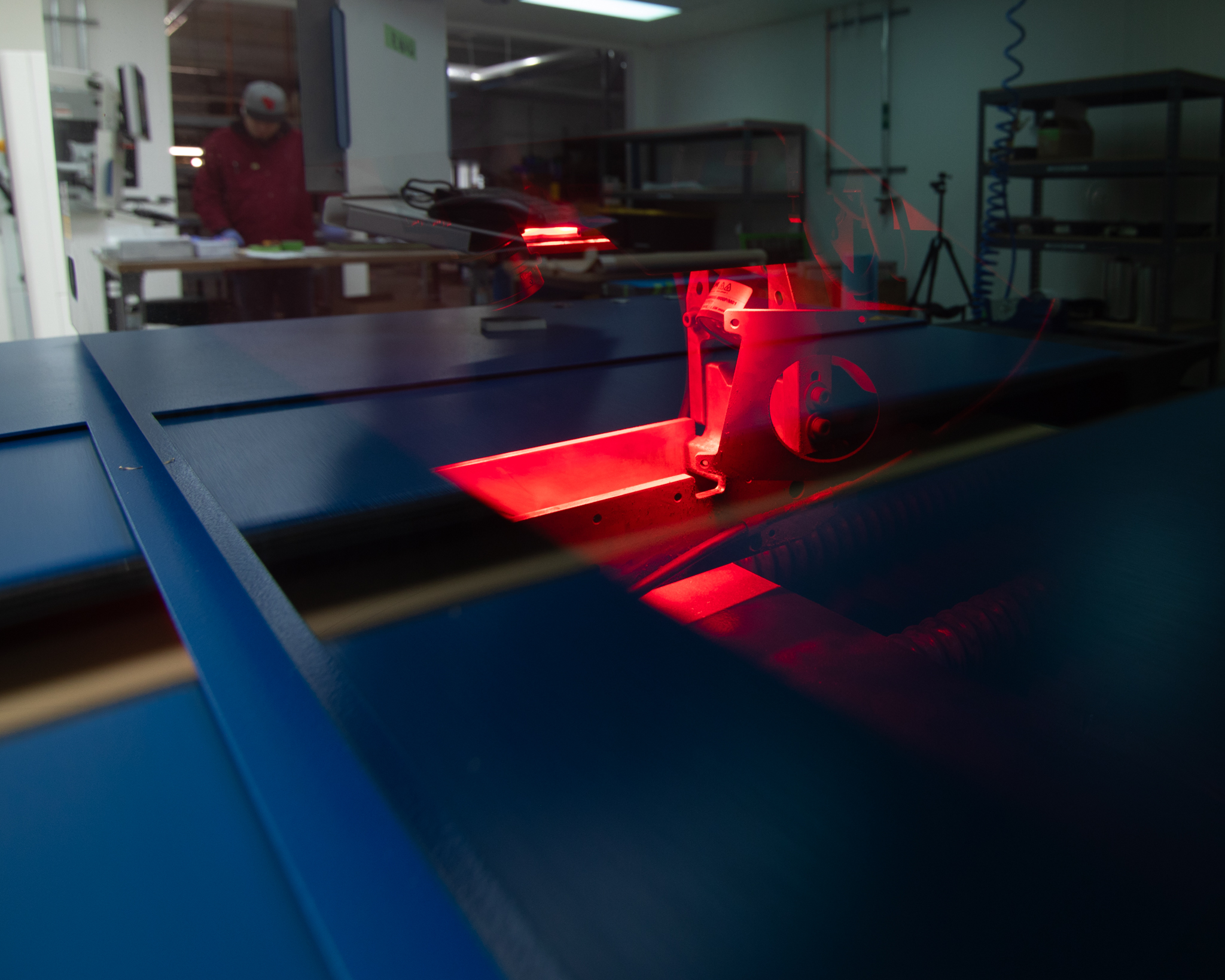
- Ultraviolet Lasers: Materials on these systems can vary greatly on these YAG pulsed systems cutting polyimides (Kapton), PEEK, FR4, graphene, mylar, silicon and nitrile rubbers, and metal alloys like stainless steel, copper, brass, molybdenum, nitinol, nickel, tungsten and many more. Best at ultra-thin and thin gauges of these materials, generally up to 0.508mm thick with beam diameters of 20um.
- Infrared Lasers: Cutting a broader range of thickness of metallic alloys, but no non-metallic materials. IR lasers are very adapted to cutting the family of stainless steel alloys up to 0.635mm or possibly thicker, with beam diameters of 30 to 35micron.
- Fiber Lasers: Provided in much higher power than UV lasers, from 50 watts to 4000 watts or higher. Fiber lasers cut metal alloys in greater thickness, up to 4mm to 10mm on stainless steel for example. They also can cut thicker tungsten, titanium, brass, nickel, and copper. Beam diameters vary, but some systems, for example, employ dual lasers cutting heads using 18 to 35micron beams.
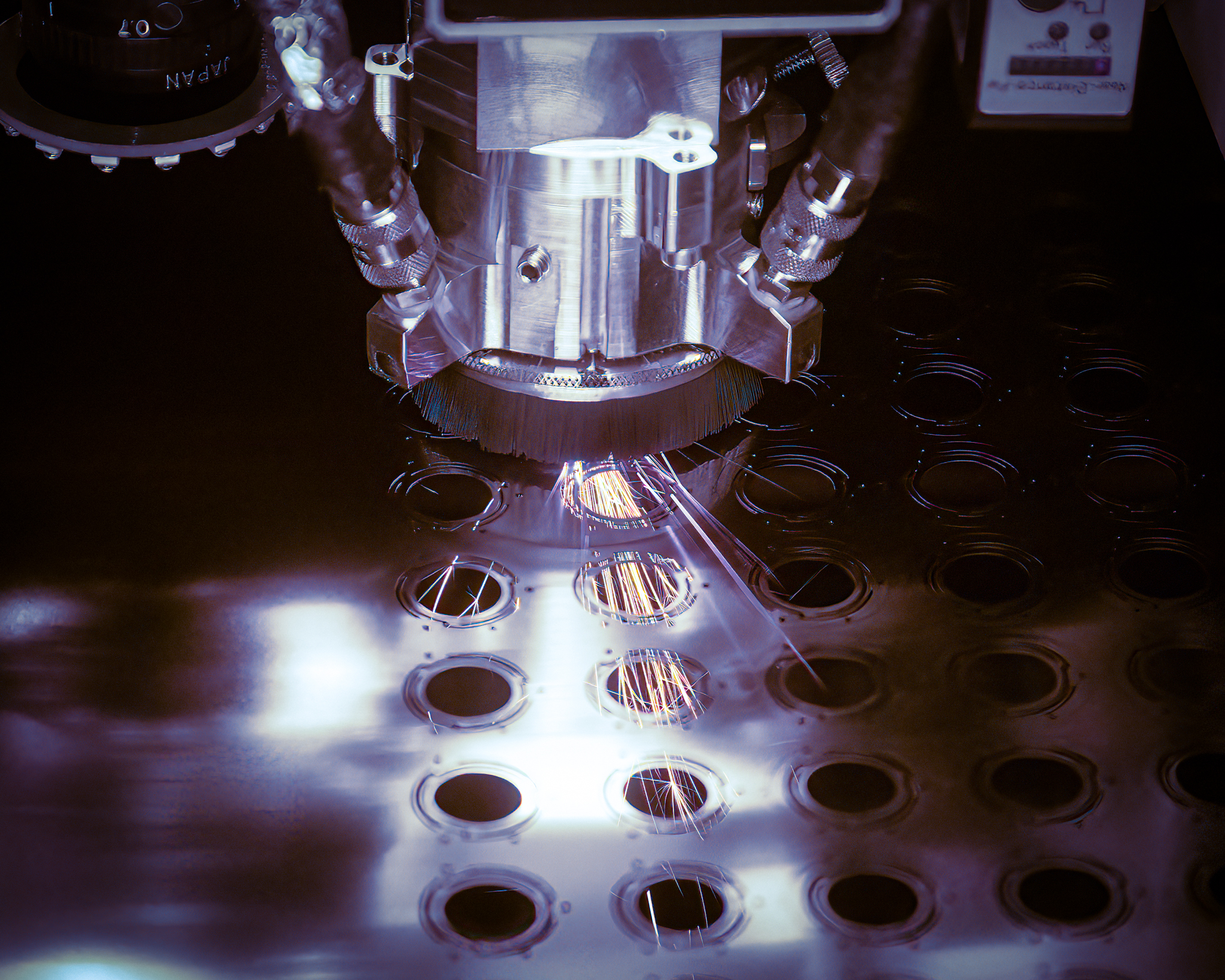
- CO2 Lasers: Cutting plastics, wood, and paper are some of the materials that are readily processed by this technology. They are not preferred to cutting metal alloys, but more powerful systems can.
- Picosecond and Femtosecond Lasers: Ideal for ultra-micromachine projects, these systems have beam diameters of 3-5 microns for example. They produce very fine features but are limited to materials in thicknesses of 15 microns thick or thinner for many systems.
Design For Manufacturing with Lasers
Laser cutting excels at providing flat, 2D profiles, along with intricate features like holes, slots, small radius and sharp corners. The beam or kerf will limit the minimum size of the geometry produced. This is a key factor to keep in mind when a new design is being considered. Specifically, by asking potential service providers what the capabilities of their laser cutting machines. Knowing what materials and geometric constraints will keep unwanted surprises from occurring. These guidelines can help when designing for using laser cutting technology:
- Material Type, thickness, and Availability: Though your project intends to use a 9mil silicone rubber, it may not be produced at that thickness. A 16mil thick stainless-steel component may only be produced at 15.5 mils and have limits on availability or be produced on large rolls rather than small single sheets. Do you need a material that has a high thermal threshold or one that has excellent light blocking characteristics? There are material solutions to almost every project and when there is none, custom materials can be made. Industry applications in many instances use materials like stainless steel for surgical instruments and aluminum for aerospace, and copper for electronics. These are generalizations of course and every precision project has a material as a key element. The impact of a materials availability depends on the design flexibility. Custom materials can be made but time and cost can extend the lead time and increase the budget of a project.
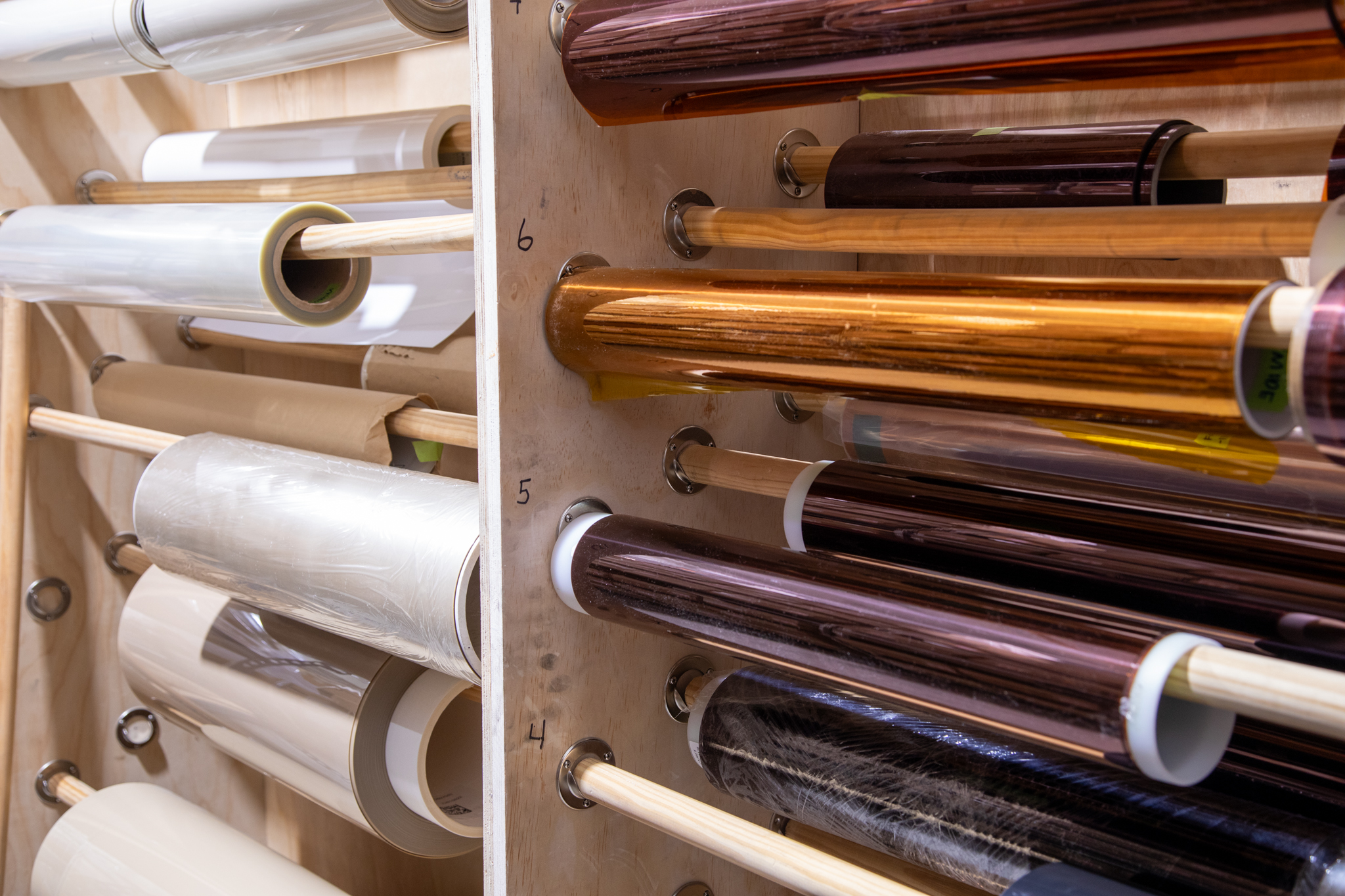
- Features To Be Cut: Laser cutting is prominent in applications supporting industries in development and production such as: medical devices, semiconductor processing, space-telecommunication, battery technology, electronics, sensors, aerospace, textiles and industrial dispensing, and numerous others. In general, the smaller the features are, the finer tuning of the laser parameters will be needed. Precision requires meeting or exceeding all the aspects of the intended designs by matching the laser systems capabilities with the material and geometric constraints. Some systems, for example, may produce a minimum feature of 0.08mm on materials up to 10 mils thick and a minimum of 0.13mm for materials above 10mil thickness. For a 12-micron hole, you could not use a UV laser that has a 20-micron beam. Laser manufacturing experts will be the best guide to match the right laser technology for the intended design.
- Maximizing Material Use: A recurring theme when designing for laser cutting is material. Maximizing the use by nesting of parts saves materials which can be very costly especially for limited types or custom laminates. Service providers will nest parts to maximize material usage. Additionally, if more parts are to be cut, it will save time and cost by asking if your provider can store unused material for a later production date.
- Locking In the Tolerance: Manufacturing to tight tolerances indeed are one of the most contributing factors in deciding to use laser cutting for precision parts. For many systems a +/- 0.0127mm is standard, but tighter tolerances can be held depending on the laser technology being used. Designing with a tolerance that is larger than the manufacturers standard, can speed up the laser process, while a tighter tolerance can reduce throughput, but may be necessary for the components design requirements. A tight or open tolerance will affect the level of inspection that is needed. With many precision manufactures being certified under ISO regulations or similar industry guidelines, there are required steps to ensure a parts conformance through inspection. If the tolerance on your part can be adjusted, advise your manufacture so the fastest and most efficient schedule is input.
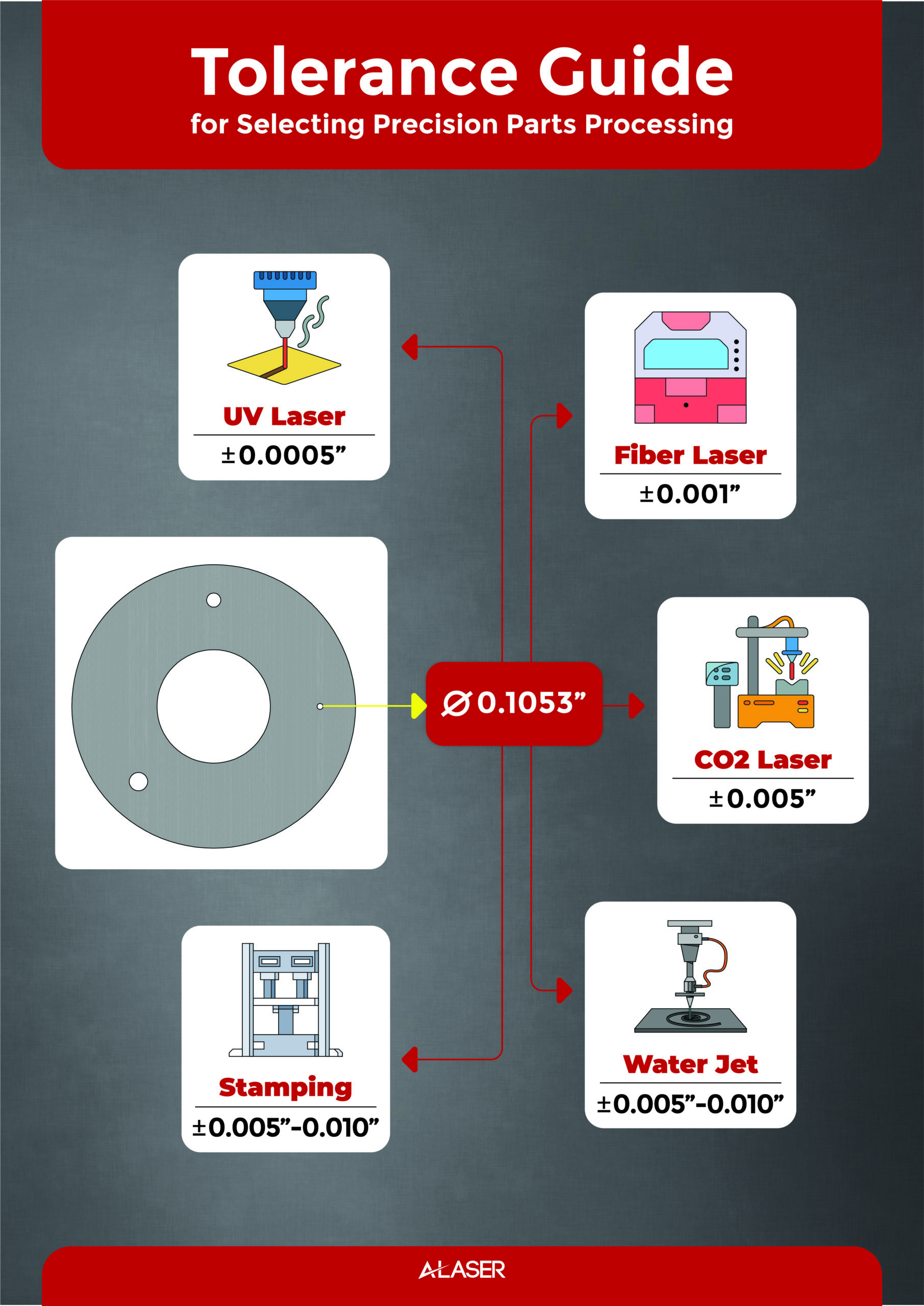
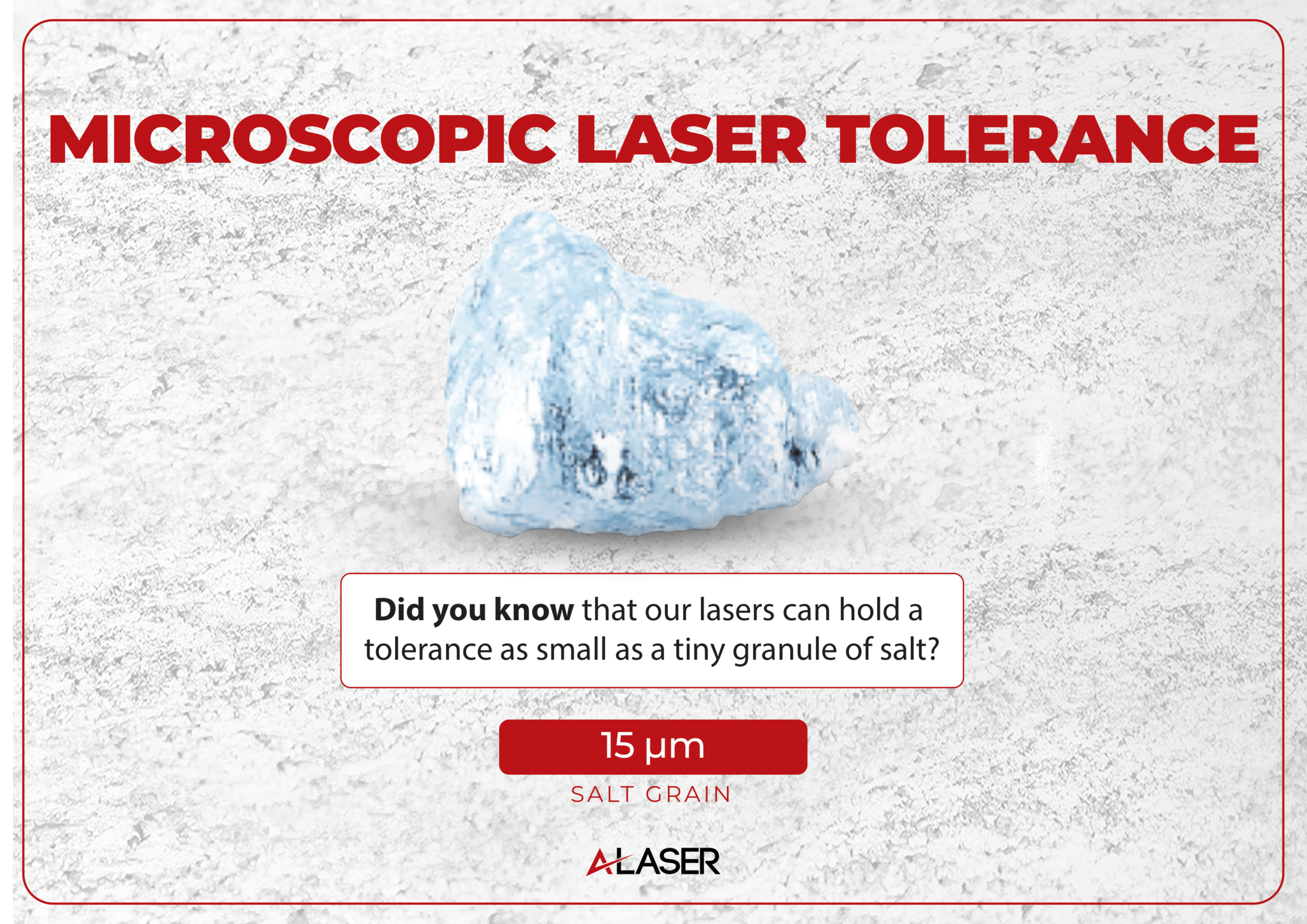
- Post Laser Processing Considerations: Metal alloys are especially prone to needing additional post laser processing to remove micro burrs or enhance the surface with electropolishing, anodizing, or painting. Etching will remove material while anodizing and painting will add material. These requirements need to be known before manufacturing so adjustments to the cutting program are done to compensate for these chemical processes.
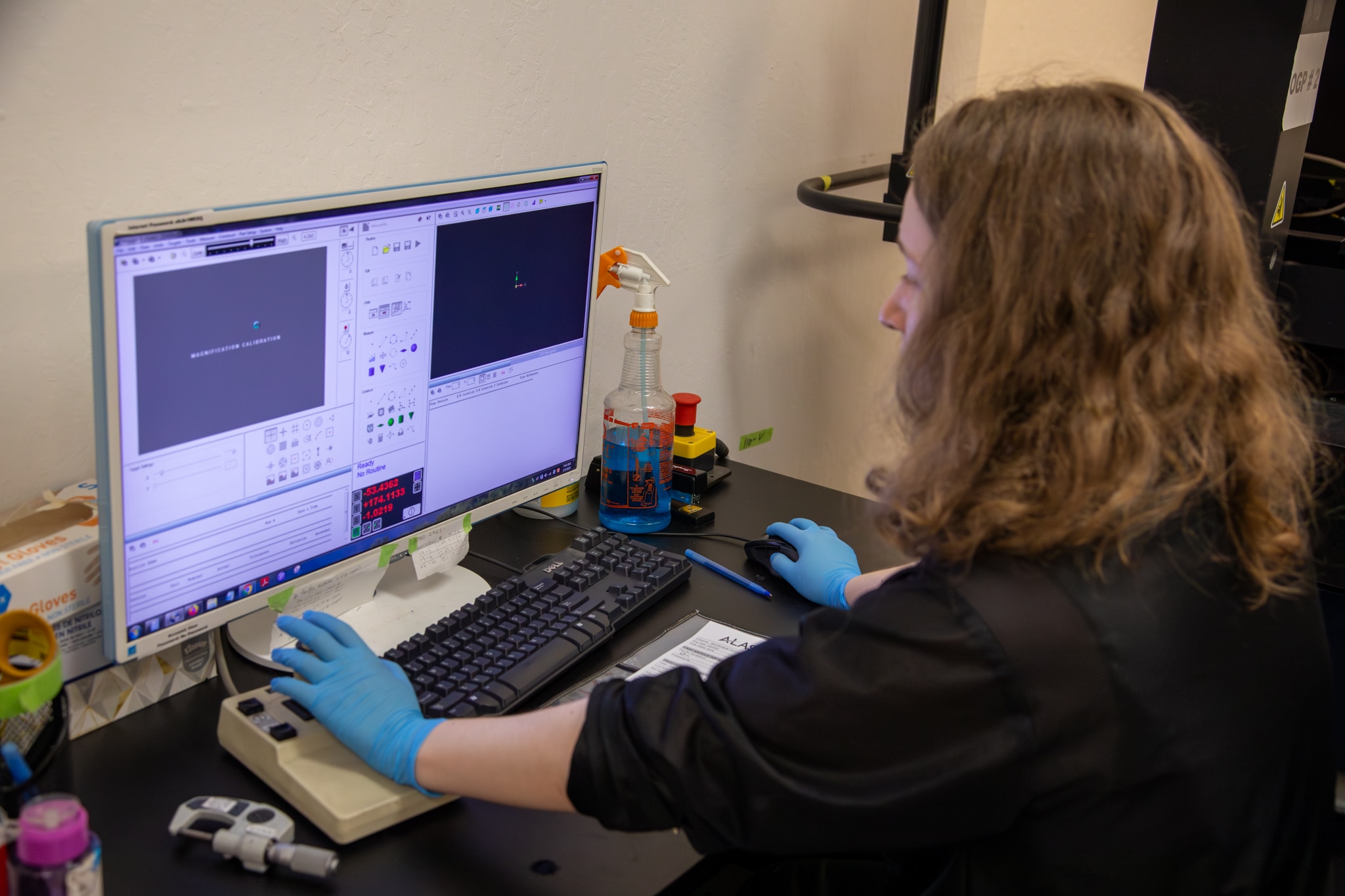
Conformance Through Inspection
Laser manufacturing adheres to various levels of inspection to ensure the highest quality standards are met. The First Article Inspection (FAI) is a detailed assessment of the initial unit produced, verifying that it meets the specified requirements and serves as a benchmark for subsequent production. Acceptable Quality Levels (AQL) involve inspecting a statistically significant sample from a production batch to determine the quality level. AQL is typically chosen for large volume productions where 100% inspection is impractical. On the other hand, 100% inspection involves scrutinizing every single part and is used when a higher degree of certainty is required, often for critical components. First and last inspections involve checking the first and the last pieces of a production run, ensuring that quality is maintained throughout the manufacturing process. Choosing the appropriate inspection level depends on factors like the criticality of the components, production volume, and the quality requirements of the end product.
Conclusion
Designing for laser cutting necessitates a meticulous approach to material selection, feature limitations, and precision requirements. By understanding the capabilities of laser systems and communicating effectively with service providers, one can optimize material usage, lock in tolerances, and ensure conformance through rigorous inspection protocols. These strategies not only enhance the efficiency and cost-effectiveness of the manufacturing process but also guarantee the production of high-quality, precise components. Ultimately, the key to successful laser cutting design lies in thorough planning and collaboration, ensuring that the final product meets all desired specifications and industry standards.