Capabilities Cutting Gaskets, BGA Test Adapters, & More
Known most popularly as Kapton, polyimide is popular amongst numerous customers and industries A-Laser supports. The advantages of this material with its electrical insulation characteristics, flexibility, availability in multiple thicknesses see it being used in forms as simple washers and gaskets to complex flex circuitry. UV laser systems, utilized by A-Laser, cut polyimide with well-defined edges and consistently hold tolerances of +/- 0.001″ (.0254mm). Patterned geometries with features as small as 0.050” x 0.100” (1.27mm x 2.54mm) at a thickness of 0.001″ and 0.002” (.0254 and .0508mm).
Suppliers of socket connectors and BGA Test Adapters frequently request dense arrays of apertures. Patterns with hole diameters of .020” (.508mm) with .010” (.254mm) spacing is very common. The arrays vary greatly, but all require consistent sharp walls and tolerance being held as close a .0005” (.0127mm). Using varying thicknesses, these alignment tools aid the insertion of fine pins. Stack-ups vary by use and function.
Flex circuits are just what they are called, but they need a different process to form the final PCB board profile. Instead of milling and routing, laser cutting of this ultra-thin circuitry is a fine fit on a UV laser. Smaller profiles of a few millimeters in area are just a few of the project demands we see. Rigid-Flex too is continuing to be needed for many consumer products and commercial use. The nature of a flex circuit is well suited for laser technology when the production rolls forward. Much of the “Real Estate” of such projects do not give any room for error for the manufacturing line. With minimal distances of .004″-.005″ (.1016-.127mm) from the profile, could not be achieved mechanically. These are held to a tolerance of +0.001”/-0.000” (.0254/-0.000mm). Another advantage is that the UV laser process cuts both rigid and flex assemblies with no mechanical stress to the boards, no vibration, and very minimal heat effect. Imagination and solutions for projects is what mechanical engineers strive to look for when seeking our support.
Masks and shims and often are cut in combination with an adhesive. This type of stack-up has been a proven solution for filling a gap or masking key areas during a secondary process. The need for such “basic” parts can play such a vital role. Whether the need is for a small mask of only 0.080” (2.032mm) in size or up to 24” (610mm) in size, UV lasers can consistently hold tighter tolerances than most manufacturing methods, as small as +/- 0.0005” (.0127mm), allowing designers to have confidence. Application of conductive inks are also used for the stability and accuracy and is repeatable and scalable for manufacturing.
Gaskets needed for their high performance in Aerospace applications or their use in the medical industry as a miniature flexible seal, will continue to be in demand. Defense applications also require and demand that stringent tolerances be held. The environment can be harsh, and performance is key. The reliability and ease of manufacture of such laser cut designs with straight walls and holding to tolerances that exceed beyond what die-cutting can provide, laser cut solutions are here. Coupled with UV laser technology un-matched quality can be achieved and often is the best choice for critical geometries that support the demands of today’s technical advancements.
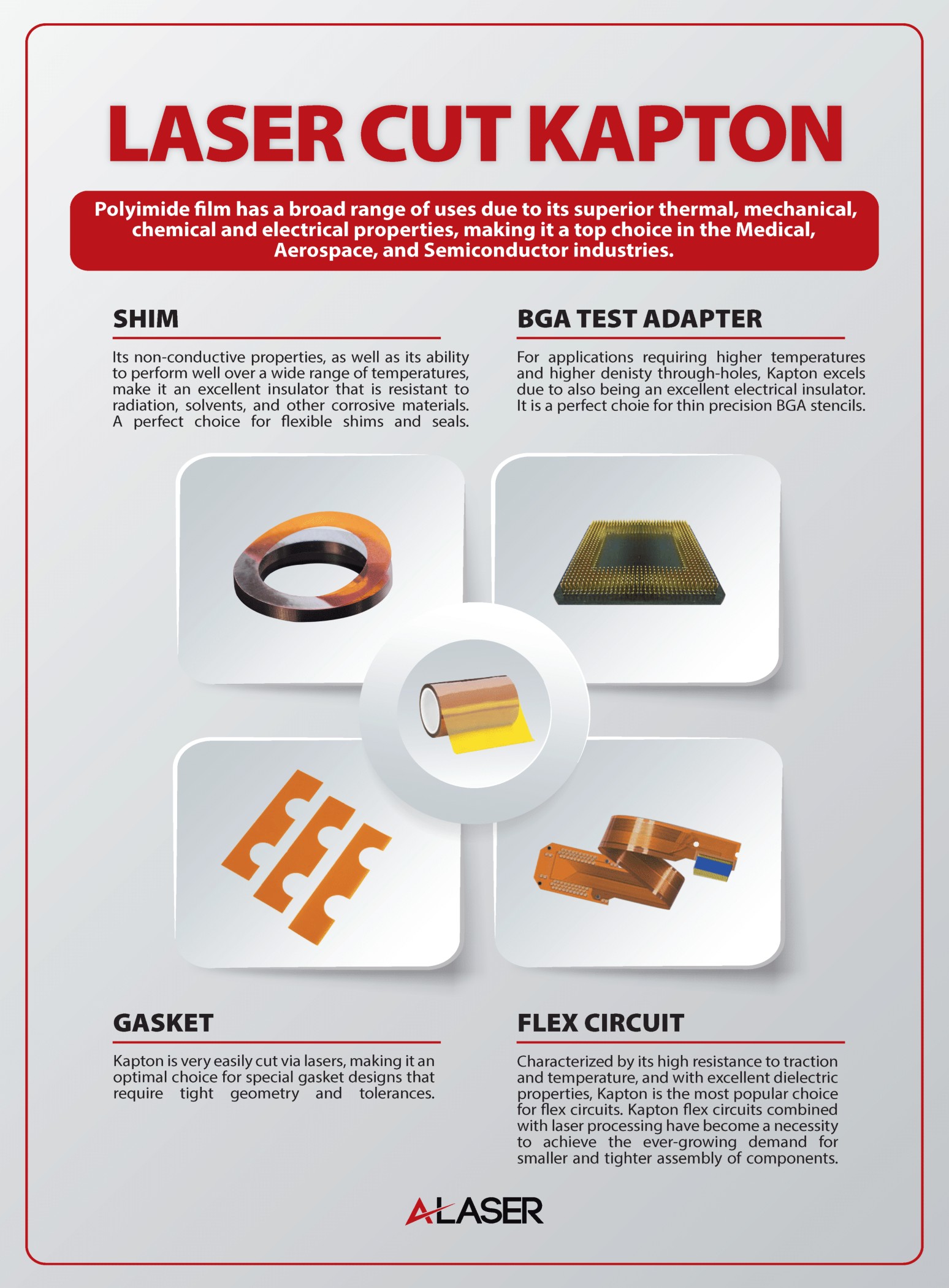