The Benefits of Stainless Steel
A little-known fact about stainless steel is that it was invented all the way back in 1913, more than one hundred years ago. Because of its resistance to rust, stainless steel was adapted for surgical tools between 1919 and 1923. Even today, the many remarkable qualities of stainless steel make it a useful material across a variety of applications and industries. I thought very little about stainless steel prior to my entry into the precision parts industry. Back then, I was just beginning in customer service, making sure the customers’ orders were input correctly, and the jobs done on time. The material for stencils then was stainless steel. Typically it was an alloy called 302/304 FH, for “full hard temper”. The thickness range then varies; 3-8 mils thick in most cases. I learned in processing stencils that thickness had a big impact on the success of the stencils in use. Thinner stencils meant a thinner layer of solder being applied to the bare fab, while thicker stencils meant a heavier deposit. The type of components determined the thickness needed. The industry is still in force today and is necessary for surface mount applications. There are new technologies coming on, but this method and material will likely be a strong choice for many years to come.
As I moved deeper into the precision parts field, I realized that the usefulness and demand for stainless steel were greater than I realized. That’s one of the perks I like in this industry of support. We get to see the very cool new directions that popular technologies take; of design and how companies are working to solve problems in industries such as health, medical devices, defense, consumer, food and many others. There are numerous alloys of stainless steel with each having different properties of hardness, tensile strength, distortion, elongation etc. There are numerous suppliers specializing in bulk material, rare alloys, thin gauges, rolled material and flat sheets. Some come with certificates of conformity, or C of C’s. Others are off the shelf and used in many instances for R&D work.
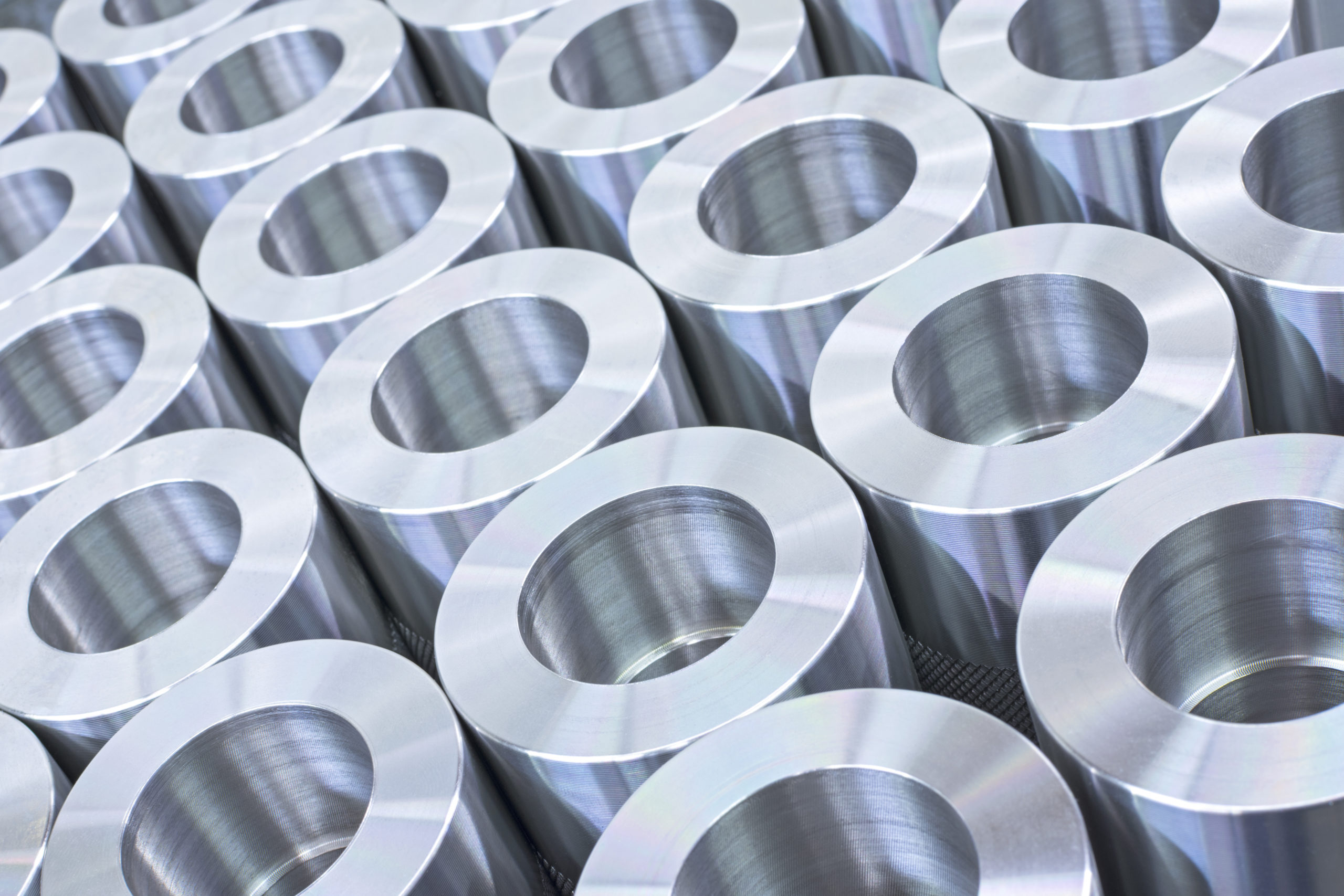
In the past, I have had the pleasure of working with a large company, mainly in their Life Sciences division. It was highly critical work, sourcing the exact alloy and precisely cutting the geometry. The project was fulfilling and possibly enhanced millions of people’s lives around the world. It was amazing to be able to think that I was there in the middle of it, helping see the project to fruition, working as part of the solution, with material that I had not given much thought for years.
At A-Laser, I have had the opportunity to be involved with medical device projects in both R&D and full production. Stainless steel plays a part in much of the fascinating work I do. I love mechanical engineering and seeing the parts we design and manufacture with stainless steel be used in the medical devices we help produce. We are not just a chop shop now, we have a key place in support and must also make sure the requested material is suitable per the design request. The right material for the function is crucial. Not all requested materials are made for the thickness needed. For that reason, it is important to know the product and do research beforehand to ensure that we use the right material for the job, at the right specifications. Being proactive and knowing the industry helps to prevent frustrations that may arise from not having the correct materials on-hand. The collaboration of any service provider should support the multitude of new challenges for this rapidly changing world that we live and work in.
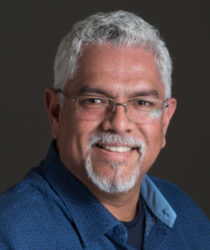
About the Author
Joe has been part of the A-Laser team for over 10 years and has extensive experience with laser cutting technology, sales, and customer service. Joe was born and raised in San Jose, CA and has resided with his family in Gilroy, CA since 1997. The unique projects he gets to learn about and the industries they support, keep everyday new! His hobbies include photography, he is a member of the Morgan Hill Photography Club, hiking, model building and collecting vintage camping lanterns and stoves. His favorite places include Mount Lassen Volcanic National Park, Portland OR, and Boston MA.