How to Reduce Edge Burrs in Precision Laser Cutting
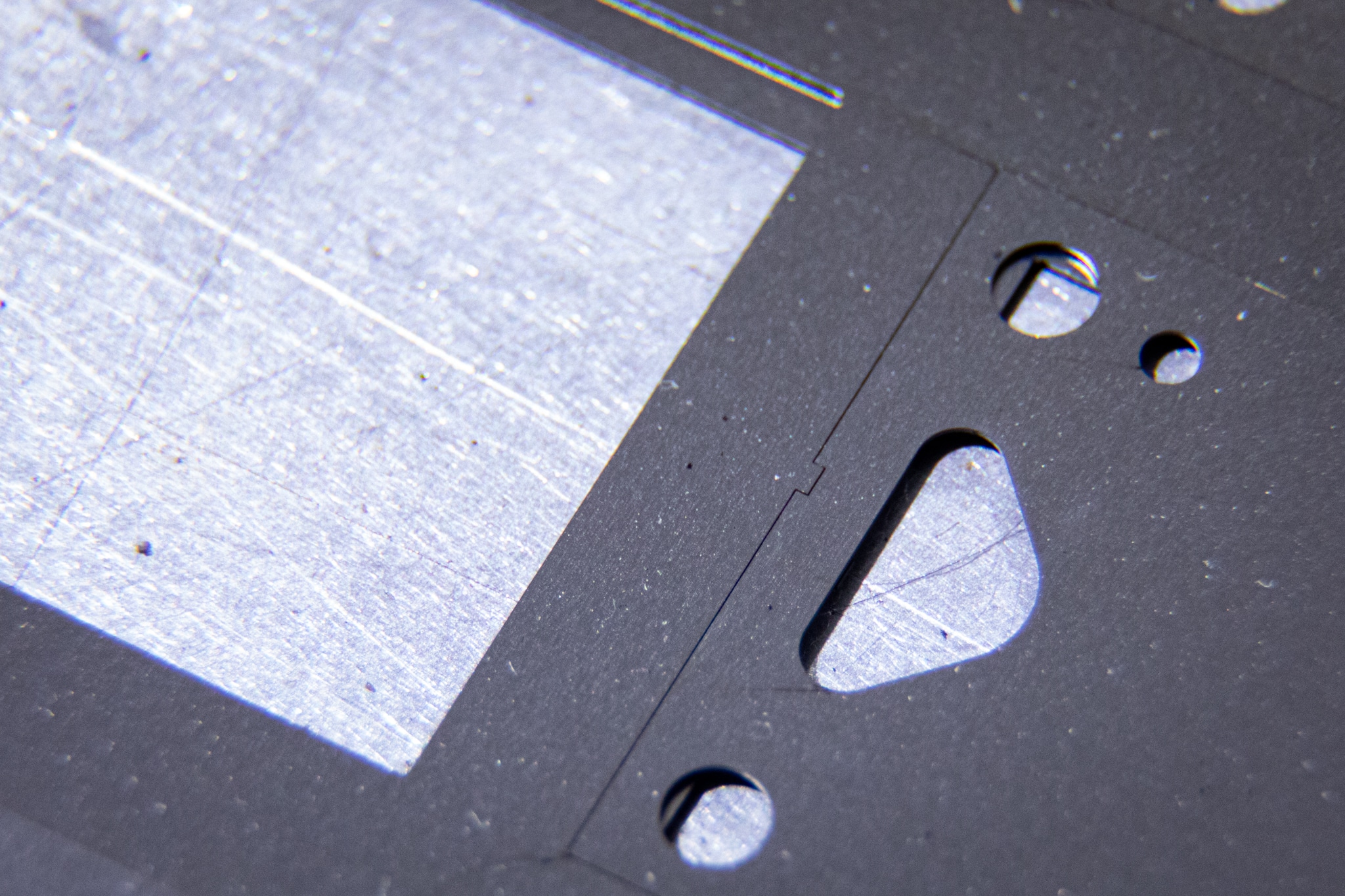
Burrs are the result of laser cutting and reducing edge burrs in metal parts is an ongoing element that laser manufacturers solve. They do this by implementing a series of procedures and recommendations to the design of the intended part and having knowledge of what materials will work best. Producing a precision component that has undergone a series of design iterations with prototypes and testing, is not usable in most cases if edge burrs are present on the final product. This can be detrimental to the function of metal parts. To counter this, edge burrs can be controlled by several factors including through the process of laser cutting, by post finishing processes, the material used and the design of the part, or a combination of some or all of these factors. Burr free laser cutting is both in part a science and art form as experience and technical knowledge are combined to produce some of the finest and most accurately made metallic precision components in use today.
Designing For Laser Cutting
One of the key elements in manufacturing a laser cut part out of a metal alloy is the design of the part. This not only means the cut profile of holes, slots, radius, and overall part size, but it includes the material to be used. Material choice is specified by the customer to meet the requirements of the parts’ use and function. Metal alloys like stainless steel come in different grades of hardness, thickness, and in sheets or rolls. Not all grades however are made equal. What is available in one thickness may not be in another grade. This knowledge is where your experienced laser cutting service provider can help in sourcing the appropriate raw material or advise when another grade or thickness is a better alternative. The design of any potential manufactured part will have constraints based on the capabilities of the laser cutting machine. Going beyond these can cause issues that can result in burrs and even warpage of areas due to heat affected zones or HAZ. To minimize design issues, keep these guidelines in mind:
- The Smallest Features: Not all laser cutting machines or providers of services are equal, but for a example the smallest holes sizes using an ultraviolet laser for up to 10mil thick metal alloy will be 0.08mm and for thicker than 10mil cut on a fiber laser it will be a minimum of 0.13mm or larger. On laser systems such as picosecond and femtosecond, these will have the capability for smaller holes diameters, but also be confined to cutting ultra-thin foils, but only through materials that are a few microns in thickness.
- Choice of Material: The intention of designed metal alloy components is to surpass older technology or be part of a new directions in advancements in industries with critical requirements, supporting needs for health, transportation, communications, defense, and consumer products. Some metal alloys can be more prone to stress, burrs and HAZ, especially for designs where features are concentrated. Examples of this would be screen or mesh cut areas, features cut in thicker grades, thus needing more laser passes and or more power applied to cut. Materials with a higher thermal threshold like tungsten, titanium, nitinol, copper or nickel are good choices if suitable. When there is no choice, as in using 304 stainless steel, for example, adjusting laser parameters (laser tool) can be a solution.
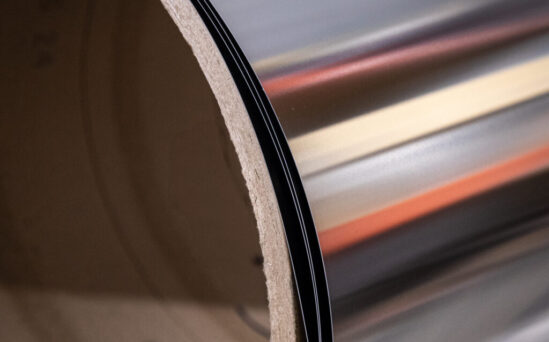
- Spacing Of Features: Using the same guidelines for the minimum hole size can also be applied to spacing of features. However, repetitive features such as slots and thin slits in the metal can weaken the structure and cause vibrations and burrs to occur during the laser cutting process, due to pressure from assisted gases like oxygen and nitrogen. To counter this, the use of tabs may be needed. Tabs are made in widths from 2-10mils, depending on the material thickness and the locations can be critical to the final result. To remove these tabs a secondary cut is done. It is recommended that tabs locations be confirmed by consulting with the laser manufacturer.
- What Does HAZ Do? HAZ (Heat Affected Zone) can occur when burrs are present and even occur when there are no burrs. This is due to areas of the metal sheet or foil that heat up beyond the alloys upper thermal threshold. For concentrated aperture locations or when the metal thickness requires more power to cut through, warpage can result and produce a non-conforming part. Burrs can be reduced and sometimes eliminated, but warping of the substrate cannot be overturned. If burrs do occur, any HAZ issues will be discovered during FAI inspection (First Article Inspection) and addressed accordingly for a change in the laser cutting process.
Designs of new metal components often require revisions that remedy any design issues found in the early stages of development. Once approved for laser processing, the next steps are to reduce the possibility for slag and burrs while on the laser with a series of adjustments to what is called the “laser tool”.
Laser Tool Adjustment
You have designed the part to be within the capabilities of the laser cutting machine, so all should go forward without a hitch, correct? In many cases yes, but to keep burrs from forming, the laser may need to be adjusted during the cutting stage with adjustments to the laser cutting tool. Multiple adjustments are made on the laser that include the laser power or wattage. Too much power may burn the material or cause burrs and HAZ. Not enough power may not cut through thoroughly. Adjusting the laser cut speed also will keep HAZ from forming and is done in combination with the number of cycles or also called laser passes. The proper wavelength may need to be refined as well, including the dwell time of the laser. Adjusting the laser beams focus will reduce slag formation, thus increasing the quality of the cut edge. Some laser systems will use oxygen, nitrogen and other gasses to assist in laser cutting of metal alloys. These and many more refinements once locked in are called the laser tool and this is saved for the duration of the production run and for future use.
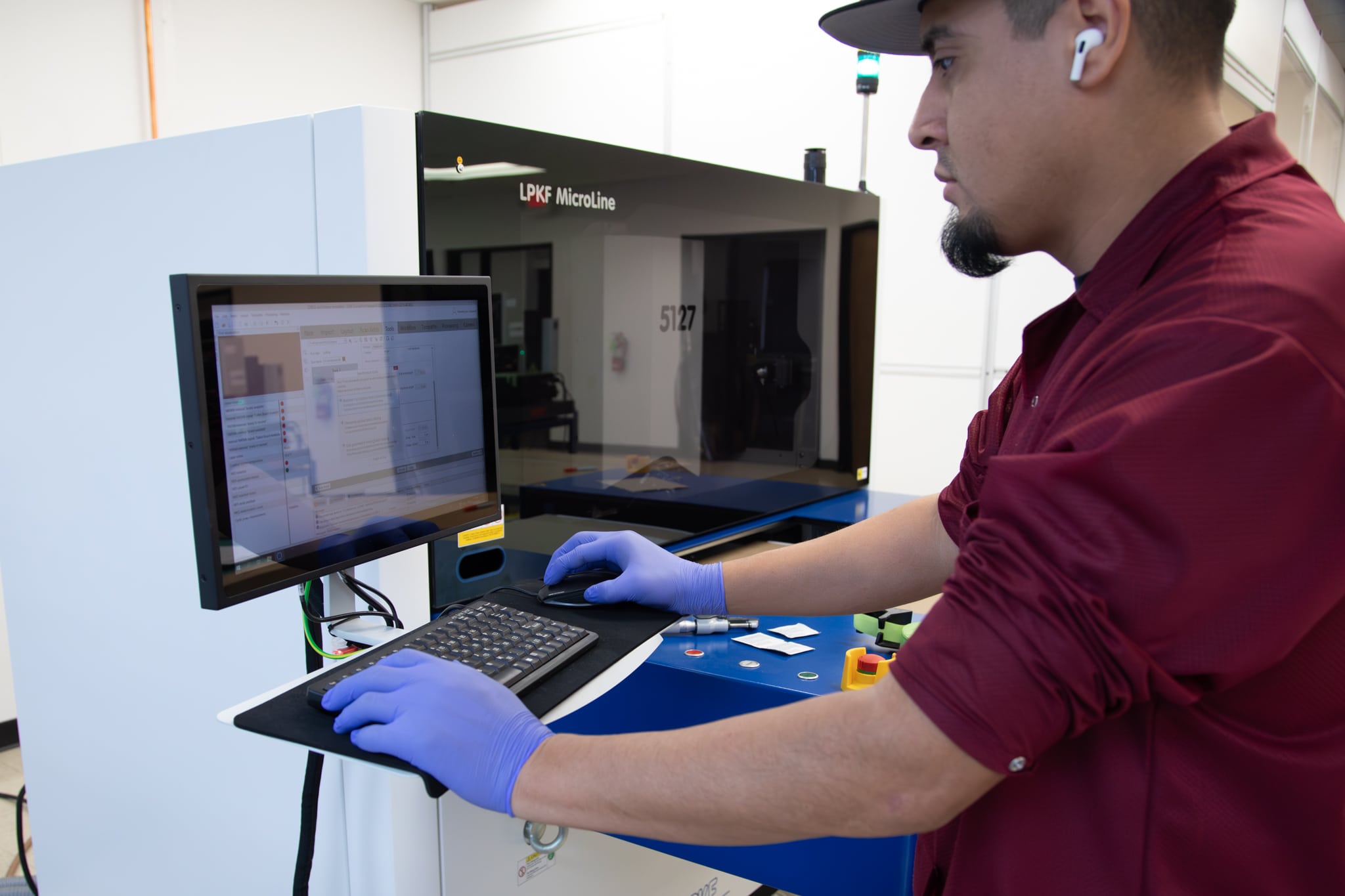
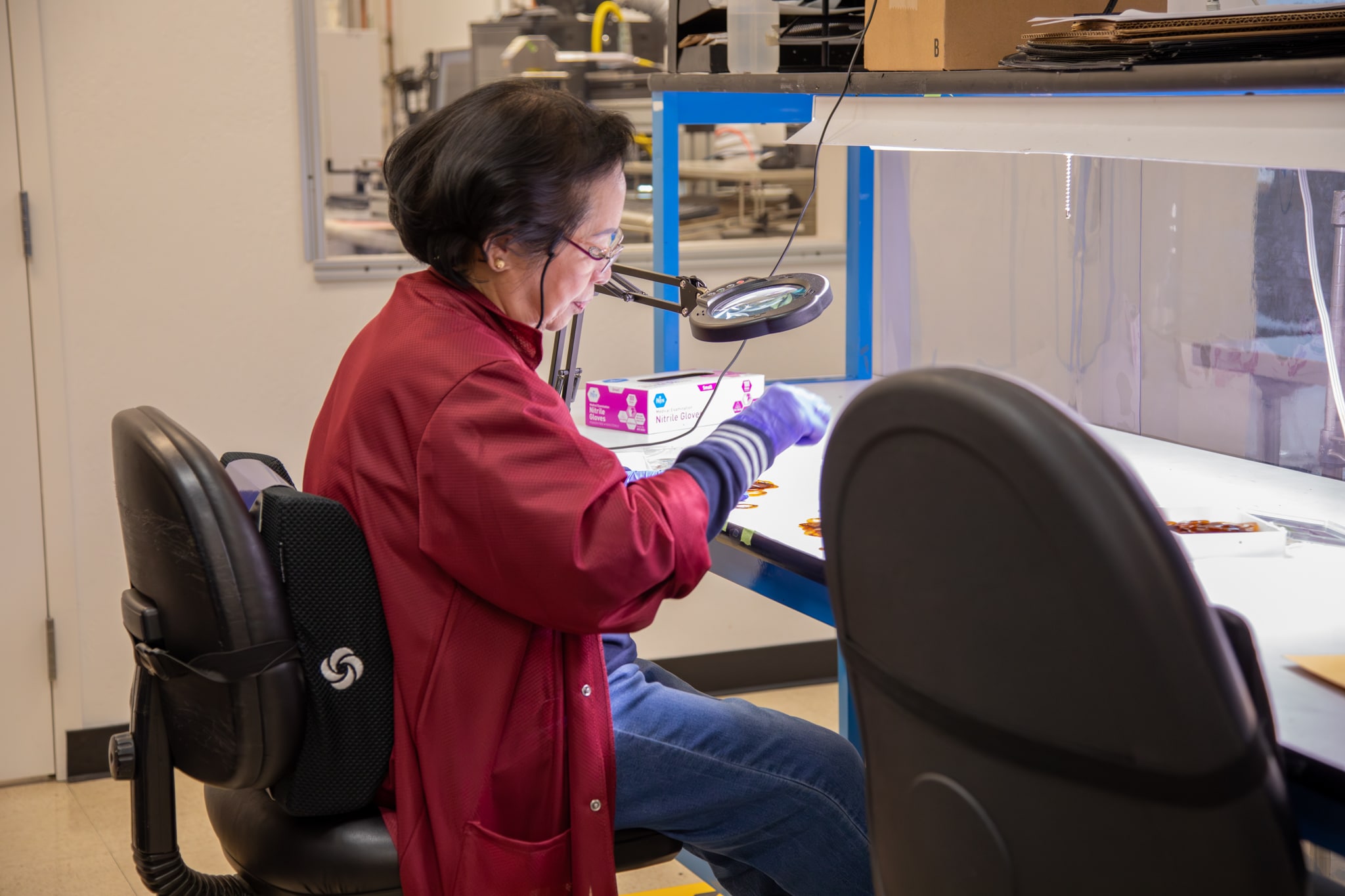
Post Laser Finishing
The final step in burr free laser cutting may need support from post finishing processes. This may be done in-house or with an approved third-party provider. Post finishing are methods such as sanding of the metal sheets, or with parts tabbed in, or sending out sheets or single parts for other processing like tumble deburring. Listed here are methods used widely to remove burrs:
- Sanding: This will take several steps using smaller and smaller grit size from 800 grit size to 2000 or higher (the smaller the number, the larger the media. Smaller media size refines the surfaces). This can be a manual process or assisted by machines but is more labor intensive than other methods.
- Tumble Deburring: Using mixed media to subject the metal parts in a barrel tumbler or an agitation bin. This method reduces burrs and slag and can also polish the surface depending on the type of media used. Caution must be used when tumbling thinner delicate parts as they may be damaged by deformation in the process.
- Electropolishing: Using a chemical bath subjected to an electric current will give the surface a clean polished look and remove smaller burrs.
- Chemical Deburring: Sometimes called micro-etching, this chemical solution also removes burrs and will smooth the laser cut edges. Chemical processing also needs controls as it can remove too much material, thus altering the parts profile and size of the cut features. Laser cutting can make adjustments if it is decided that the chemical deburring will be needed, by adjusting the cut features to be smaller and letting the final etching process create the required feature size.
For post processing to be efficient and practical, smaller parts require the design for manufacturing to have tabs that hold the parts in place on the sheet or metal foil, during the laser cutting process. Tabs are also needed when sanding is the desired method to remove edge burrs. The tab locations can be very crucial to the parts’ function and performance, so it is highly advisable for the customer to approve the tab locations. Tabs will be in width from about 2 mils to 4mils on thin metal foils and between 5-10mil in width for metals cut at 10mils in thickness or higher.
Conclusion
Maintaining a burr-free edge in precision laser cutting involves a combination of initial tool adjustments and post-processing techniques. While laser tool adjustments such as power, speed, wavelength, and dwell time are critical for minimizing burr formation during cutting, post-finishing processes like sanding, tumble deburring, electropolishing, and chemical deburring further refine the quality of the edges. Each method has its unique advantages and may be chosen based on the specific requirements of the project. It is essential to consider the nature of the material, the design intricacies, and the final application to determine the optimal approach. In essence, while the methods discussed provide a robust framework, flexibility and customization in technique are paramount for achieving the best results in precision laser cutting.