Determining the Right Plastic Cutting Process
Plastic cutting machines, like those used and run by laser service providers, can produce extremely diverse and complex plastic components that are part of devices and systems from consumer products to highly critical needs medical devices. Imagine a new line of medical devices that required intricate, custom-shaped plastic components. These precision parts would interact directly with human tissue making precision paramount, and any imperfections could compromise the devices’ efficacy and patient safety. Traditional cutting methods, like CNC machining or water jet cutting, while effective for many applications, cannot guarantee the level of detail and cleanliness required. A plastic cutting machine is a tool designed to cut plastic materials into specific shapes and sizes. Powered by laser technology, these systems can be solutions that are unmatched by other methods. It’s a versatile tool used in various industries in manufacturing, while smaller and simpler systems are used for arts and crafts and hobbyists. Laser cutting is a manufacturing method that has gained tremendous popularity over the past 30 years and continues to advance in capabilities as technology itself advances in all sectors of manufacturing.
Proven Technology Within the Details
Although not all laser types are suited to cutting plastics, the ones that do have specific materials that are processed into precise geometries for not only the medical industry, but for all facets of consumer and industrial uses. Environmental concerns of plastics have been discussed in parallel with the use of these materials as it is harder to break down over time and presents a large percentage of waste in landfills. As new methods and agreements to recycle plastics have made great strides in this area, new types of biodegradable plastics are being researched. As progress in recycling grows, so does the need for new products. To bring new ideas into reality, product designers, mechanical engineers and other professionals are using laser technology to review prototypes and support long term volume manufacturing. They move forward with intention of using laser technology for characteristics that the laser plastic cutting machines have such as:
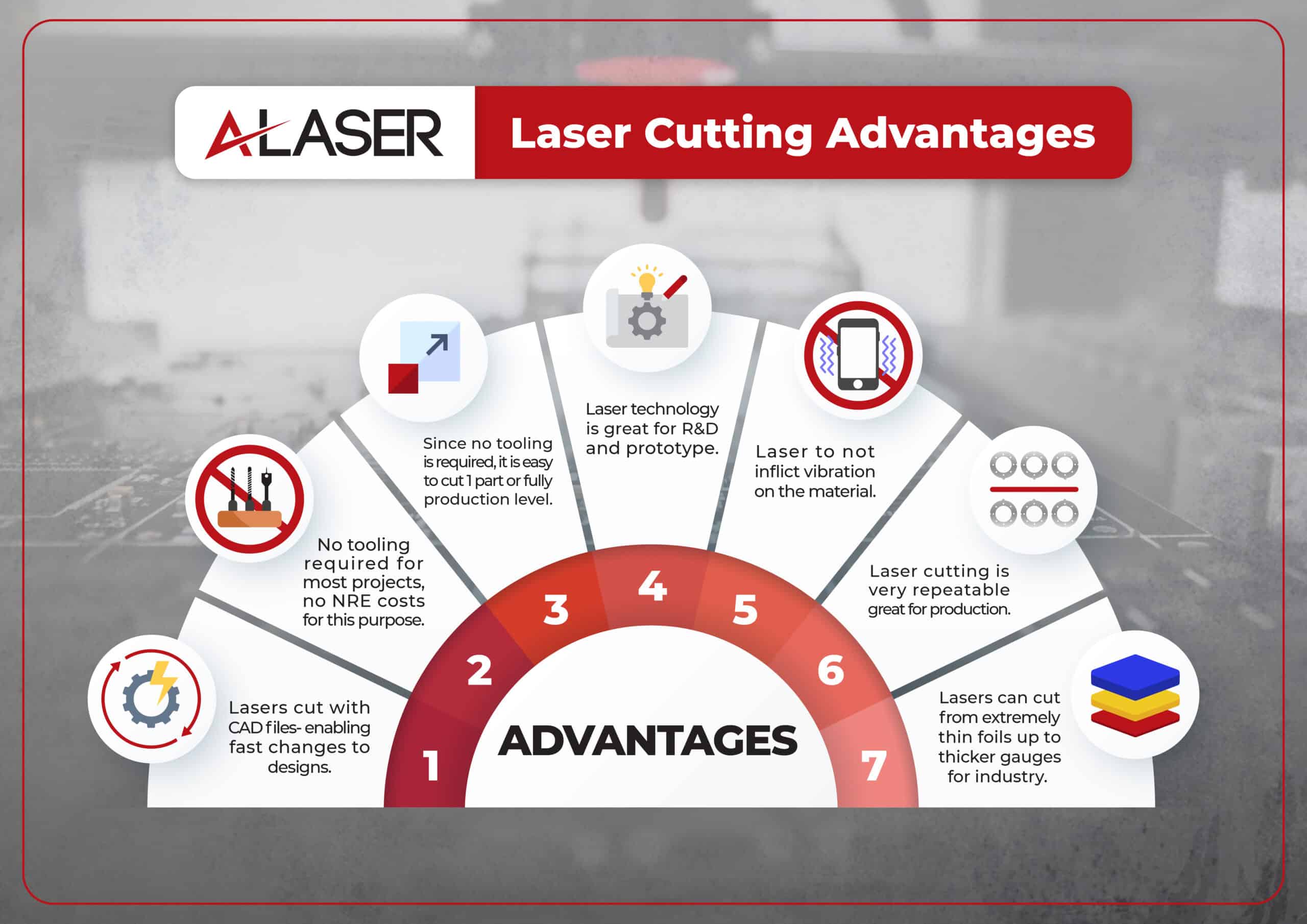
- Intricate Designs and Fine Detail:
- Laser cutting excels at creating intricate patterns, fine details, and complex shapes that would be difficult or impossible to achieve with other methods.
- For medical devices, aerospace, battery energy, communications, semi-conductor processing and many other sectors, demands for precision are foremost.
- Clean, Burr-Free Edges:
- Laser cutting produces clean, smooth edges without the need for additional finishing processes. This is crucial for many precision components.
- Minimal Material Waste:
- Laser cutting allows for precise cutting, minimizing material waste. This is especially important for expensive or specialized plastics.
- Variety of Material Compatibility:
- Laser cutting can work with a wide range of plastic materials, from acrylic and polycarbonate to more specialized grades on extremely flexible sheets or thicker varieties with and without an adhesive backing.
- Rapid Prototyping and Customization:
- Laser cutting is well-suited for rapid prototyping, allowing engineers to quickly iterate on designs and test different configurations. Rapid iteration assists in keeping project schedules intact when changes to a design occur.
- It also enables customization of components to meet specific needs.
Other methods like waterjet cutting or die-cutting do have a solid foundation in cutting plastic materials ranging from simple shims, gaskets, to insulators and mesh components, to name just a few. For a clearer understanding of available methodologies to cutting plastics the following section gives more insight.
Plastic Cutting-The Larger Picture
As mentioned, laser technology is varied in the types of materials that can be cut. For plastics, two of the best are ultraviolet or UV laser systems and CO2 lasers. The ultraviolet wavelength is great at cutting polymers and polyimides, mylars and Peek. CO2 laser systems have the capability to cut acrylics, polycarbonates and other types. Other manufacturing methods are used to cut plastics and establish a broader range of available cutting options as shown in the following table:*
Cutting Methods | Plastic Material Processed | Technology Used In the Process |
---|---|---|
Laser Cutting | Peek, Polyimides, Polymers, Mylar, Acrylic, PETG, Ultem | UV or ultraviolet beam of 20micro or less. CO2 Gas -beam diameter of 75microns or more. |
CNC Technology | Acrylic, PVC, Polycarbonate, ABS | CNC Milling, CNC Drilling-using cutting bits that are rotated at high speeds. |
Waterjet Cutting | HDPE, Polycarbonate, Acrylic, UHMWPE, Polyester | High pressure water- focused through nozzles. |
Blade Cutter/Knife Cutter | Fiberglass, Vinyl, Polypropylene, | Blade under assisted manual or hydraulic pressure cuts through larger sheets of plastics |
Die-Cutting | Ultem, Vinyl, PETG, Teflon Polyester, ABS | Steel die cast into the desired shape and geometry. Good for high volume. |
*Many more plastics are available for each technology mentioned above. The list shown are examples of some of the most popular.
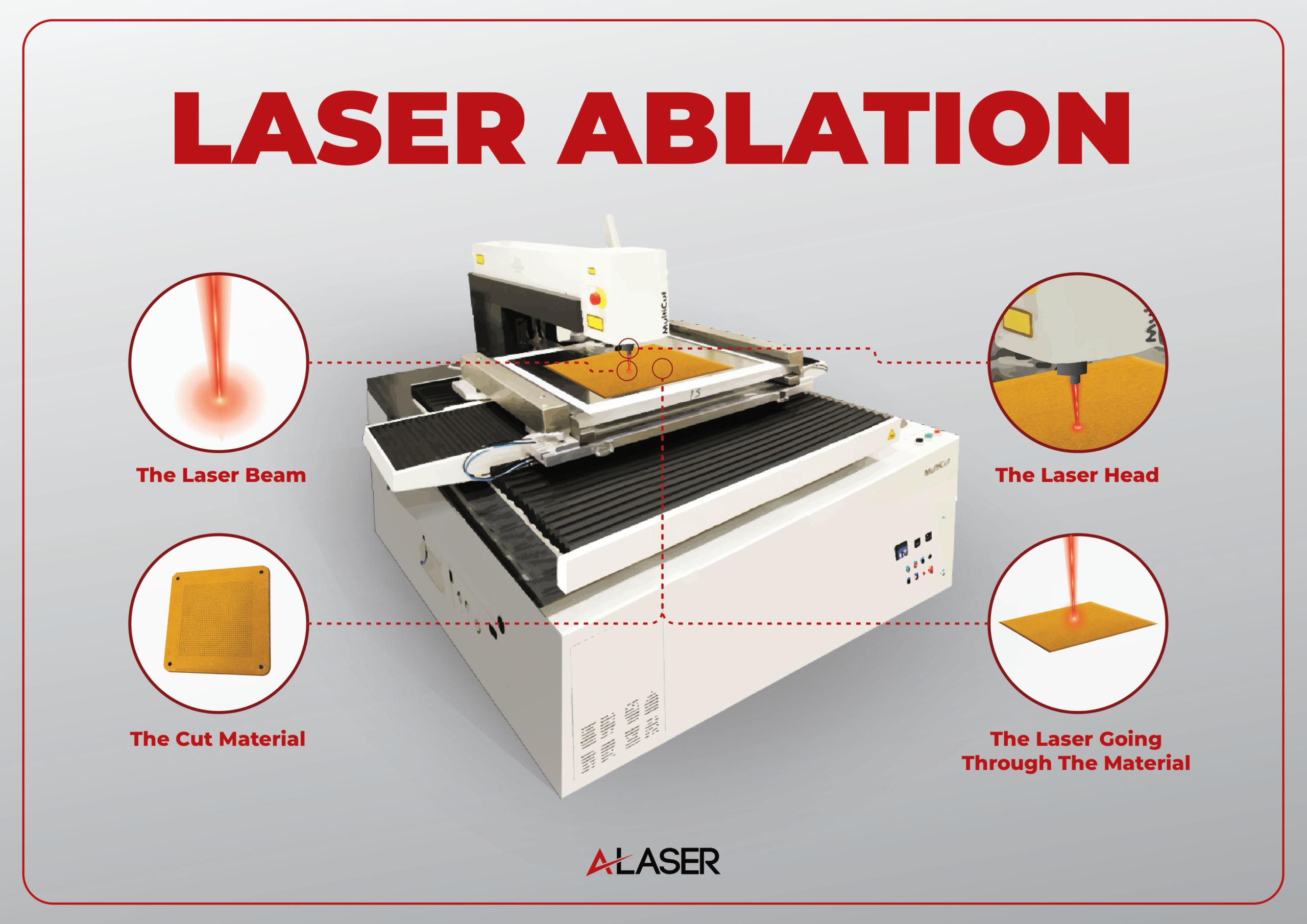
Standing Alone or Teamwork?
In manufacturing there is often a collaborative effort that brings together multiple disciplines that form the final product and for laser manufacturing of plastic components, many times, this holds true. You might see a device with a machined housing made from aluminum by CNC technology and spacers made with die-cutting, and flexible components made with laser technology. The assembly takes enormous amounts of coordination from one supplier to another, forming a supply stream and leads into volume manufacturing. Of course, there are standalone components made from every manufacturing method including plastic machine cutting, that support small quantity demands up to large scale operations with quantities in the hundreds of thousands or perhaps millions of units. The decision is made with all the details and factors to steer each project to the best process available that meets the requirements. Plastic cutting machines serve that role when other processes cannot produce the needed precision nor handle the plastic material without inflicting damage to the plastic surface. By consultation with experienced service providers, a better understanding and determination of the best way to produce your plastic part will save time and cost resulting in greater satisfaction.