The Importance of High-Precision Components
Precision parts are a need for many projects and uses in all kinds of industries. Most people not involved in manufacturing never think about what it takes to produce the technology and devices used by us every day. We rely on the innovations and collaborations of talented individuals to keep pushing forward technology. Fortunately, my profession in manufacturing, gives me privilege to be exposed to fascinating projects. One project at a time, each part manufactured allows me to be part of the growing technological advances, at least in a small way.
A factor that drives the innovation is the material and how it is to be used. One of the unique materials we see at A-Laser is Grafoil. The sealing characteristics, unlimited shelf life and high surface conformity are a superior fit when manufactured by laser.
Gaskets for instance, used in semi-conductor processing are vital in the production stream. The uniformity of the cut profiles for parts ranging in size from 11.500” inches OD x 9.75” ID to 19.600” ODx17.75” ID, are a requirement when used in such conditions. Tolerances held are as small as +/- .001” mil. Utilizing a beam diameter of 20um, this kerf creates well defined sharp edges, straight walls, and consistent cuts. Whether a simple or complex geometry, a shim can be vital in the functioning of mechanical devices. Requiring more durability, shims from stainless steel reinforced Grafoil, have proven to be a welcomed solution. From sizes of .250 O.D. up to 5.40 O.D., and a tolerance of +/- .001” mil is providing reliable long-term use.
Gaskets in support of the oil, automotive, nuclear and gas industries highly need reliability in their products. Gaskets in sizes from .500” O.D. up 18.600” O.D are being held to tolerance of +/- .001” mil. Another area being supported is EMI shielding using precision cut parts. EMI shielding plates out of 10 mil thick grade and holding to a tolerance of +/- .002” is a sample of how this bridging of materials and technology can benefit this industry and can be a great plus for electronics contract manufactures.
The advantages of laser technology allow for gaskets being used for thermal management such as for thermal electric elements in the medical device industry. Because of the increasing demand for smaller footprints, faster speeds, and thinner overall size in electronic devices, more projects are steering towards a laser solution that can fill that gap and become part of the supply chain.
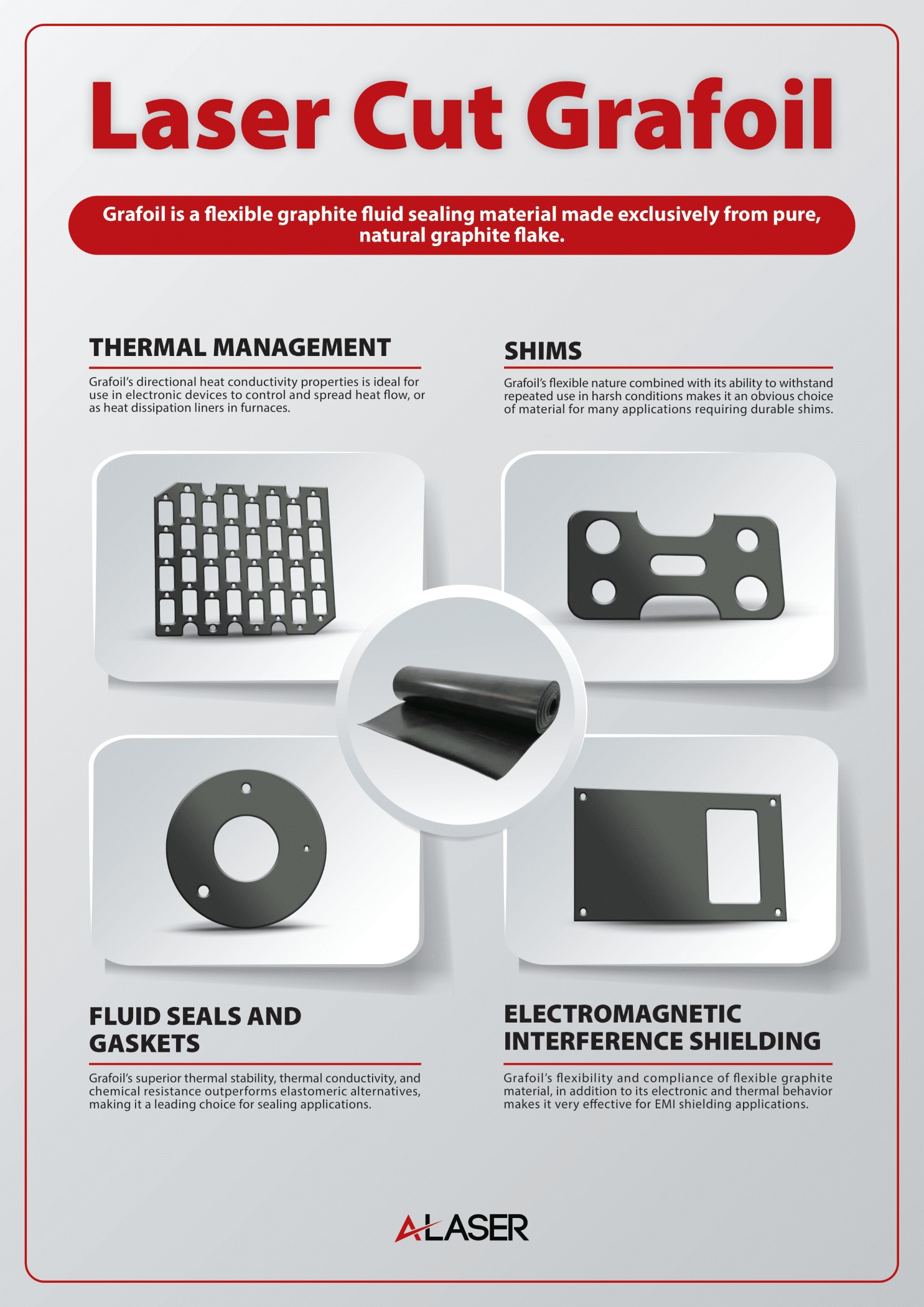
Options available to OEM’s, Contract MFG or other suppliers of essential parts are leaning increasingly to laser technology. An idea and concept provide the spark for R&D. With support and collaboration progress is made to NPI and hopefully to production. Consider the technology best suited for the application for the assigned material. All the before mentioned geometries are cut with a 20um UV laser beam diameter. This creates repeatability and can be a great fit for quality and function. Let us have a discussion to move your project forward.