The Science Behind Laser Systems
Firstly, to understand how laser systems work and how we can do machining parts manufacturing we must understand what a laser is. The word “LASER” is an acronym that stands for Light Amplification through Stimulated Emission of Radiation. Let’s unpack what this means.
All atoms consist of a nucleus with electrons revolving around them at different distances from the center. These distances are discrete, they can be one or the other, never in between. These distances are known as “energy levels”. Electrons can move between these energy states but doing so requires a change in energy. As we know energy can not be created or destroyed. Thus for such a change to happen energy must be introduced to or released from the system. When an electron moves down one energy level to another this energy is released in the form of a photon being “emitted”. If a photon is added to the system or “absorbed” by the atom, one of its orbiting electrons will move up an energy level.
Due to these energy levels existing at discrete distances and due to the law of conservation of energy, only specific wavelengths of photons have the ability to cause a shift.
This distance is what determines the wavelength of the emitted photon. It is also the wavelength required to “lift” the electron. When this drop occurs randomly we call it “emission”. By introducing photons of this known wavelength we can “stimulate” this process. This is known as “pumping”.
Electrons in the high energy state could be thought of like spinning plates on the tip of a cane. Each person spinning plates will randomly drop one. If we continually add more people into the room we will have more spinning plates but as one called they will cause a chain reaction. By pumping in more photons we are lifting more “plates”(electrons) to the high energy position. If we try to add too many then they begin to collide and fall in unison. As everything falls together we could describe this as “in phase”, or in terms of waves, “coherent”.
Laser cutting, specifically laser CNC cutting is a technology used to create high precision parts from stock material. Laser cutting is used extensively in the electronics industry where tolerances are tight and accuracy is paramount. This is how precision parts manufacturing work and this is how products are made by CNC machines.
CNC stands for Computer Numerical Control. Which is an evolution of Numerical Control (NC) from the 1940s.
What is laser precision parts manufacturing?
Machining metal parts, specifically infrared laser cutting is the process in which a beam of invisible IR radiation essentially creates a controlled burn at microscopic levels. This burn liberates a small portion of material from the workpiece. This is often described as a “thermal separation method”. In this process, the laser light will be concentrated through optics to increase its utility. The more concentrated the beam can be the more efficient the separation method will be but more on this later. In order to aid the laser cutting process often an “assist gas” will be used. This is a pressurized gas that will help in penetrating the material, increasing the burn rate, and removing waste material. Common gasses are compressed air for regular cutting, pure oxygen for higher burn temperatures, nitrogen for clean cuts with reduced oxidation plus many others for specialized properties. This gas can also have the added benefit of cooling the workpiece just as the coolant in a traditional CNC would.
- Bad data formats
◦ Non-closed polygons
◦ Non-tangential arcs on corners
◦ Badly declared shape definitions
- Unstable power supply
- Internal motion errors
◦ Discrepancies between axes working together
◦ Friction in travel
◦ Unbalanced weight on an axis
- Energy dissipation
- Beam quality
Why Laser Cutting?
Before we dive into this question we must first explore the differences between products made by CNC machines, the differences between traditional CNC milling to laser CNC cutting. Traditional milling operations will make contact between a high-speed tool and a supported workpiece. This tool will generally be of a much stronger compound than the workpiece it is acting on. CNC systems often use a coolant whilst cutting. This coolant serves two purposes one, to keep the temperature down to avoid “work hardening” and two, to remove liberated material from the workpiece. This process leads to the degradation of the cutting tool.
When tools degrade, the final product will be subject to unforeseen defects. Solutions to this have come in the form of water jet cutting and laser cutting. Where these methods are used, the cutting medium is a stream rather than a solid tool. A stream of water molecules or a stream of photons, as opposed to a block of material. Both of these methods drastically reduce tooling costs. Two major drawbacks of water jet systems are containing the water to where it’s supposed to be, away from electrical equipment, and disposal of wastewater after the job.
With laser as your option, there is no waste material from coolant, no scrap tools, and no wastewater. With a laser, there is higher accuracy and stronger repeatability.
By utilizing the science of optics we have the opportunity to focus the beam. This gives us a high-intensity shallow working area or a long working area with a straighter more consistent cut. As light is weightless it can be transferred across distances at a very low cost.
An extra benefit of precision parts manufacturing by laser cutting is that the workpiece does not need to be clamped down in the way it would on a milling system. it often will be but because the material is being cut by photons rather than mechanical methods the clamping force can be much smaller, therefore, reducing setup times.
Lasers will offer the ability to cut much smaller regions due to the beam diameter being so small.
In essence, there are many, many benefits to laser cutting. In reality, it’s process dependent which if laser cutting is right for you. The thing to remember is that lasers are much more versatile than most people know.
Problems Facing Laser Systems
Due to the high precision nature of laser systems, small disturbances can lead to very noticeable issues. When cutting a small entity for example under an area 1 mm2. If the system has a 5-micron oscillation this will be much more noticeable than the same osculation on a large machined part. So controlling the motion system becomes a much more crucial task.
With this in mind, we can look to reduce the cause of these issues. They may take the form of the following:
Bad Data
One of the biggest culprits in bad production is bad data. Generally, we are looking a micron level errors. Without relative experience, it can be difficult to understand the impact a few microns can have on a part. A few microns whilst almost unnoticeable even under a microscope can cause small parts to not fit correctly. For some laser manufacturing processes, a single part will be cut out and inserted into a void in a host material much like the final jigsaw piece being placed. As with the jigsaw if the curves don’t match exactly the part won’t fit.
A danger of materials becoming thinner and thinner is that an inserted part may appear to fit, however, it may not actually sit flat within its space.
Unstable Power Supply
Stable power is crucial in any motion system. Unstable electrical power is analogous to engine knocking in a car. Stable electricity will not only increase the life of laser and motion systems but also maintain the quality of its output.
For many of these issues, a Universal Power Supply or UPS can protect and extend the life of a system.
Motion System Errors
Motion system errors can be broken down into two main categories Tuning and Mechanical. Determining which one is at fault can often be difficult. In general when an error is found mechanical errors will increase or decrease linearly with an increase or decrease in speed. Tuning issues can occur at what appear to be random times. If a system is tuned badly it may struggle to move at 50mm/sec but perform flawlessly at 70mm/sec.
One often reliable indicator is where a mechanical flaw will still present when moved manually with the motion is powered down. Things like physical blocks, worn bearings, seized joints, and such can be felt by touch and then tackled appropriately.
For tuning issues, a good safety measure is to limit the power to a machine whilst investigating. Many control systems include cutoff thresholds for current/power. This should be the first step in investigating issues.
Energy Dissipation
If we take an example of cutting stainless steel. An unfocused beam will not cut through the material. Passing the laser through some optics will allow the beam to be concentrated in a much smaller area. In doing so we create a smaller work area with higher energy. This is described as “energy density”. With a high energy density spot, the laser can begin to penetrate the steel. As this happens small parts of the steel are liberated and then removed by the assist gas.
This process works by adding speed gas at the focal point of the laser thus concentrating all the tools at or disposal. Even with these strategies working together we can sometimes see issues with the energy dissipating throughout the surrounding material. On thin metal cutting, this can cause warping, grain restructuring, and hardening. Whilst this always happens in a limited sense it can be accelerated by an unfocused beam, damaged optics, or degrading beam quality.
Beam Quality
If the beam quality has dropped due to wear and tear this will reduce energy density. This will cause warping of the steel which will, in turn, cause the material to move out of focus from the laser. Clearly, this is a runaway train situation. Problems like this should be tackled early. As Benjamin Franklin once said, “An ounce of prevention is worth a pound of cure”. Even though I prefer the metric system, the analogy stands. Catch issues early and save yourself in the long run.
Types of IR Laser
CO2
CO2 Lasers create a photon stream in the region of 10,640nm wavelength.
Nd:YAG
Nd:YAG Lasers create a photon stream very tightly held at 1,064nm wavelength.
These two lasers differ not only in wavelength but also in maintenance costs, power, bandwidth, reliability, and more.
Fiber lasers (Nd:YAG) will output a beam close to 1,060nm in wavelength. CO2 will output 10,640nm. Why would someone choose one over the other? Mainly this comes down to the material that will be processed. Whilst this would be an entire article of its own. It can generally be thought broken down into metals being suited to the lower wavelength and natural materials such as wood or cardboard being suited to the higher wavelength.
Final Thoughts
It’s difficult to give recommendations in engineering without being vague. Everything we do is unique to each project. Lasers offer control and speed that are unmatched in other methods. Sometimes those other methods are just more appropriate for the job. The main thing that I personally always think is, lasers are just really cool. Technology is all around us today. Lasers are a small part of our everyday life, some for fun, some for manufacturing, and some for science. All of which stemmed from a hypothesis in 1905 by Einstein. One of many thoughts of his that would shape all of our lives.
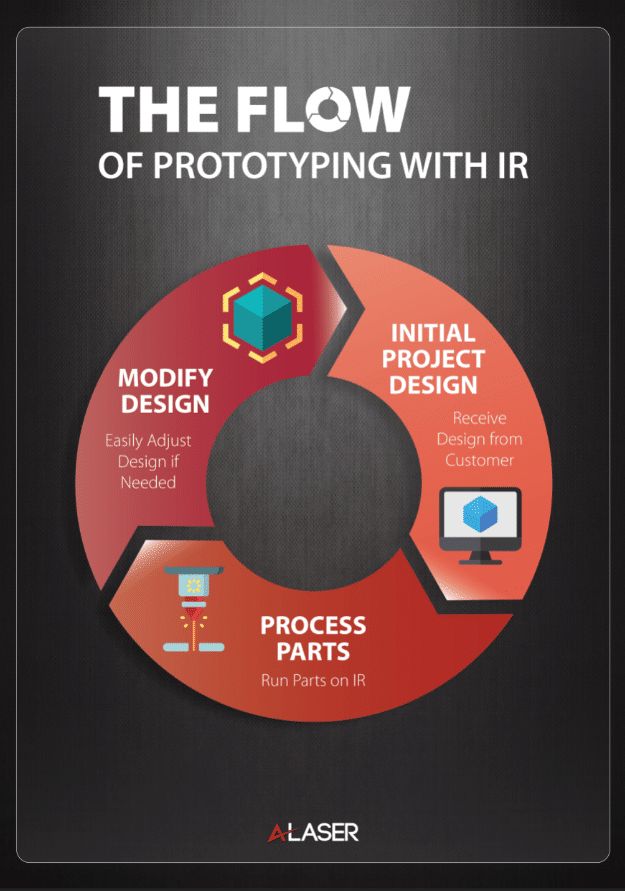