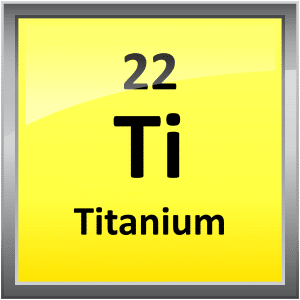
Laser Cutting Titanium
Can you laser cut titanium?
Titanium when it was first discovered and cataloged back in 1791 by an amateur mineralogist named Reverend William Gregor, must have been followed by some sense of wonderment and possible frustrations as it would be over 150 years later until the industrial production of titanium would ensue. Since then, this alloy, with a melting point of 1941K and a boiling point of 3560K, has proven to be highly sought after with uses in critical and commercial industries like aerospace, medical, automotive, science research and many, many more. As it is machined often using CNC technology, titanium sheets or foils are laser cut when the projects details require such methods. Laser processing does have its advantages and disadvantages to cutting titanium. The following guidelines will help determine if laser technology will be a good fit.
Titanium has some unique characteristics to keep in mind:
- It is corrosion resistant: Great for applications that are exposed to harsh environments and chemicals. A good choice for a marine environment.
- It is biocompatible- Used in medical implants.
- Has a high strength to weight ratio- great for applications where weight is a concern.
- Has tolerance for high heat temperatures and can be used where other alloys would show degradation.
Laser Technology suitable for cutting titanium are fiber lasers, Nd Yag lasers and CO2 lasers. The advantages of using laser technology to cut titanium are:
Precision by a small, focused beam: Lasers have very small beam diameters ranging from 10um to 40um in many systems. The creates opportunities for designs that are intricate and other technology would not be able to support.
Cut Edge Quality: and being able to repeat this result over and over. Laser manufacturing can support both R&D and production runs.
Ability to nest parts: Laser set-up can adjust to maximize the number of parts cut from a sheet or foil.
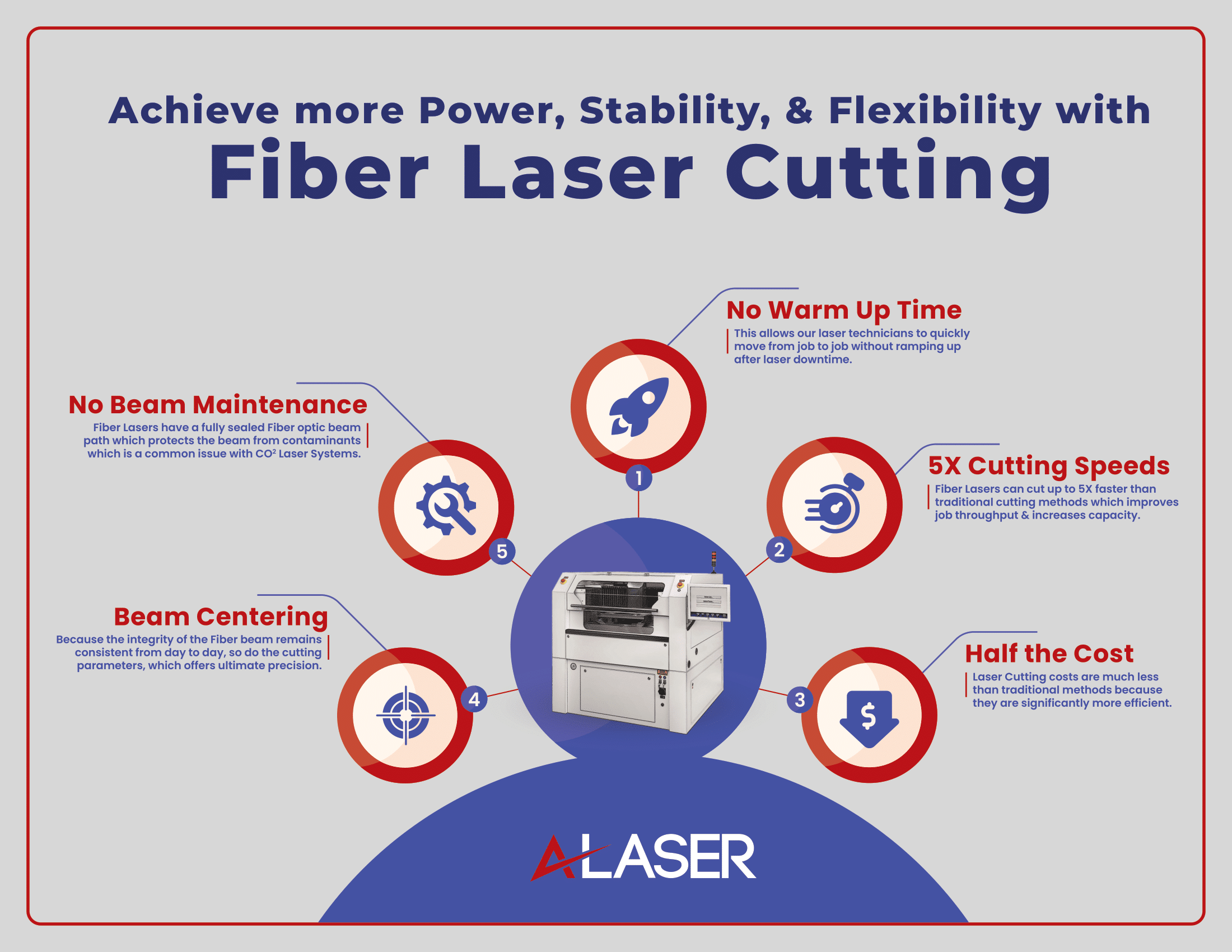
Challenges Of Titanium
Because of the characteristics of titanium mentioned earlier, some of the challenges while cutting are:
- Thickness: Titanium will need higher powered systems to cut through as the thickness increases.
- Oxidation during cutting process: while oxidation can occur on the laser cut edge, this can be eliminated or reduced by using an assist gas like argon or nitrogen.
- Titanium is reflective and like other reflective metals, can damage the laser optics. Adjustment to the laser settings and process are needed during the laser operation and can cause longer processing time.
Titanium can be laser cut and a discussion with an experienced service provider will direct which type of system is best to use considering the characteristics of titanium and challenges that each project brings forth.
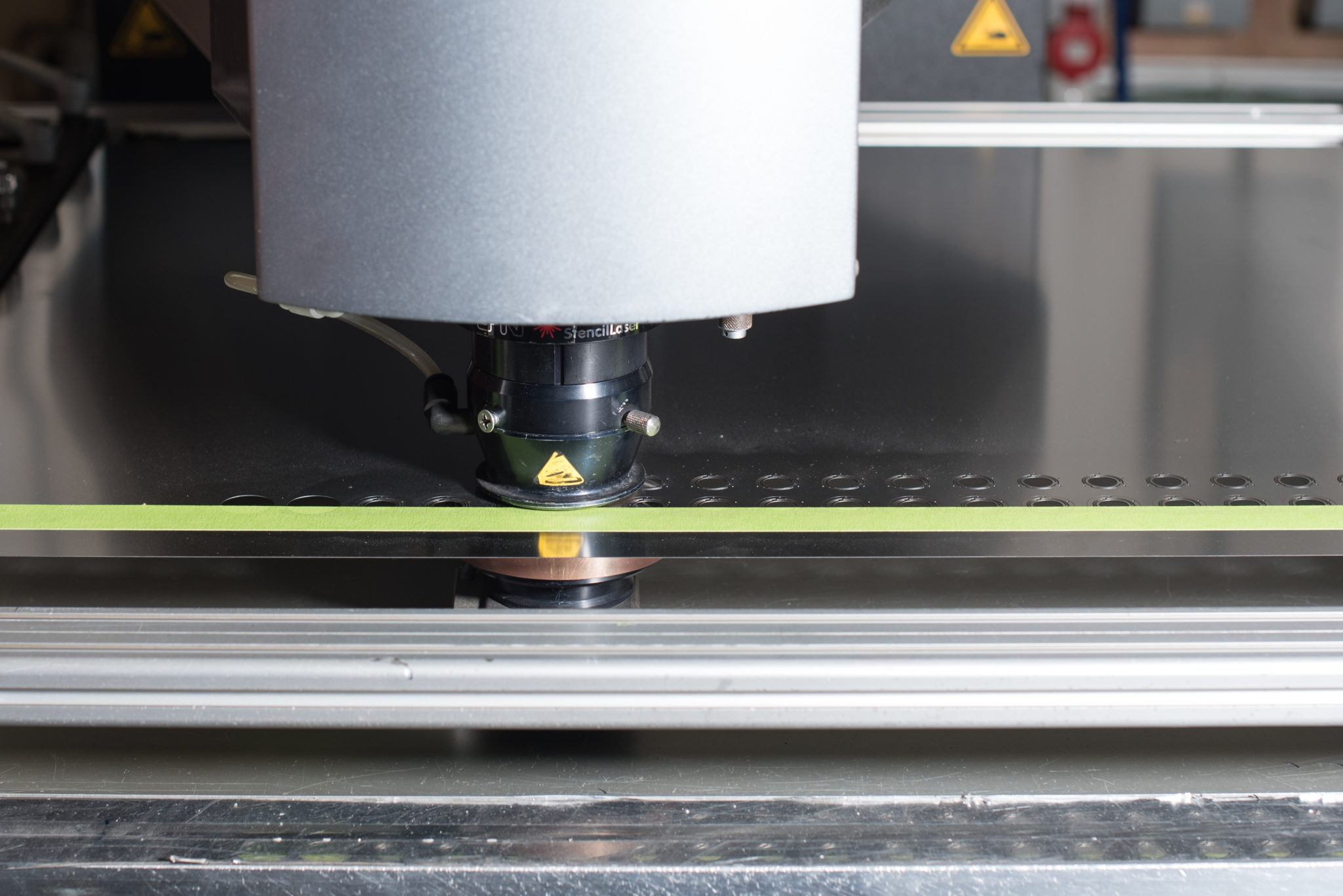
What are the best titanium grades to laser cut?
It would be easy if all manufacturing could use one material and that material would be good for everything. Imagine taking that question out of the equation and all that would be needed is the imagination to create. Whatever is needed in all industries could be made from Alloy “XYZ”. In an imaginary world that is kind cool, but we are ever so far from this occurring. Every material used in manufacturing has found its place and is used so for specific project requirements. Titanium, being one of those special metals, has numerous forms and within this are good when using laser cutting technology.
In its purest forms titanium comes in grades of 1,2,3, and 4. As each higher-grade number increases so does the tensile and yield strength. Not being alloyed, these grades are lighter than steel with a high strength to weight ratio. Projects requiring these characteristics would be used in industry applications such as: medical, aerospace, marine, architecture and chemical processing, for example.
Grade 5 is used very often and referred to as Ti 6-4, Ti 6AL-4V and Ti6AL4V. Sheets of Grade 5 have superior strength and high range of temperature threshold and corrosion resistance. Used also in industry needs for aerospace, medical implants, and environments where potential corrosion is found.
Not to be outdone, grade 9 titanium is an alloy that includes aluminum and vanadium. Sheets of this have increased strength, weldability, and corrosion resistance. Offering more flexibility to designs for uses in sporting goods, aerospace hydraulic systems, marine environments.
The best grade of titanium for laser cutting projects is going to depend on the degree of factors such as: strength to weight ratio, temperature threshold, the environment that the parts will be subjected too, the corrosion resistance needed, will the parts need welding after and what industry will this be for? Consultation prior to design and manufacturing with experts will assist in guiding the best material choice.
How to laser cut a Titanium sheet
Laser cutting titanium is a wonderful method to produce precision parts. Like other metallic materials titanium has its characteristics to which if aware of and properly set-up procedures are done, a very high degree of satisfaction will be accomplished. The cost of titanium is higher compared to stainless steel. Therefore, acquiring the right sheet size is needed to limit overspending. Nesting of the design to maximize the number of parts per sheet will limit waste. Once confirmed with the size of the sheet the following steps are taken to laser cut titanium.
All laser systems use a CAD file to run the desired cut path. This includes the nesting of the array of the parts maximized for the sheet size. CAD files typically come in formats such as a dxf or AutoCad Step file. This is loaded into the system and programed to cut the design profile including cut holes, slots etc.
The set-up of the titanium sheet:
-
- Grain direction- Some parts have crucial requirements to the grain. The sheets must be orientated to cut in the desired direction. This is important for parts being subject to bending or forming post laser.
- Careful handling of the sheets to avoid injury as metallic sheets are sharp.
- Proper placement to avoid scratches and contamination prior to laser processing.
- Securing the sheets thoroughly- The laser cuts with a focused beam of high energy. Uneven material will cause an errant cut and reduction in quality.
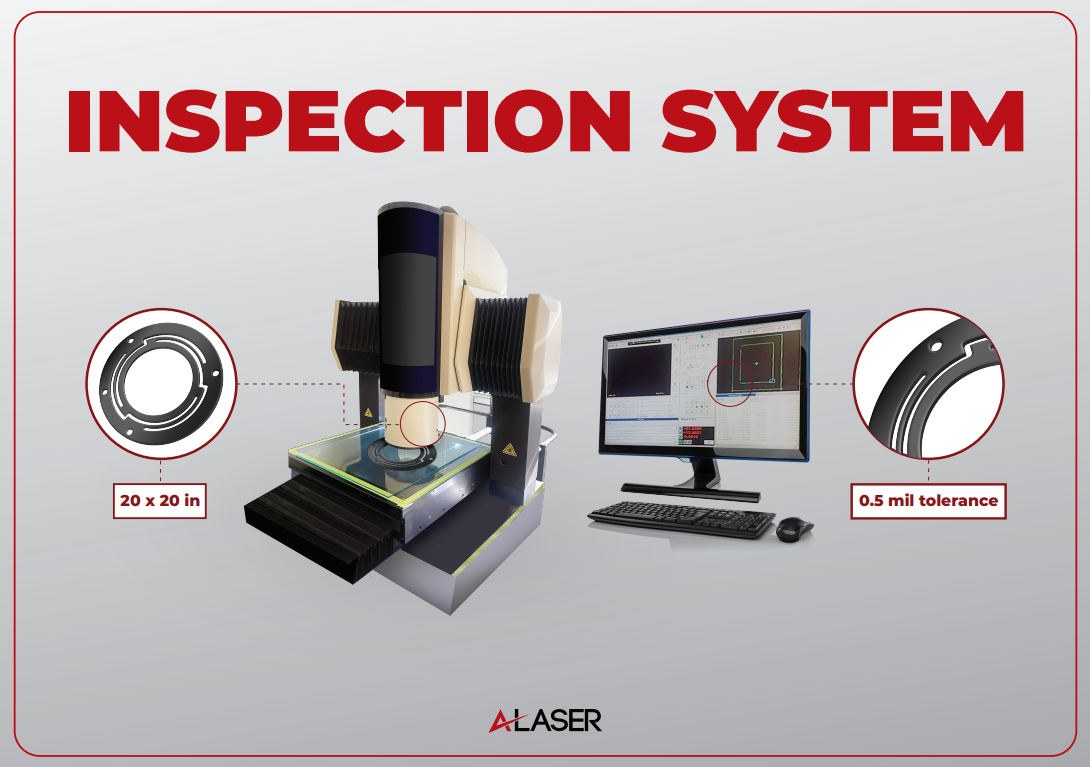
First Article Inspection: An initial run is performed using the CAD file along with settings on the laser called the “laser tool”. Because titanium is reflective, it can damage the laser optics. Additionally, an inaccurate or lower quality cut edge can result. The F.A. inspection is done on a qualified inspection system, for example an OGP or Optical Gaging Product. If found to not be in spec to the parts print and requirements, adjustments are made to:
-
- The speed of the laser cutting, measured as millimeters per second.
- The power of the laser in wattage.
- The number of laser passes.
- The dwell time or delay time? How long the laser stationary before moving along the next laser pass.
- If needed a second F.A inspection is done to approve the production run.
- Production Run: This is the easy part- The material is in place; the file has the maximized quantity per sheet and the laser tool is adjusted to maximize quality.
Final Inspection: As in all industries and manufacturing, a proper Quality System must be in place to ensure that the customers’ expectations are met. Quality inspection of the completed run will be checked at the required inspection level. This can be as simple as inspection of the first and last parts or higher AQL level and CPQ inspection.
Final Cleaning and Packaging: Depending on the project additional cleaning is done. Care in handling precision laser cut parts is needed to keep them from damage. Some methods used to secure for shipment: Gel-paks, foam boxes, sleeved parts with lint free paper.
The steps of laser cutting titanium varies per service provider and the laser system being used. It is important to have these discussions with your service provider. Do they routinely have machines calibrated? Do they have a training manual and have examples of past projects? Asking these questions will give you confidence that your project will result in high quality and satisfaction.